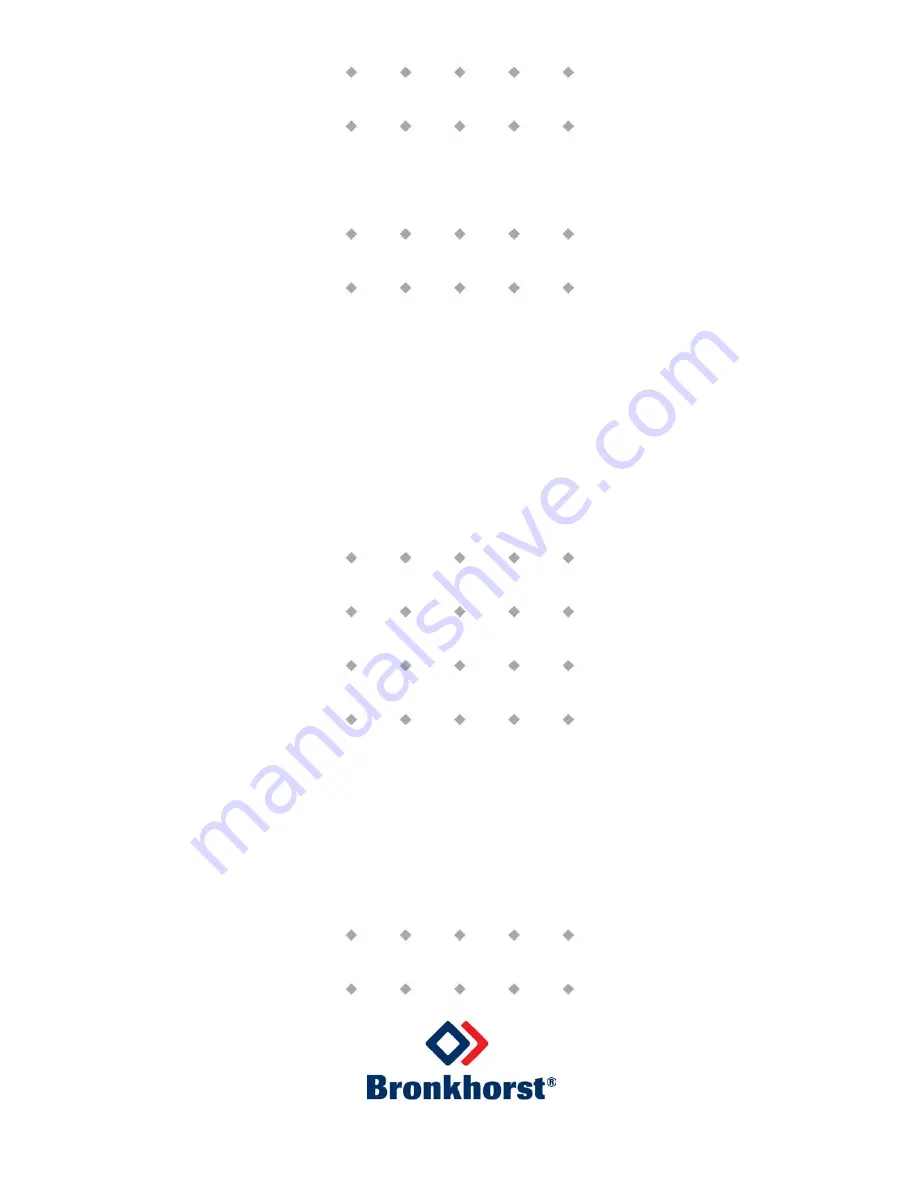
Doc. no.: 9.17.045V Date: 26-11-2018
ATTENTION
Please read this Instruction Manual carefully before installing and operating the instrument.
Not following the guidelines could result in personal injury and/or damage to the equipment.
IQ
+
FLOW
®
series
Digital Mass Flow / Pressure Controllers
for gases
Instruction Manual