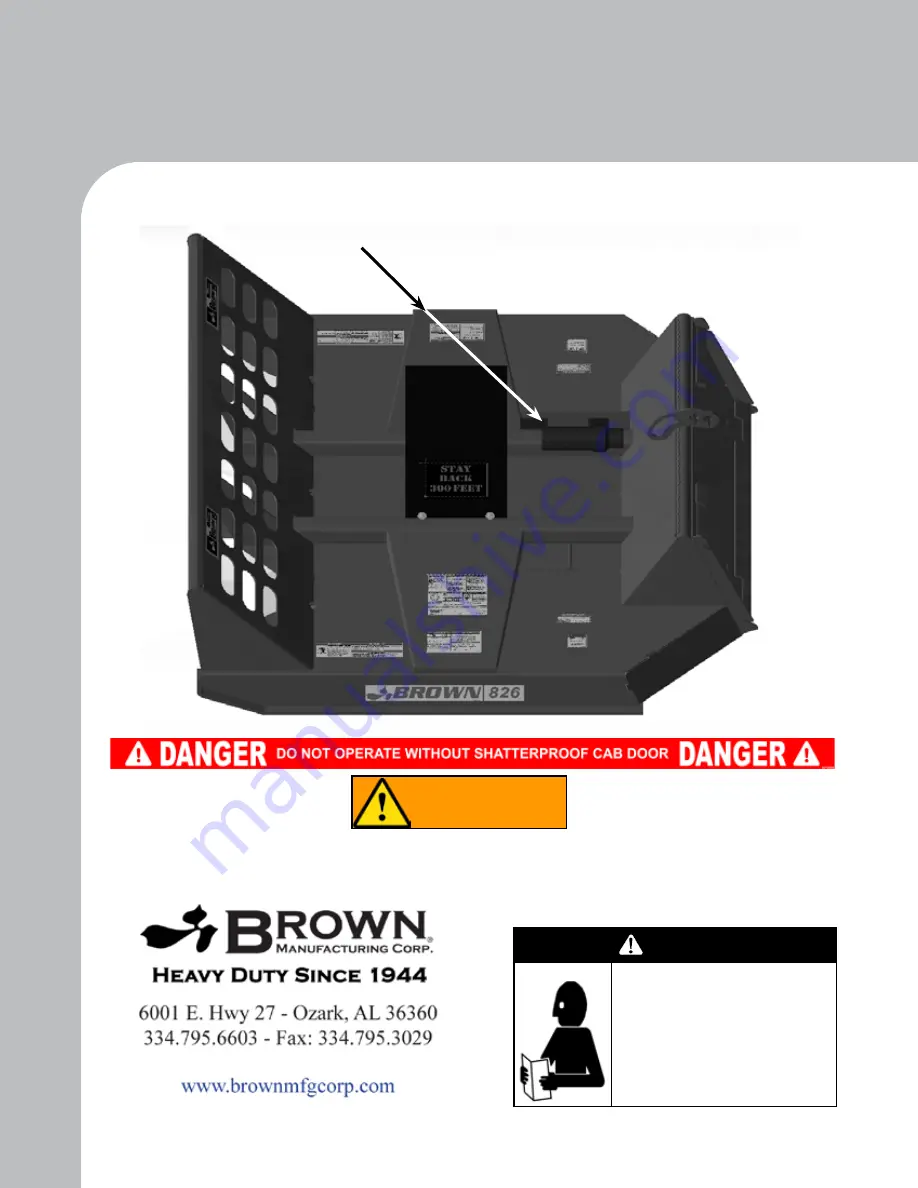
Owner / Operator Manual
Brown 815
Brush Cutter
Before operating your machine,
stop and read this owners manual.
Do not attempt to operate the unit
until you fully understand the
material covered in this manual.
Without the knowledge contained
in this manual, injury or death can
result.
WARNING
For use with models having serial numbers with “
A
” as
the
FOURTH
digit:
Example: 815A0001
Lift Restriction Chains
must be attached from the skid loader to the brush cutter to keep the
cutter below the level of the operator BEFORE operating this machine. See
Page 17
for further
information.
ATTENTION:
ALL WARRANTY WORK
MUST
BE APPROVED
BY BROWN MFG. CORP.
BEFORE
WORK BEGINS
Serial Plate Location
WARNING