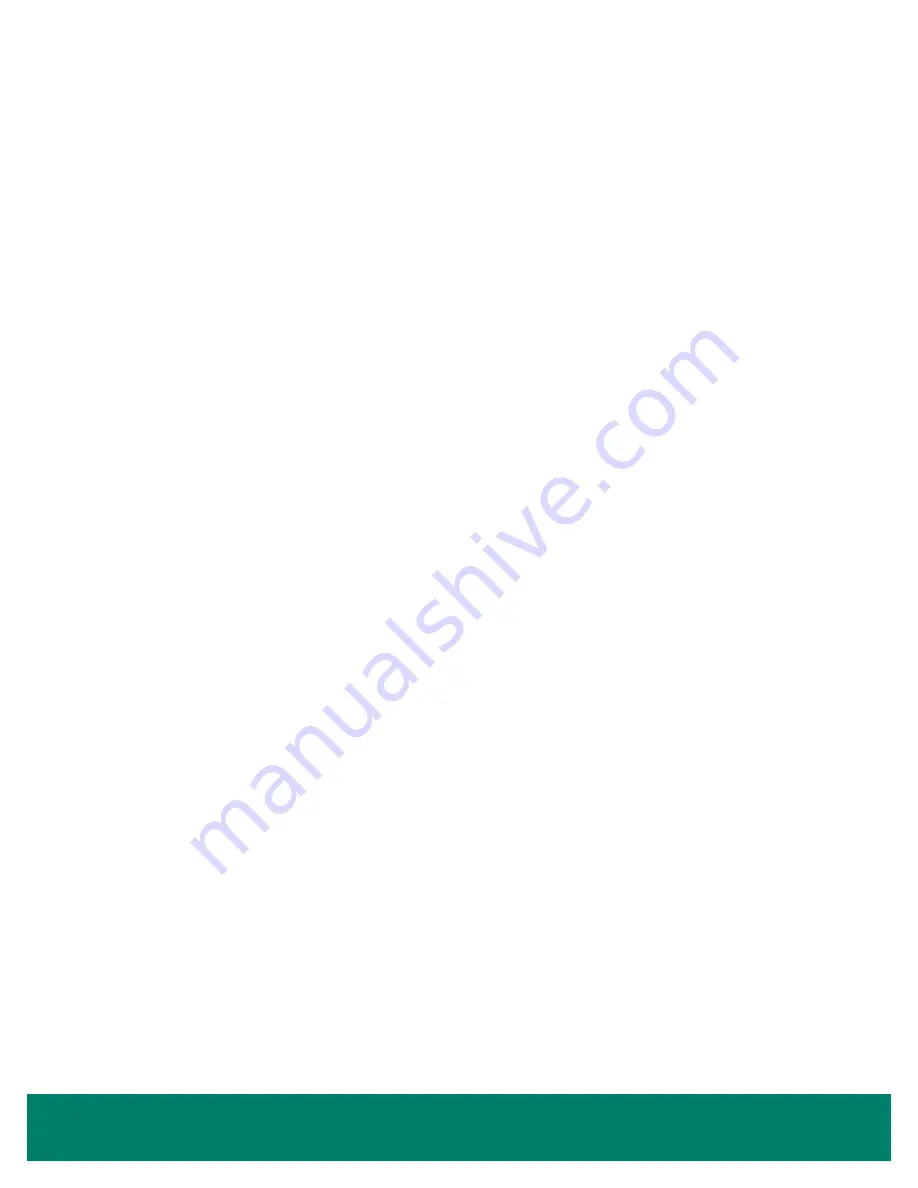
8 • Installation & Operation
INSTALLATION & OpERATION
1. Starting from the left end of the lineup, attach a Tinnerman clip to each bumper support bracket. Locate them over the hole for the bumper.
2. Attach the kickplate splice to the right side of the kickplate using the 3/4" screw in the lower hole.
3. Lean the kickplate against the bumper support bracket.
4. Hang the bumper on the case. The kickplate should be located behind the bumper assembly.
5. Install the black 1 1/2" screw through the bumper, kickplate, kickplate splice, and into the Tinnerman clip. A scratch-awl or similar tool can
be used to line up the holes.
6. Follow these steps to install the next bumper in the lineup. A bumper splice (provided) should be installed between the two cases. Center
the splice and adjust the height so the decorative tape (if applicable) lines up. Using self-tapping screws (provided), attach the upper
portion of the splice using the predrilled holes in the splice. Then with two more screws, attach the lower half.
UNDER CASE RETURN AIR FLOW ASSEMBLY INSTRUCTIONS
To assemble the bumper for under case return air flow (if requested), a spacer (provided) must be inserted between the bumper and kickplate.
. The spacer is held in place with the standard black assembly screw used to attach the bumper. One 3/8" spacer
is required at each screw location (2 spacers on a 2-door, 3 spacers on a 3-door, etc.).
1. To ease installation, hook the bumper to the case and position the kickplate. Then pull the bottom edge of the bumper forward, hold the
spacer in place, and then insert the assembly screw through the bumper, spacer, kickplate, bumper bracket, and into the Tinnerman clip.
2.
With the spacers in place, air will be allowed to flow between the bumper and kickplate and then underneath the case. The target airflow
rate under the case design is 50 cfm/door.
Note: An optional louvered kickplate is available. (Provides 150 cfm/door.)
Cleaning
The case and doors are cleaned prior to shipping. However, the case should be thoroughly cleaned before start-up and routinely thereafter to
maintain a clean appearance. Use mild detergent and warm water (never an abrasive cleaner) to wipe out the inside of the case. Wash down all
glass doors with glass cleaner. Do not wash down the fan motors. Do not use any products containing silicon on anti-fog glass coatings. Clean
interior glass reduces fogging and increases visibility. The case will remain bright and sparkling with just a few minutes of cleaning each week.
Internal components can be cleaned after removal of access panels. The case drain should be regularly cleared of debris and price tags.
Coils may be cleaned with a garden hose or pails of water. Cases that use pump, drain pans and condensate evaporators should be cleaned
with a minimum amount of water. The drain should be blocked and the water removed with a shop vacuum.
Do not use high-pressure water or steam to clean the interior.
UNDER CASE FLOOR CLEANING (NSF)
The floor underneath your Zero Zone display case can be cleaned by following a few simple steps:
1. Remove the fasteners that hold the bottom kick plate to the display case. The fasteners are accessed from the front of the unit.
2.
With the kick plates removed, remove paper and other debris (typically price tags or receipts) from the floor.
3. Vacuum under the case to remove any dust build-up that may be present.
4. Using an approved cleaner and warm water, mop underneath the unit.
5.
When finished mopping, squeegee any remaining water underneath the unit to the floor drains to speed the drying process. Replace the
kick plates when the floor has dried.