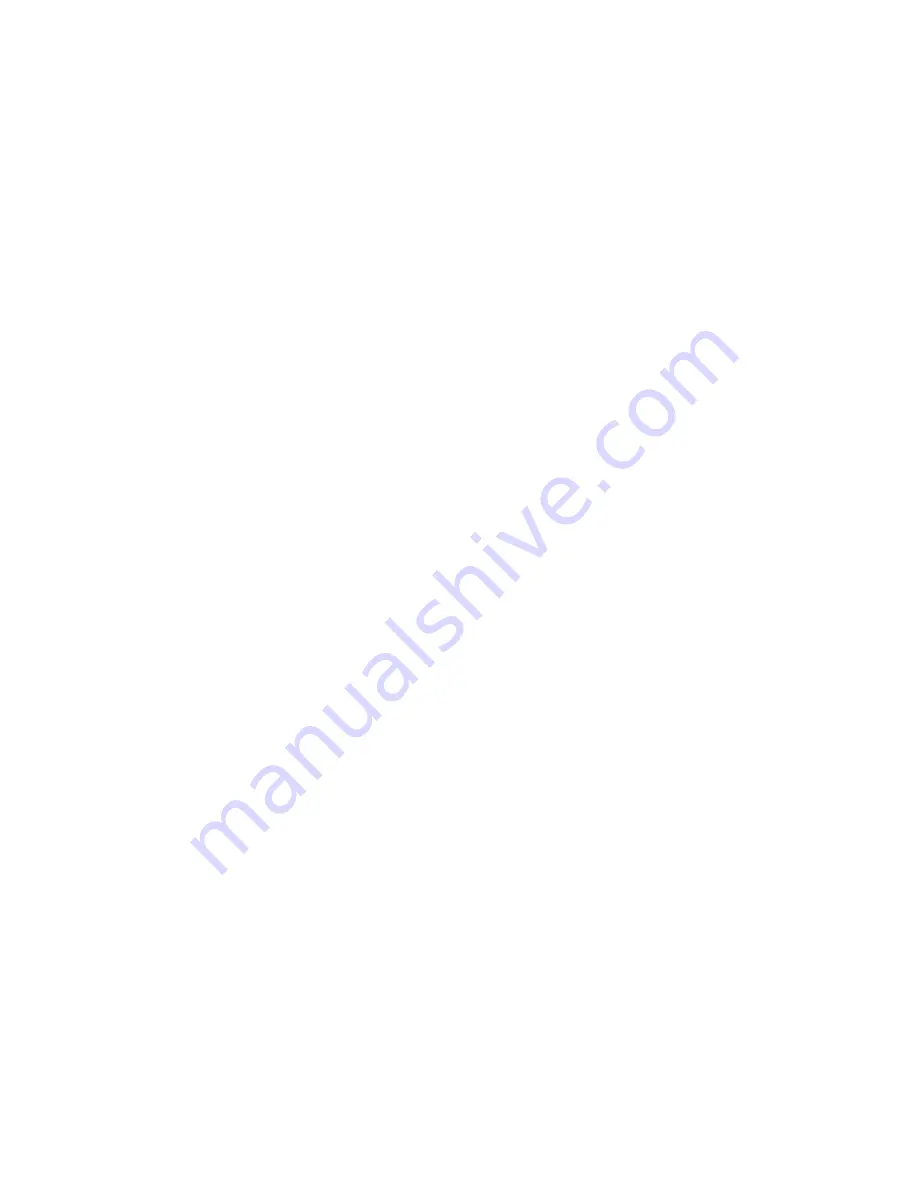
ACCU TURN
MULTI-SPEED BRAKE LATHE SYSTEM
MODEL 8944
OPERATIONS AND MAINTENANCE MANUAL
PAGE
2 List of Standard Equipment
2 Brake Lathe Specifications
3 Acceptance from Carrier
3 - 7 Safety Information
8 Assembly of Lathe
9 - 14 Operation Procedures
Multi-Speed Settings
Inspection
Drums or Rotors
Flywheels
15 - 18 Diagrams
19 - 24 Parts List
25 - 30 Additional Diagrams
31 Warranty
When ordering parts contact your local For Records and Information:
Distributor, give Serial # of your machine Date Recv __________
and the date purchased; this will help in Serial # ____________
expediting your order. Rep Name__________
04\97 500
#436311
Summary of Contents for 8944
Page 18: ...15 PROPER MOUNTING OF HUBLESS ROTOR OR DRUM ...
Page 19: ...16 PROPER MOUNTING OF HUBBED ROTOR OR DRUM ...
Page 20: ...17 PROPER MOUNTING OF FLYWHEEL ...
Page 28: ......
Page 29: ...26 ...
Page 30: ...27 ...
Page 31: ...28 ...
Page 32: ...29 ...
Page 33: ...30 ...
Page 34: ...31 ...
Page 35: ...32 ...
Page 36: ......
Page 37: ...33 ...