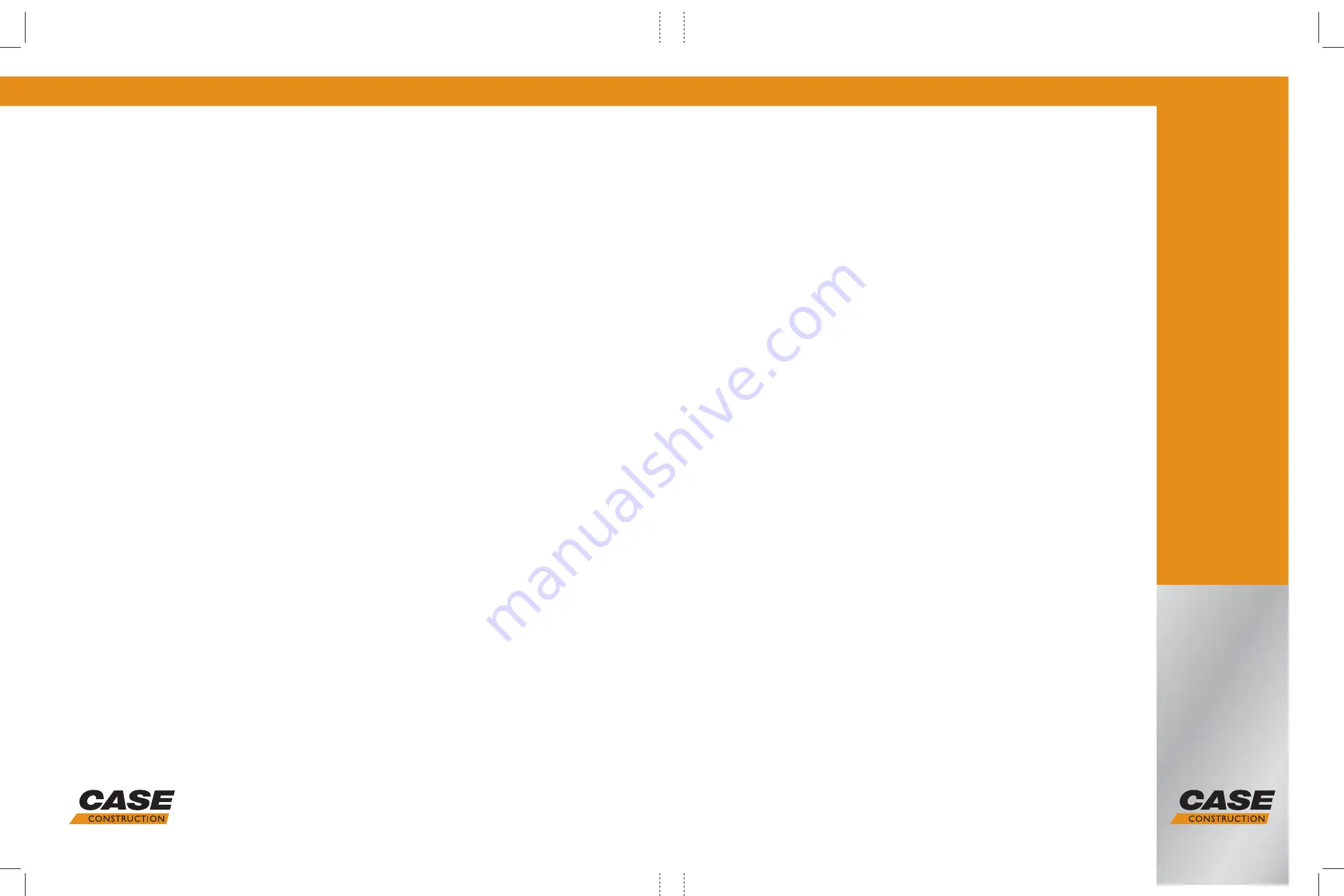
Part number 47685161
1
st
edition English
June 2015
SERVICE MANUAL
SR270 / SV300
Tier 4B (final)
Alpha Series Skid Steer Loader
SR270 PIN NFM481941 and above; SV300 PIN NFM470295 and above
TR340 / TV380
Tier 4B (final)
Alpha Series Compact Track Loader
TR340 PIN NFM482972 and above; TV380 PIN NFM483044 and above
Printed
in U.S.A.
© 2015 CNH Industrial America LLC. All Rights Reserved.
Case is a trademark registered in the United States and many
other countries, owned by or licensed to CNH Industrial N.V.,
its subsidiaries or affiliates.