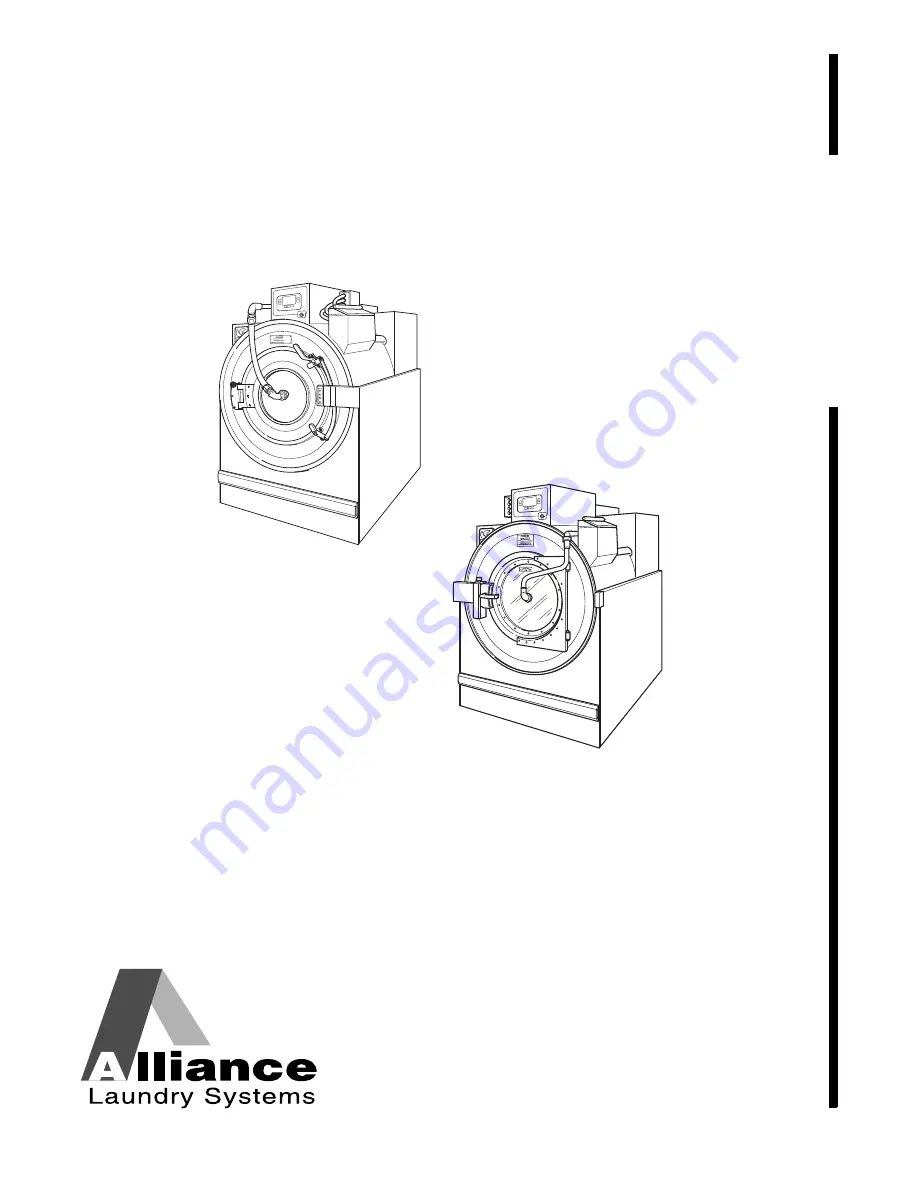
Installation
www.alliancelaundry.com
Washer-Extractors
Pocket Hardmount
UniLinc
Refer to Page 5 for Model Numbers
PHM1400C
PHM1400C
PHM1402C
PHM1402C
150 Model
35 – 125 Models
Part No. F8138601R12
October 2012
Keep These Instructions for Future Reference.
(If this machine changes ownership, this manual must accompany machine.)