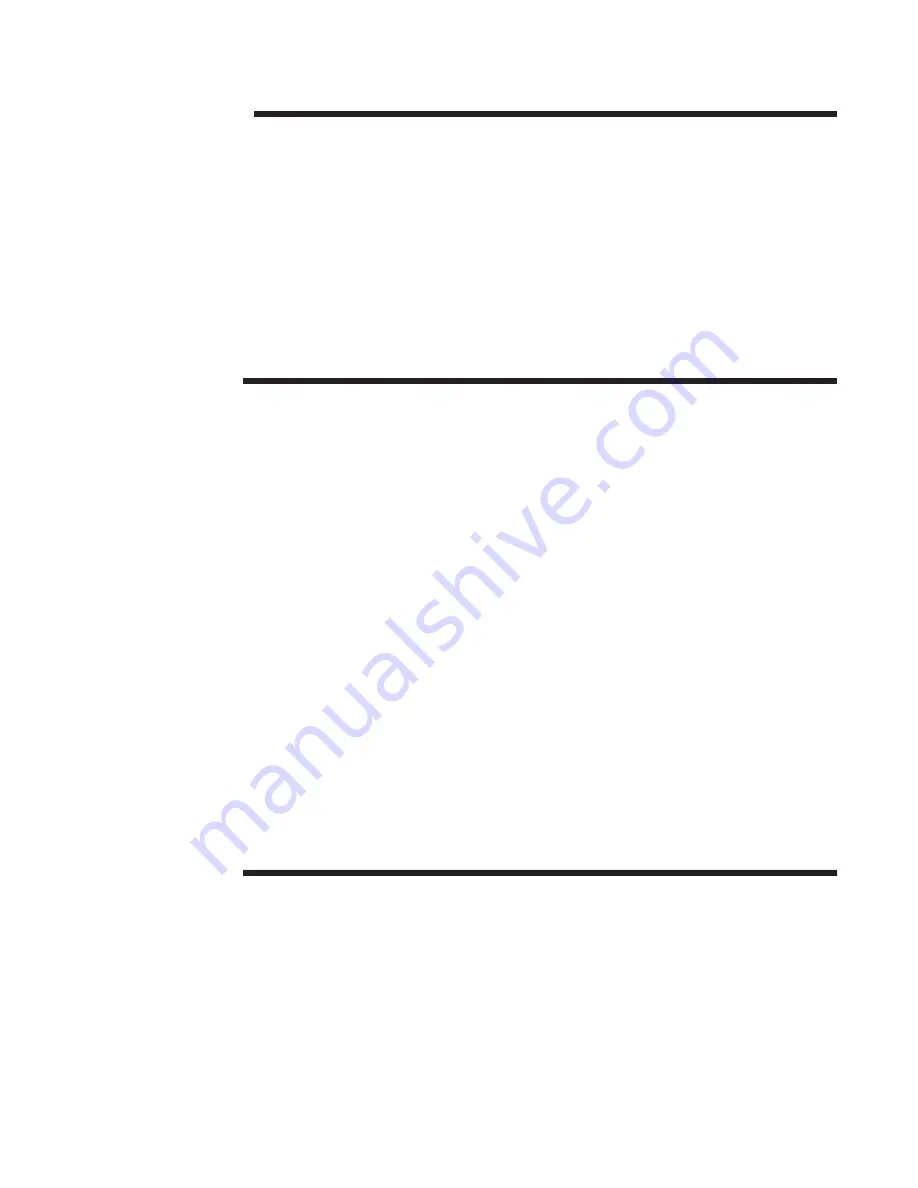
Zenith
®
Pumps
2
Thoroughly read and understand this entire manual
before installation and operation of pump.
Benefits
Specifications
Capacities:
0.16 to 750 cc/rev.
Operating Speed:
10 - 90 rpm on most extrusion processes depending upon
process parameters
Differential Pressure:
Up to 5,000 psi (345 bar)
Body Pressure:
10,000 psi (690 bar).
Temperature:
To 645° F (340° C),
(950° F maximum with special fasteners and seals).
In 1926, Zenith Pumps was approached
by the synthetic fiber industry to design a
pump to provide a precise, pulseless, and
repeatable flow and assure better quality
control.
Since then, Zenith has provided
pumps for virtually every polymer utilized
in the plastics extrusion industry. Over the
years, Zenith has continually developed
and improved its pump designs to meet
the stringent demands made by new
polymers and new processes.
Zenith Pumps' line of PEP-II polymer
extrusion pumps has a unique positive
displacement design, which provides con-
sistent, accurate polymer delivery under
varying extruder output conditions of
pressure, temperature and viscosity.
These virtually pulseless gear pumps are
the ideal interface between the extruder
and the die of extrusion systems, and pro-
vide a homogeneous melt at increased
throughputs and tighter gauge tolerances.
For years, polymer processors have utilized
gear-pump-assisted extrusion to solve
critical issues in the diverse plastics
industry.
The Zenith gear pump optimizes the
extrusion process by allowing the screw
to melt and homogenize the polymer. As
the pump generates the needed pressure,
it relieves the extruder of work; therefore,
reducing heat from the shear, lowering the
torque required, and eliminating surging.
All this optimizes the performance of the
extruder and offers the following benefits:
•
Improved Dimensional Stability—
Effectively isolates the die from
upstream fluctuations.
•
Controlled Melt Quality—
Regulates
the extruder back pressure while it
reduces residence time, stabilizes the
plasticating action, and lowers melt
temperature.
•
Increased Production—
Provides very
high efficiency regardless of its pres-
sure building requirement.
•
Reduced Raw Material Usage—
Provides a narrower finished product
gauge variation.
•
Eliminates Surging and Screw Beat—
Effectively handles problems caused
by melt density or extruder parameters.
•
Increased Extruder Flexibility—
Allows varying process conditions
such as higher regrind levels, tempera-
tures, pressures, etc.
•
Crowned Root Gear Design—
Reduces shear internal to the pump,
lowering the temperature and increasing
the production rate per power required.
•
Streamlined Operation and Start-up—
Closed-loop controls provide easy
operator interface.
•
Extended Extruder Life—
Reduces
work required by the extruder such as
pressure and torque.
•
Lower Operational Costs—
Provides
a more efficient method of conveying,
eliminating material giveaway, and
increasing production per pound of
extrudate, etc.