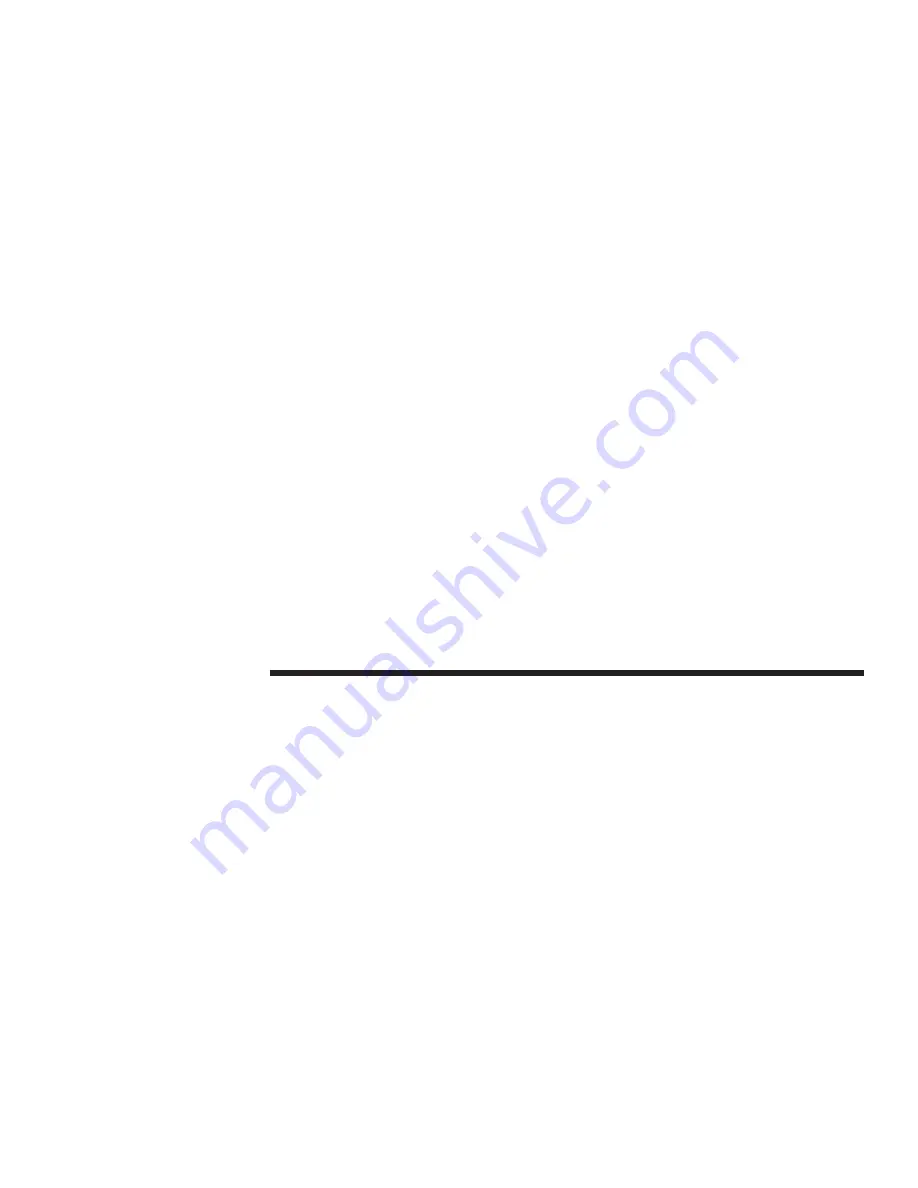
Cleaning,
Inspection,
Repair and
Service
7
Disassembly
After removal from the system, the assem-
bled pump can be cleaned by placing it
in a suitable furnace (i.e. vacuum oven,
fluidized bed, etc.) and slowly increasing
the temperature to 800-850° F in no less
than two hours. Special care should be
taken to avoid flashing of the polymer.
Control of temperature is essential as it is
possible to draw back the hardness of the
steel and affect dimensional stability if the
pump is overheated. The time to com-
pletely carbonize the polymer is three to
twelve hours, depending on the polymer,
temperature, pump size and furnace load.
The pump must be gradually cooled
to room temperature (no forced cooling
or quenching), then disassembled and
cleaned as instructed in the following
section. Close adherence to these instruc-
tions should be maintained for maximum
pump life and performance.
It is recommended that pump users
institute a program of dimensional inspec-
tion of critical parts in order to keep main-
tenance and operating costs at a minimum.
By noting the performance of a pump
immediately before removing it from service
and correlating the performance to meas-
ured component wear, the user can
establish the maximum wear limits for the
pump’s critical components. Further, he
can predict the service life of the pump,
and schedule his downtime accordingly.
After a pump has been disassembled,
all parts should be carefully inspected for
nicks, burrs, scoring or other signs of
wear. The side plates, D-bearings (and
sides of the gears on the 3.0 cc/rev and
smaller pumps) can be hand blocked on
600 grit paper, and any nick or burrs and
other sharp edges very lightly touched
with an Arkansas stone.
Note:
After cleaning, all seals, O-rings
and fasteners must be discarded.
CAUTION:
As the thickness relation-
ship between metering gears, center
plate and D-bearings is critical to metering
performance, care should be taken that
these parts are only polished and that
no metal is removed. Lapping of these
components should not be done under
any circumstances.
As with any other Zenith pumps, PEP-II
pumps may be returned to Zenith for
complete rehabilitation as necessary. This
procedure may be desirable if only a few
pumps are involved. If a large number of
pumps are to be maintained at the user’s
plant, it may be worthwhile to have key
maintenance personnel attend a mainte-
nance seminar at the Zenith factory to view
the manufacturing, gauging and assembly
techniques involved in producing the
PEP-II pump. In addition, Zenith also
offers a contract service program. Please
contact Zenith for further information on
these services.
These instructions should be thoroughly
read and understood before starting dis-
assembly.
General instructions that should be
observed to ensure correct disassembly
of the pump are as follows:
• If the pump is to be disassembled
on a regular basis, set up a room with a
separate clean area with all the tools
required for disassembly, reassembly and
storage.
• During disassembly, note the loca-
tion and orientation of all parts to ensure
proper reassembly.
• Use a soft-jawed vise to hold the
pump during disassembly.
When maintenance is required, refer
to the exploded view and disassemble the
pump as follows:
CAUTION:
Careful handling of the parts
is imperative. Do not drop or allow parts
to strike each other. The slightest nick or
burr can cause difficulty in reassembly and
may cause further damage to the pump.
1) Clearly mark which side of the
pump is the inlet port and drive input side.
2) Remove the screws securing the
Rheoseal seal plate cover to the seal
housing and remove the cover.
3) Remove the screws securing the
Rheoseal seal housing to the cover plate
and withdraw the housing from the cover
plate and shaft, taking care not to dam-
age the drive shaft. After removal of the
seal housing, disassemble and clean the
Rheoseal housings either mechanically or
chemically (always replace the O-rings).
4) Carefully pry out and discard the
lipseals at this time, taking care not to
damage the seal countersink in the hous-
ing, as damage here could cause polymer
leakage at start-up.
5) Loosen and remove the D-bearing
retainer screws (40 cc/rev and above
only).
6) Loosen all cover plate screws one
turn, then back them out and remove
them from the pump. Remove each cover