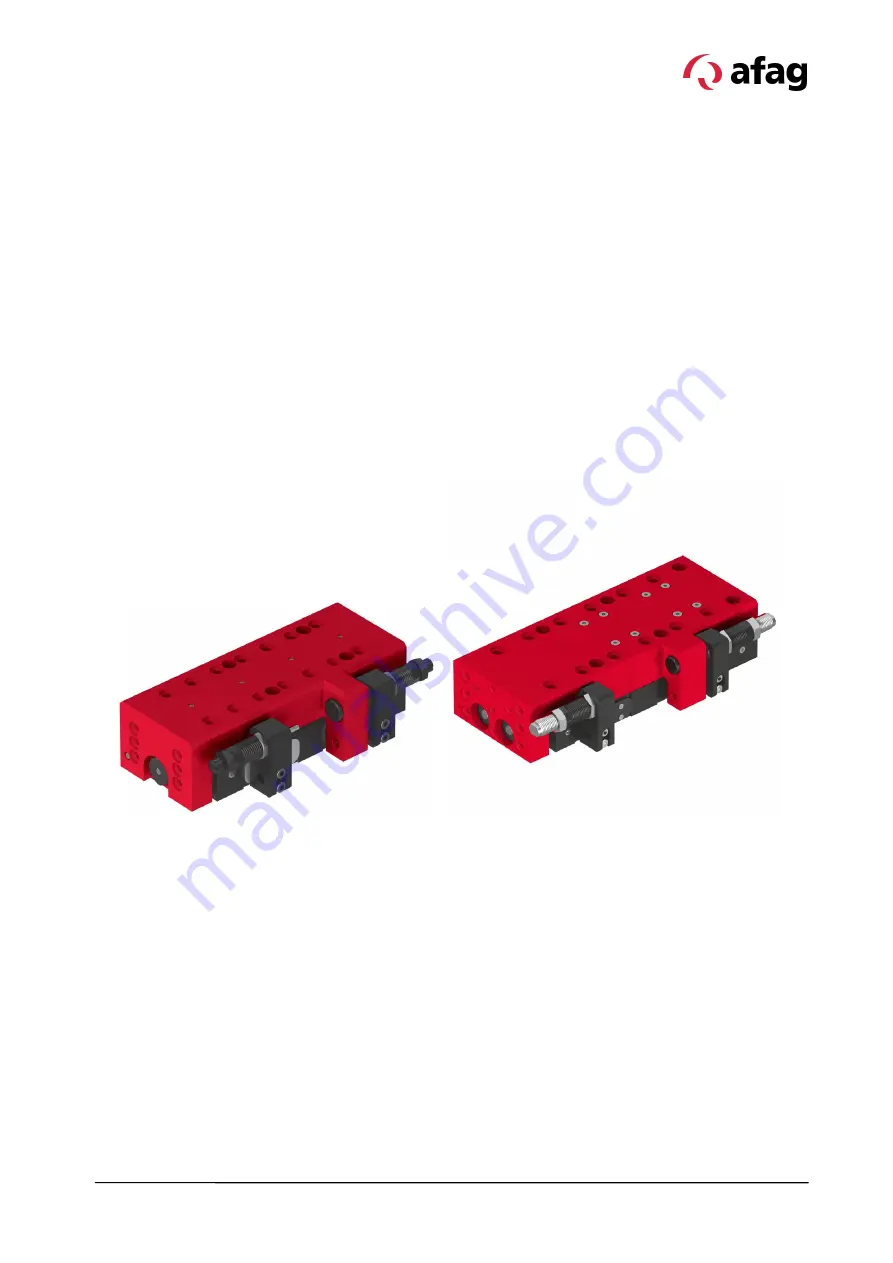
Assembly instructions
EN
CS 16 - CS 20
Date 01.06.2021
Version 6.0
1–64
Assembly and operating instructions
C
ompact
S
lide
CS 16 – CS 20
Translation of the Original Assembly Instructions EN
CS 16/30
Order no.: 50167742
CS 16/60
Order no.: 50154069
CS 16/90
Order no.: 50154070
CS 16/120
Order no.: 50154071
CS 20/50
Order no.: 50100711
CS 20/100
Order no.: 50100712
CS 20/150
Order no.: 50100713