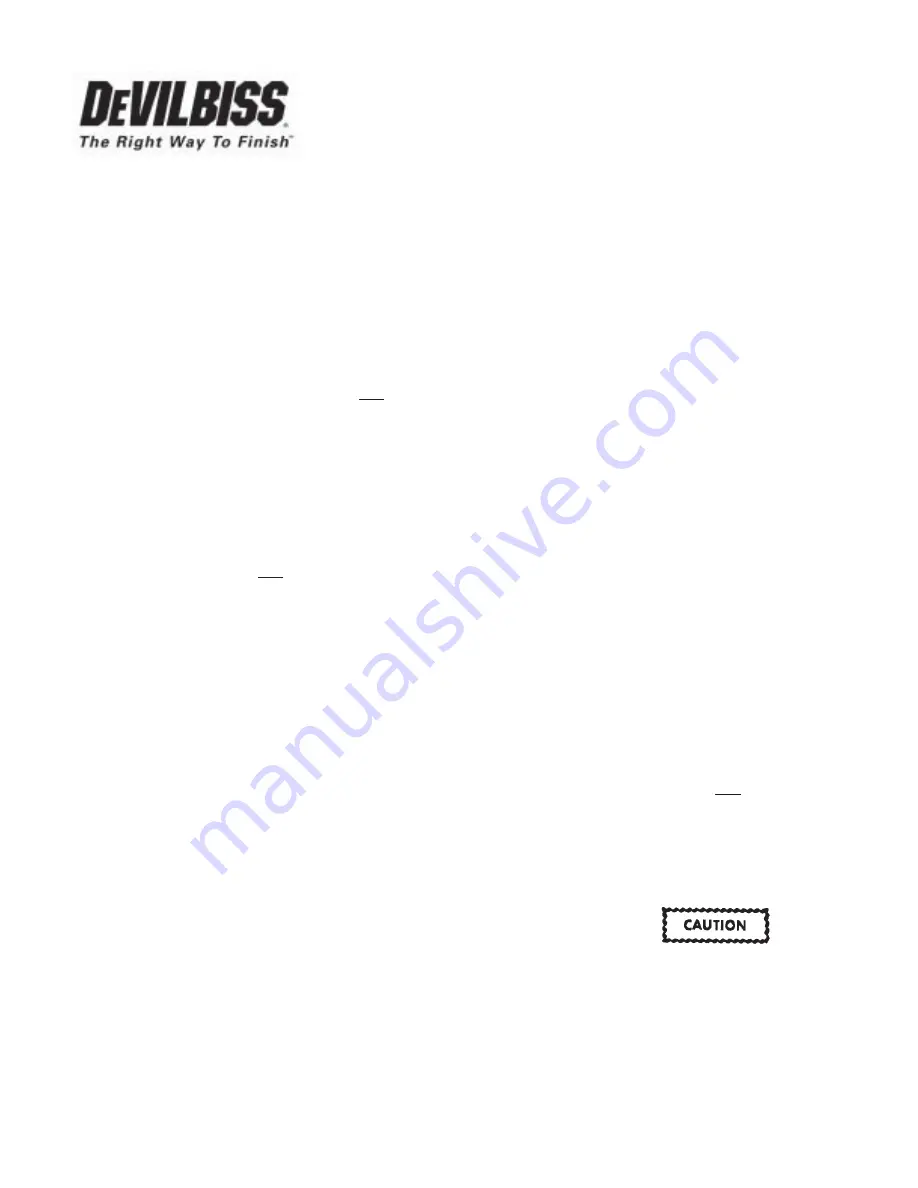
IMPORTANT: Before using this equipment,
read all safety precautions and instructions.
Keep for future use.
DESCRIPTION
The gravity feed high volume low pressure
GFG gun is designed to apply a wide variety
of finishing materials. This gun was manu-
factured to provide maximum transfer effi-
ciency by
limiting air cap pressure to 10 psi
(complies with rules issued by SCAQMD
and other air quality authorities).
This gun will produce approximately 10 psi
cap pressure at 80 psi gun inlet pressure, as
measured at the gun inlet. An air cap test kit
(see
Accessories) should be used to insure
10 psi air cap pressure is not exceeded.
Note
This gun includes stainless steel
fluid passages, 300 series SS
needle and and 400 series SS fluid
tip. Guns may be used with chlo-
rinated solvent materials only if
the attached gravity cup is Acetal.
Do not use aluminum cups with
chlorinated solvent materials.
Note
The GFC gravity feed cups are only
included with the gun as part of
the gun-cup assembly. See
Accessories on page 6 for
more information.
