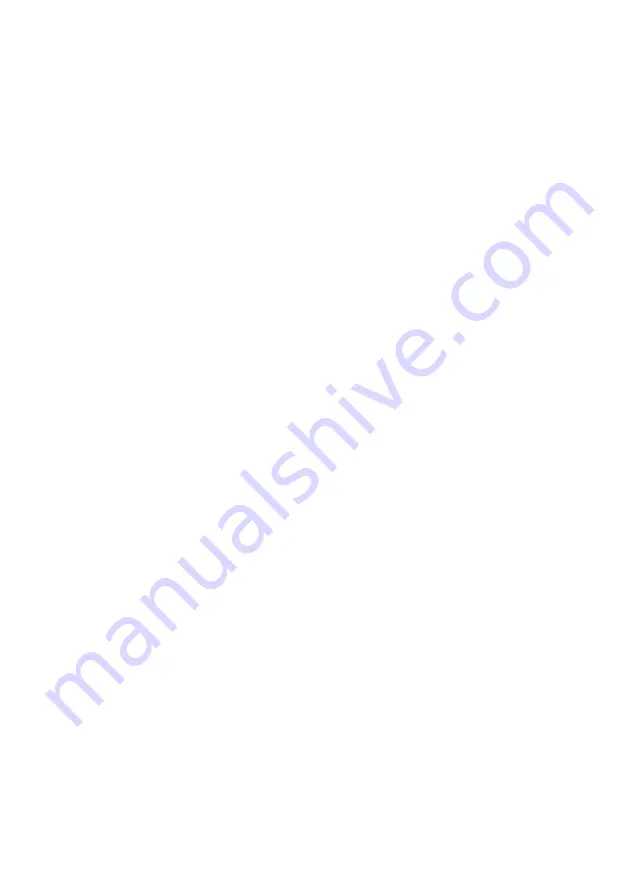
7
3. weldinG plastic pipes
3.1.
Technology description
When performing sleeve welding with
the help of heating sockets on the heating
element, pipe joint and profiled part are
lapped. Pipe end and sleeve of the pro-
filed part are heated with the help of heat-
ing spigots and sockets, installed on the
heating element, and then joined. There
are two methods of sleeve welding with
different sizes of the spigot and sockets.
Method A does not include mechanical
tooling of pipes, method B includes me-
chanical tooling – centreless grinding.
Heating spigots and sockets ZENIT are
intended for method A welding only.
Sleeve welding with the help of heating
sockets can be performed on pipes with
diameter up to 63 mm.
When working with pipes of bigger diam-
eter it is recommended to use an appropri-
ate welding machine.
3.2.
Prior to welding
Follow recommendations of the pipe man-
ufacturer and profiled part manufacturer!
End of the pipe must be cut square and
evenly. These parameters are achieved
by using pipe shears. Besides, end of the
pipe must be beveled for easy joint. Right
before welding pipe end and internal sur-
face of the sleeve of the profiled part and
heating spigot and socket, if necessary,
are cleaned with a piece of paper, leav-
ing no paper dust or a napkin leaving no
filaments, moistened with gasoline or
commercial alcohol. Make sure plastic
remainders don’t stick to the surface of
the heating socket. When cleaning heat-
ing sockets make sure not to damage spe-
cial teflon coating. Do not touch surfaces
treated in this way before welding.
3.3.
Welding technology
3.3.1. Heating of pipes and profiled
parts
To heat the pipe and profiled part quickly
insert them on heating spigots, fixed on
the heating element of the machine, to the
end position or to the marking, and keep
for time required (see welding table).
It is recommended to follow instructions
of the pipe manufacturer.
When heating, the heat gets inside the sur-
faces to be welded and Во время разогрева
тепло проникает в подлежащие
спаиванию поверхности соединений,
доводя их до нужной температуры.
3.3.2. Welding and fixing
After heating remove the pipe and pro-
filed part from the spigots of the heating
element and push them inside one another
without turning. Fix (hold) them for a pe-
riod of time, recommended by the plastic
pipe manufacturer (see welding table).
Time between removing from the heat-
ing element and welding must not exceed
time, recommended by the pipe manufac-
turer (see welding table). Otherwise weld-
ing surfaces will not be heated enough for
quality welding.
3.3.3. Cooling
Load on joints must be applied only after
estimated cooling time (indicated by the
plastic pipe manufacturer), (see welding
table).
4. maintenance
ATTENTION! Before maintenance and
repair disconnect the tool from the power
source and let it cool! These operations
must be performed by qualified specialists
only.
Before every welding clean the teflon coat-
ing of the heating element spigots with a
Summary of Contents for PPW-2000
Page 1: ...Instruction manual Plastic pipe welding machine PPW 2000...
Page 2: ......
Page 9: ...9...