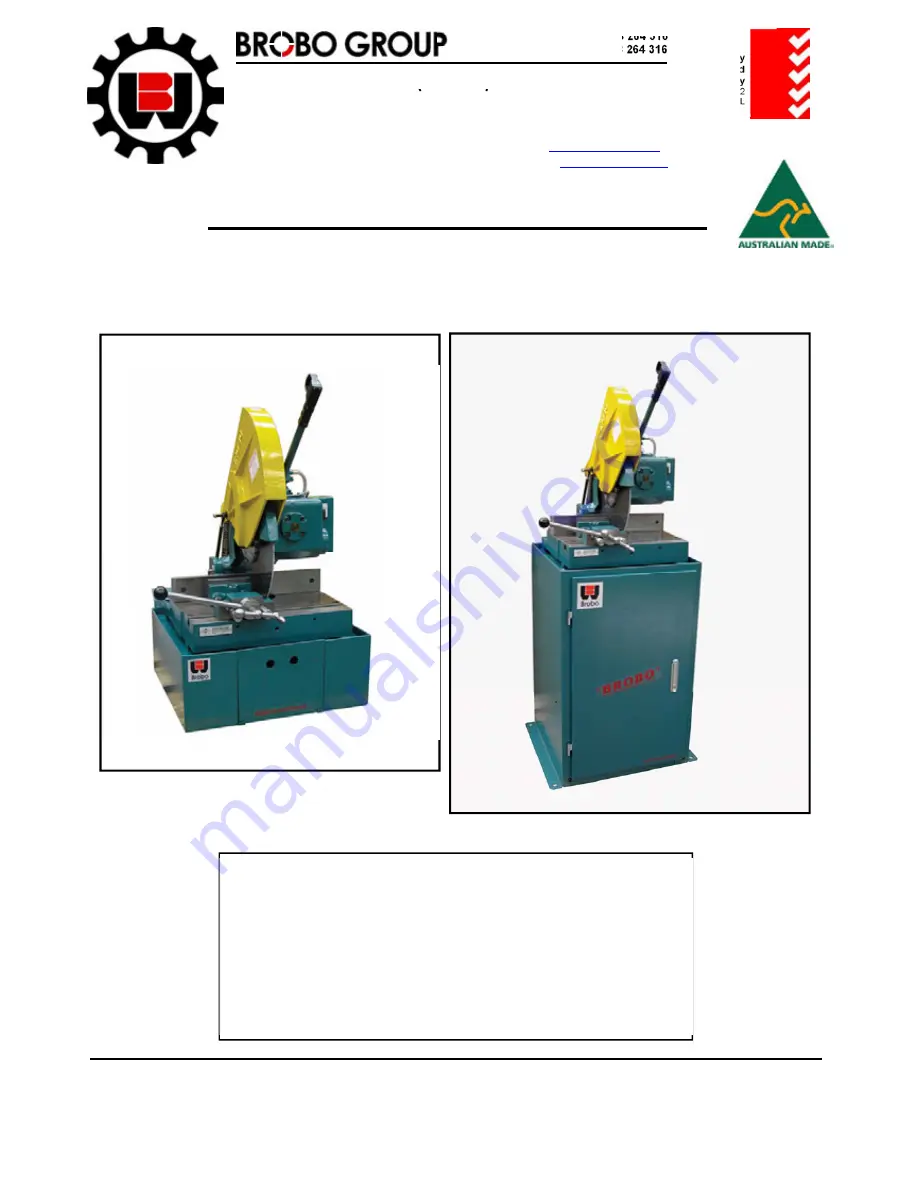
Precision Drilling Machines
Tapping Machines
Multi Head Drills
Tool Grinders
Tool Post Grinders
Machine Vices
Special Production Equipment
Accessories
Riveting Machines
Pedestal Grinders
Metal Cutting Saws
Linishers
PRODUCT AND MAINTENANCE MANUAL
OHS SERIES METAL SAWS
MODEL No. S315D, S350D, S400B / Serial No’s. C 29680~
BROBO GROUP (AUST) PTY. LTD.
A.C.N.
098 264 316
A.B.N.
42 098 264 316
8 Fowler Rd, Dandenong, 3175
PO BOX 4274 Dandenong Sth, 3164
Victoria, AUSTRALIA.
Tel:
61 3 9794 8751
Email:
info@brobo.com.au
Fax:
61 3 9794 8792
Website:
www.brobo.com.au
Quality
Endorsed
Company
ISO 9001 Lic. 10292
SAI GLOBAL
Quality System
YOUR BROBO DISTRIBUTOR IS:
Bench Mount Unit
Floor Mount Unit