Important:
This gun may be used with most
common coating and finishing materials. It
is designed for use with mildly corrosive
and non-abrasive materials. If used with
other high corrosive or abrasive materials,
it must be expected that frequent and thor-
ough cleaning will be required and the ne-
cessity for replacement of parts will be
increased.
INSTALLATION
For maximum transfer efficiency,
do not
use more pressure than is necessary to
atomize the material being applied.
1 .
Connect the gun to a clean, moisture
and oil free air supply using a hose size
of at least
5/16" I.D.
hose. Do not use
1/4" I.D. hose (25' x 1/4" hose at 18 CFM
has a pressure loss of 25 psi. 25' x 5/16"
hose at 18 CFM has a pressure loss of
8 psi).
Note
Depending on hose length, larger
I.D. hose may be required. Install an
HAV-501 air gauge at the gun handle
and air cap test kit over tip. When
SERVICE BULLETIN
SB-2-169-D
Replaces SB-2-169-C
Repair Kit KK-5025
GFG-517 GRAVITY FEED HIGH VOLUME LOW PRESSURE SPRAY GUN
gun is triggered on, adjust regulated
pressure to desired setting to pro-
vide a maximum of 10 psi at the air
cap.
Do not use more pressure than
is necessary to atomize the material
being applied.
Excess pressure will
create additional overspray and re-
duce transfer efficiency.
Note
If quick connects are required, use
only high flow quick connects (see
Accessories, page 6). Other types
will not flow enough air for proper
gun operation.
Note
If an air adjusting valve is used at the
gun inlet, use DeVilbiss Model HAV-
500 or HAV-501. Some competitive
adjusting valves have significant
pressure drop that can adversely
affect spray performance. Models
HAV-500 and HAV-501 have minimal
pressure drop, which is important for
HVLP spraying.
2 .
Attach the gravity feed cup to the
material inlet.
Note
Protective coating and rust inhibi-
tors have been used to keep the
gun in good condition prior to ship-
ment. Before using the gun, flush it
with solvents so that these materi-
als will be removed from fluid pas-
sages.
OPERATION
Mix, prepare and strain the material to be
sprayed according to the paint maufacturer's
instructions.
Strain material through a 60 or 90 mesh
screen.
1 .
Fill the gravity feed cup with the mate-
rial. Do not overfill. Make sure that the
cup lid vent hole is clear.
2 .
Open the spreader adjustment valve
(20) (Fan) by turning the valve stem
counterclockwise.
3 .
Close the fluid needle adjusting screw
(26) by turning clockwise.
4.
Turn on air supply and set gun inlet
pressure to lowest recommended pres-
sure for material being sprayed. Best
atomization will occur with 10 psig air
cap pressure. However, some materials
can be sprayed at lower pressures,
improving transfer efficiency.
5.
Spray a test area by turning fluid needle
adjusting screw (26) counterclockwise
until a full coat is obtained.
If the finish is too sandy and dry, the material
flow may be too low for the atomization air
pressure being used.
If the finish sags, there is too much material
flowing for the atomization air pressure be-
ing used.
Both of the above can be corrected by
increasing or decreasing the atomization air
pressure or the material flow. Pattern width
can be altered by turning spreader adjust-
ment valve (20), either clockwise to de-
crease the width or counterclockwise to
increase the width.
See Spray Gun Guide, SB-2-001 latest revi-
sion, for details concerning setup of spray
guns.
PREVENTIVE MAINTENANCE
To clean air cap and fluid tip, brush exterior
with a stiff bristle brush. If necessary to
clean cap holes, use a broom straw or
toothpick.
Never use a wire or hard instru-
ment.
This may scratch or burr holes caus-
ing a distorted spray pattern.
To clean fluid passages, remove excess
material from cup, then flush with a suitable
solvent. Wipe gun exterior with a solvent
dampened cloth. Never completely immerse
in solvent as this is detrimental to the lubri-
cants and packings.
Note
When replacing the fluid tip or fluid
needle, replace both at the same
time. Using worn parts can cause
fluid leakage. Tip and needle sets
are available. See Chart 2. Also,
replace the needle packing at this
time. Lightly lubricate the threads
of the fluid tip before reassem-
bling. Torque to 20-25 ft. lbs. Do
not overtighten the fluid tip.
To prevent damage to fluid tip (3)
or fluid needle (3), be sure to ei-
ther 1) pull the trigger and hold
while tightening or loosening the
fluid tip, or 2) remove fluid needle
adjusting screw (26) to relieve
spring
pressure against needle
collar.