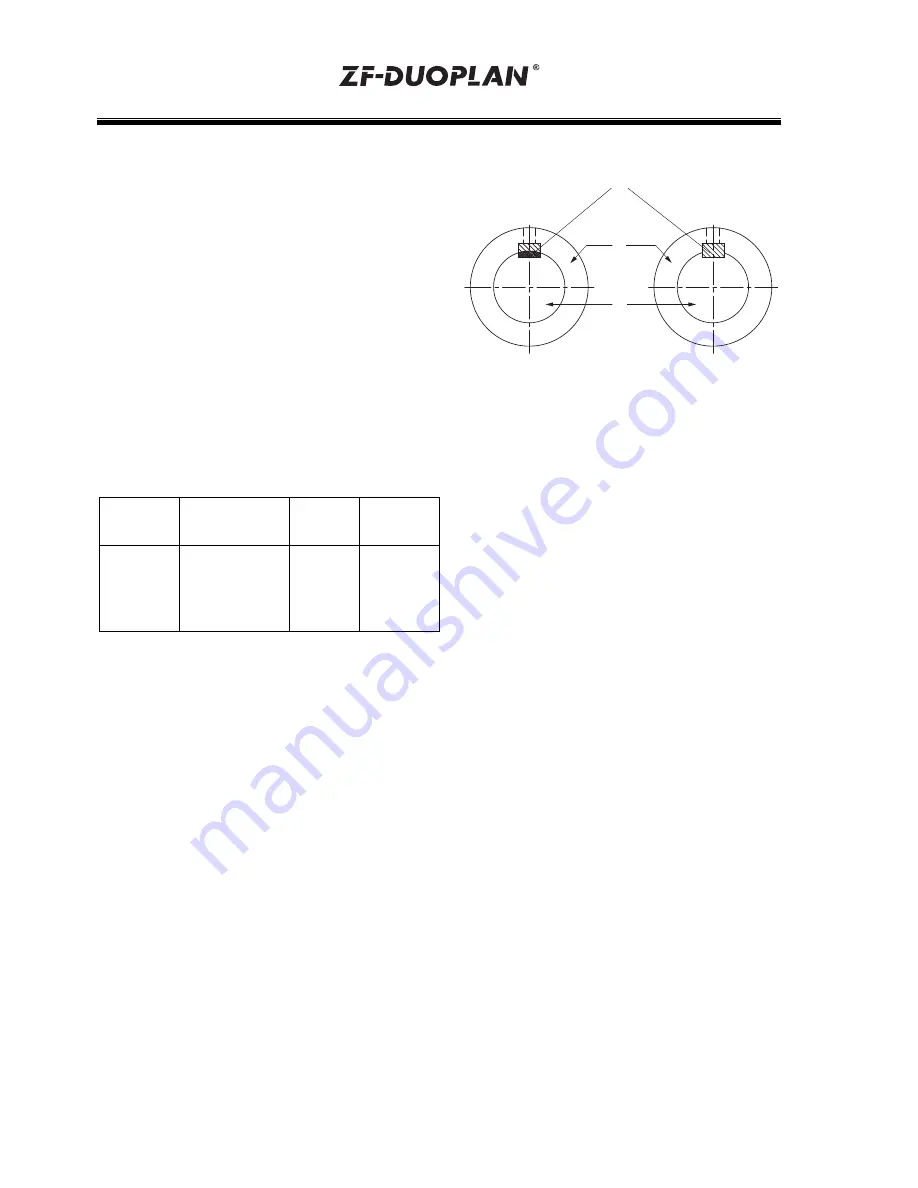
Operating
Instructions
Initial Installation
2K800/2K801/2K802
12
EN 4161.758.103m – 2015-10
Semi-key balancing
Full-key balancing
3.2
Balancing
The hubs (2) come with a keyway (1) for
transmitting power from the motor shaft (3) as
standard.
There are two balancing types for the motor
and gearbox: Semi-key and full-key, which are
described in more detail in DIN ISO 8821.
It must be ensured that the hub is balanced in the
same way as the motor.
This is why it is very important to indicate the
motor data, dimensions and balancing type when
ordering.
Motor output shafts with standard fitted key
in accordance with EN 50347: 2001
Gearbox
type
Shaft diameter
Fitted
key
Fitted key
length
2K800
2K801
2K802
60 mm
65 mm
75 mm
80 mm
A18x11
A18x11
A20x12
A22x14
125 mm
125 mm
125 mm
140 mm
NOTE
In the case of motor shafts with open ends of the
keyway, the parallel key is to be glued into the
groove in order to avoid axial migration of the
parallel key and/or the hub.
3.2.1
Semi-key balancing
In semi-key balancing, the keyway is filled with
a balance compensation corresponding to
approximately half a key, shape B by default. This
is based on the original key, shape, length and
position used by the motor manufacturer and is
defined as a counterweight. In semi-key balancing
– in contrast to full-key balancing – the joint
passes through a shared component. This means
imbalance can arise after assembly due to
tolerance factors.
As a result, it is recommended that rebalancing
should be performed after the joined parts have
been assembled.
3.2.2
Full-key balancing
In full-key balancing, the motor shaft is balanced
with a full key whereas the hub is not. The key,
shape, length and position are not important in
this case.
1
2
3