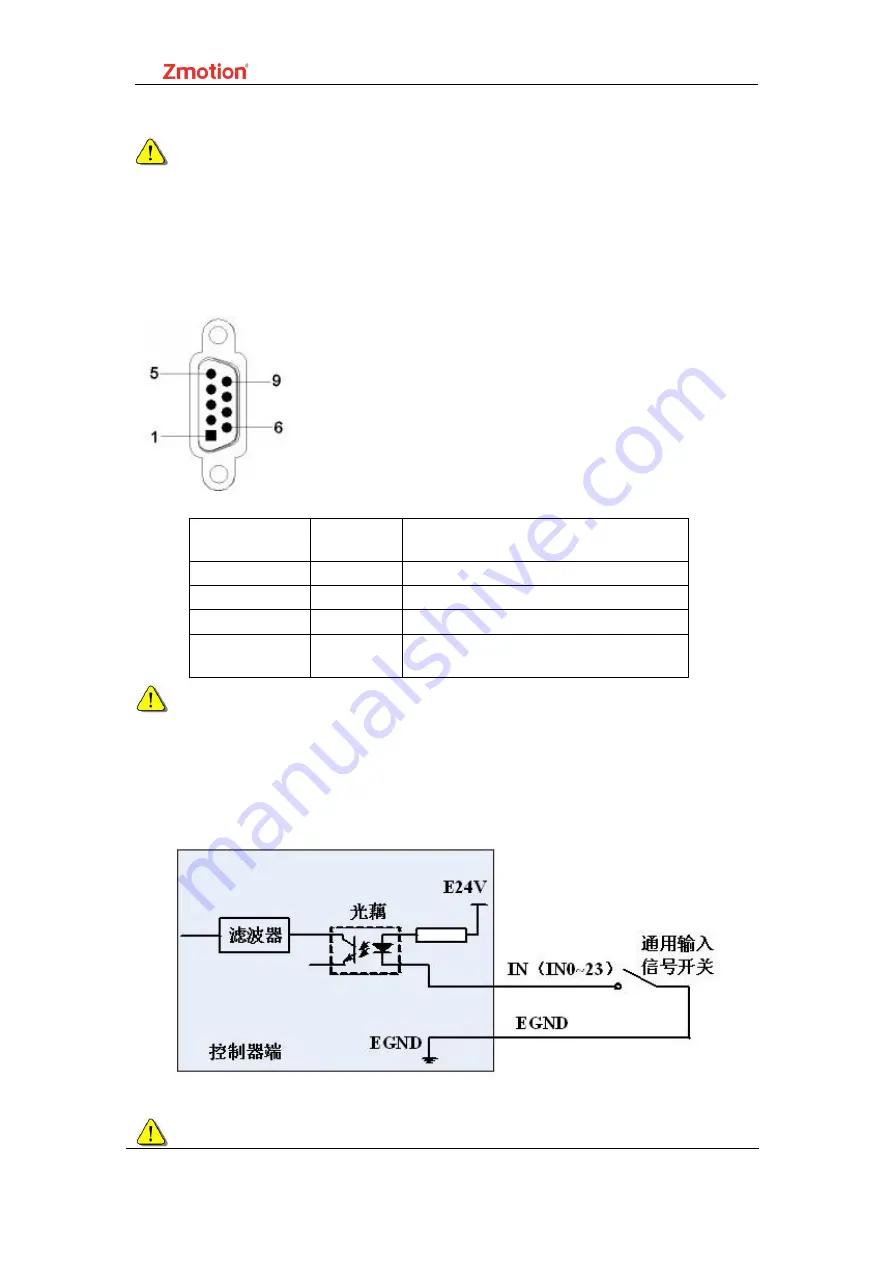
ZMC420SCAN Motion Controller
14
resistance.
The communication interface of ZMC4 series adopts external 24V power supply, please
pay attention when connecting with other controllers or touch screens.
2.2.3
RS232 interface:
RS232 interface. Its 9pin pin is defined as follows:
Pin
number
name
Explanation
2
RXD
Receive data pin
3
TXD
Send data pin
5
EGND
External power ground
9
E5V
External power supply 5V output, can
be used to power the text screen
To connect with the computer, you need to use a 2.3-crossover cable with double
female connectors.
2.2.4
General input signal:
There is another universal input port in each axis signal, see axis interface