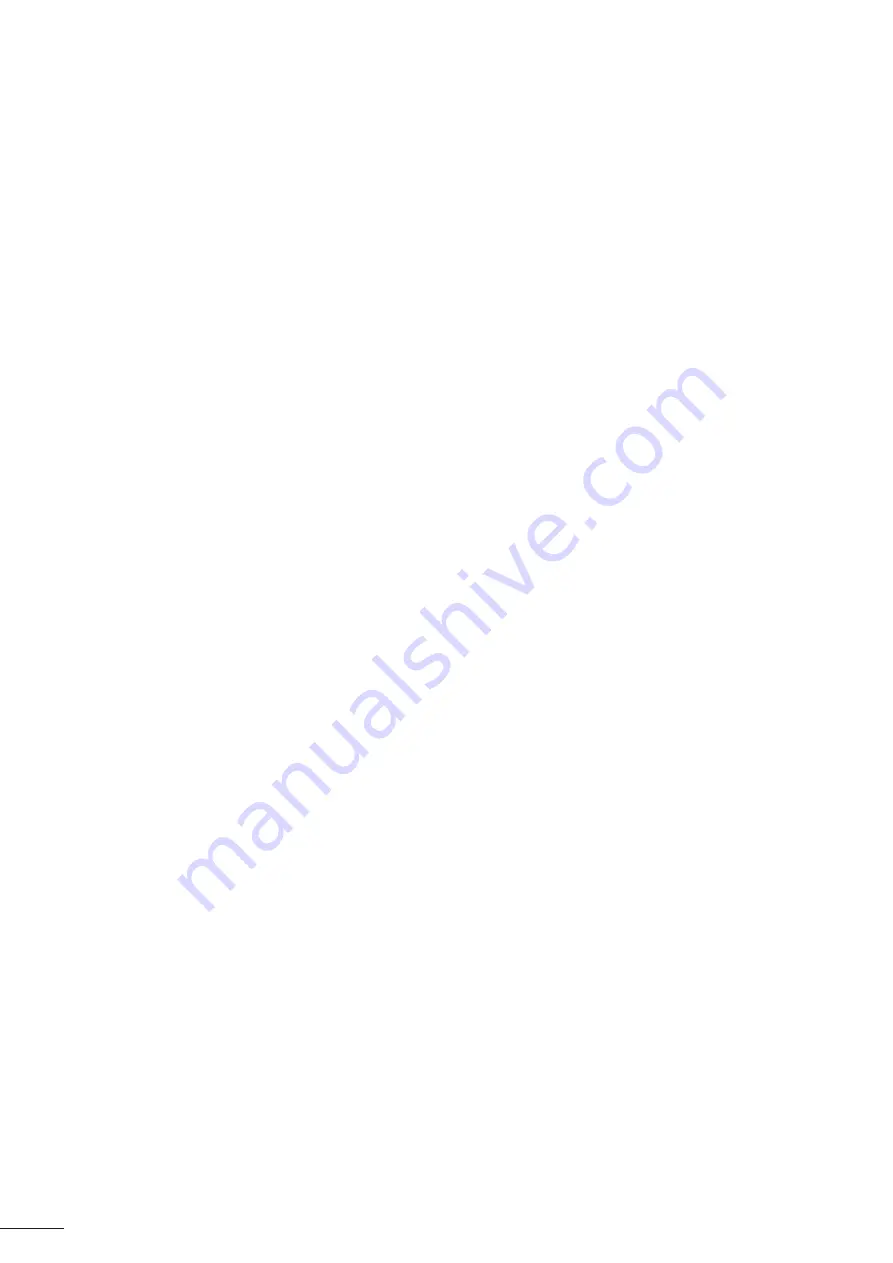
16
approved by the manufacturer. When in doubt, contact the manufacturer’s technical department for assistance.
•
The following checks must be applied to installations using flammable refrigerants:
- if an indirect cooling circuit is used, the presence of refrigerant in the secondary circuit must be analysed;
- the markings on the equipment must remain visible and legible; any illegible markings or signs must be rectified;
- the hoses or components of the cooling circuit are installed in a position where they are unlikely to be exposed to
any substance capable of corroding the components containing refrigerant, unless the components are made from
materials that are typically corrosion-proof or correctly protected from such corrosion.
