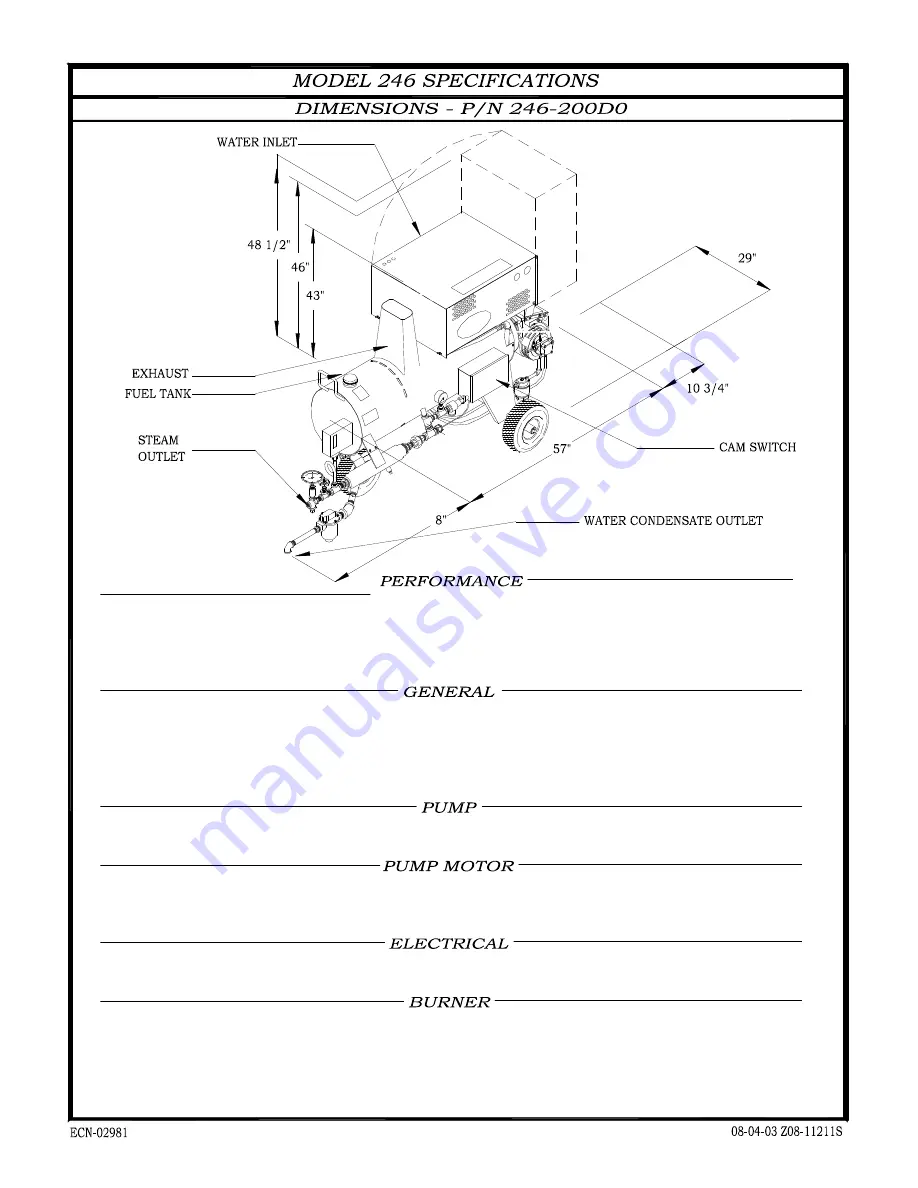
FUEL NOZZLE..................(4.50 90 DEGREE B) P/N V4.50 90DB
TYPE.........................................................PRESSURE ATOMIZING
FUEL TYPE......................................KEROSENE, #1 OR #2 DIESEL
FUEL CONSUMPTION...............................4.92 GPH / 18.6 LPHR
FUEL PRESSURE ..............................................120 PSI / 8 BAR
FUEL PUMP ..........................................(DANFOSS) V-100714-001
MOTOR - 1/4HP.....................................................P/N V00-20383
VOLTAGE..............................................................115V 1PH 60HZ
SPEED........................................................................3450 RPM
BURNER....................................................................V00-17345
VOLTAGE............................................... 115 VAC, 60 HZ, 1 PH
TEMPERATURE CONTROL - HIGH LIMIT.....P/N F04-00817-C1
CAM SWITCH...............................................................F04-00741A
CURRENT...........................................................................15 AMP
PULLEY.......................................(AK32 X 5/8) P/N R03-00132
PART NUMBER..............................................................F02-00042
SPEED.......................................................................1725 RPM
VOLTAGE ..............................................................115V 60HZ 1PH
HORSEPOWER............................................. 3/4 HP / 0.56 KW
PUMP ...................................................(TT941) P/N N07-00026
PULLEY................................................(AK69H) P/N R03-00669
COIL BACK PRESSURE REQUIRING DESCALING...................................................................50 PSI @ 2.0 GPM / 3.40 BAR @ 7.5 LPM
COIL SIZE................1/2"ID X 126' SCHEDULE 40 - P/N 53-200
COIL BACK PRESSURE (NEW)..................................................................................................5 PSI @ 2.0 GPM / 0.34 BAR @ 7.5 LPM
WEIGHT (DRY)....................................................650 LBS / 283 KG
MINIMUM WATER INLET PRESSURE..............40 PSI / 0.68 BAR
HOSE, HIGH PRESSURE.............3/8" X 16 1/2' P/N Y01-00016
FUEL TANK CAPACITY...............................................10 GAL / 38 L
BELT............................................(A30 SUPER II) P/N R02-00430-II
ALL DIMENSIONS ARE IN
IN INCHES UNLESS OTHERWISE
NOTED. 1 INCH = 25.4 MM
PUMP HEAD PRESSURE.....................................80 PSI / 6 BAR
TEMPERATURE LIMIT...............................UP TO 425 DEGREES
TEMPERATURE RISE...375°F @ 132 GPHR / 191°C @ 500 LPHR
DRAFT/STACK INSTALLATION................0.2" - 0.04" WC READING
COMBUSTION SMOKE/BACHARACH SCALE......#1 OR #2 SMOKE
CARBON MONOXIDE ALLOWED...........................................0.01%
HEAT INPUT....................630,000 BTU/HR / 158,760 KCAL/HR
PULLEY BUSHING...............................(H X 24MM) P/N R04-00001
1
Summary of Contents for 246-200D0
Page 23: ...2 2 ...
Page 24: ...3 ...
Page 25: ...12 05 03 Z08 11218 ECN 02981 Supersedes 07 31 03 Z08 11218 4 ...
Page 26: ...5 12 05 31 Z08 11218 ECN 02810 Supersedes 07 31 03 ...
Page 27: ...6 ...
Page 28: ...7 ...
Page 29: ...8 ...
Page 33: ...WIRE COLOR CODE 12 ...
Page 34: ...13 ...
Page 35: ...14 ...
Page 36: ...15 ...
Page 37: ...16 ...
Page 38: ...17 ...
Page 40: ...19 ...
Page 44: ...23 ...