Electric component check
•
The repair and maintenance of electric components must include initial safety checks and component inspection
procedures. If a defect capable of jeopardising safety arises, no power supply must be connected to the circuit until
the problem has been completely resolved. If the defect cannot be rectified immediately and if maintenance work
must continue, an appropriate temporary solution must be found. This must be reported to the equipment’s owner
so that all persons concerned are made aware.
•
The repair and maintenance of electric components must include the following initial safety checks:
- the capacitors are discharged: this must be carried out safely to prevent all risks of ignition;
- no electric component or live wiring is exposed while charging, overhauling or draining the system;
- the system must be grounded at all times.
Repair of insulated components
•
When repairing insulated components, all power sources must be disconnected from the equipment on which
the work is being carried out before removing the insulating cover, etc. If the equipment must be powered during
maintenance work, a leak detector must continuously monitor for leaks at the most critical point in order to report
any potentially hazardous situation.
•
Particular attention must be paid to the following points to ensure that, when performing work on the electric
components, the housing is not altered to the point of affecting the protection rating. This includes damaged wires,
an excessive number of connections, terminals that do not comply with the original specifications, damaged seals,
incorrect installation of the cable glands, etc.
•
Make sure that the appliance is properly fixed.
•
Make sure that the seals or insulating materials are not deteriorated to the point that they no longer prevent a
flammable atmosphere from penetrating the circuit. Spare parts must be compliant with the manufacturer’s
specifications.
Repair of intrinsically safe components
•
Do not apply any permanent electric capacitance or induction charge to the circuit without checking that it does not
exceed the allowed voltage and intensity for the equipment being used.
•
Typically safe components are the only types on which work can be carried out in the presence of a flammable
atmosphere when live. The test appliance must fall under a suitable classification.
•
Only replace components with parts specified by the manufacturer. Other parts could cause the refrigerant to leak
and ignite in the atmosphere.
Wiring
•
Check that the wiring shows no signs of wear, corrosion, excessive pressure, vibration, cutting edges or any other
detrimental environmental effect. The check must also take into account the effects of ageing or continuous vibrations
caused by sources such as compressors or fans.
Detection of flammable refrigerant
•
Under no circumstances must potential ignition sources be used to search for or detect refrigerant leaks. A halide
torch (or any other detector using a naked flame) must not be used.
•
The following leak detection methods are considered to be acceptable for all cooling systems.
•
Electronic leak detectors can be used to detect refrigerant leaks; however, in the case of flammable refrigerants, the
sensitivity level may not be suitable or recalibration may be necessary. (The detection equipment must be calibrated
in an area devoid of refrigerant). Check that the detector is not a potential ignition source and is appropriate for the
refrigerant used. The leak detection equipment must be adjusted to a percentage of the refrigerant’s LFL and must
be calibrated according to the refrigerant used. The appropriate gas percentage (25% at most) must be confirmed.
•
Leak detection fluids are also suited for use with most refrigerants, however the use of detergents containing chlorine
must be avoided since it could react with the refrigerant and cause corrosion to the copper piping.
•
If a leak is suspected, all naked flames must be removed/extinguished.
•
If a refrigerant leak is detected and requires soldering, the entire quantity of refrigerant must be removed from the
system or isolated (by way of shut-off valves) in part of the system located away from the leak.
Removal and discharge
•
When accessing the cooling circuit to carry out repairs, or for any other reason, conventional procedures must be
employed. However, for flammable refrigerants, the recommendations must be complied with in order to take
account of the product’s flammability. The following procedure must be followed:
- remove the refrigerant;
- purge the circuit with an inert gas;
- drain;
- purge with an inert gas;
- open the circuit by cutting or soldering.
•
The refrigerant charge must be recovered in suitable recovery cylinders. For appliances containing flammable
refrigerants other than A2L refrigerants, the system must be bled with nitrogen devoid of oxygen to make the appliance
suitable for receiving flammable refrigerants. You may need to repeat this process several times. Compressed air or
oxygen must not be used to purge cooling systems.
Loading procedures
•
Check that the vacuum pump outlet is not located in the vicinity of any potential ignition source and that ventilation
is provided.