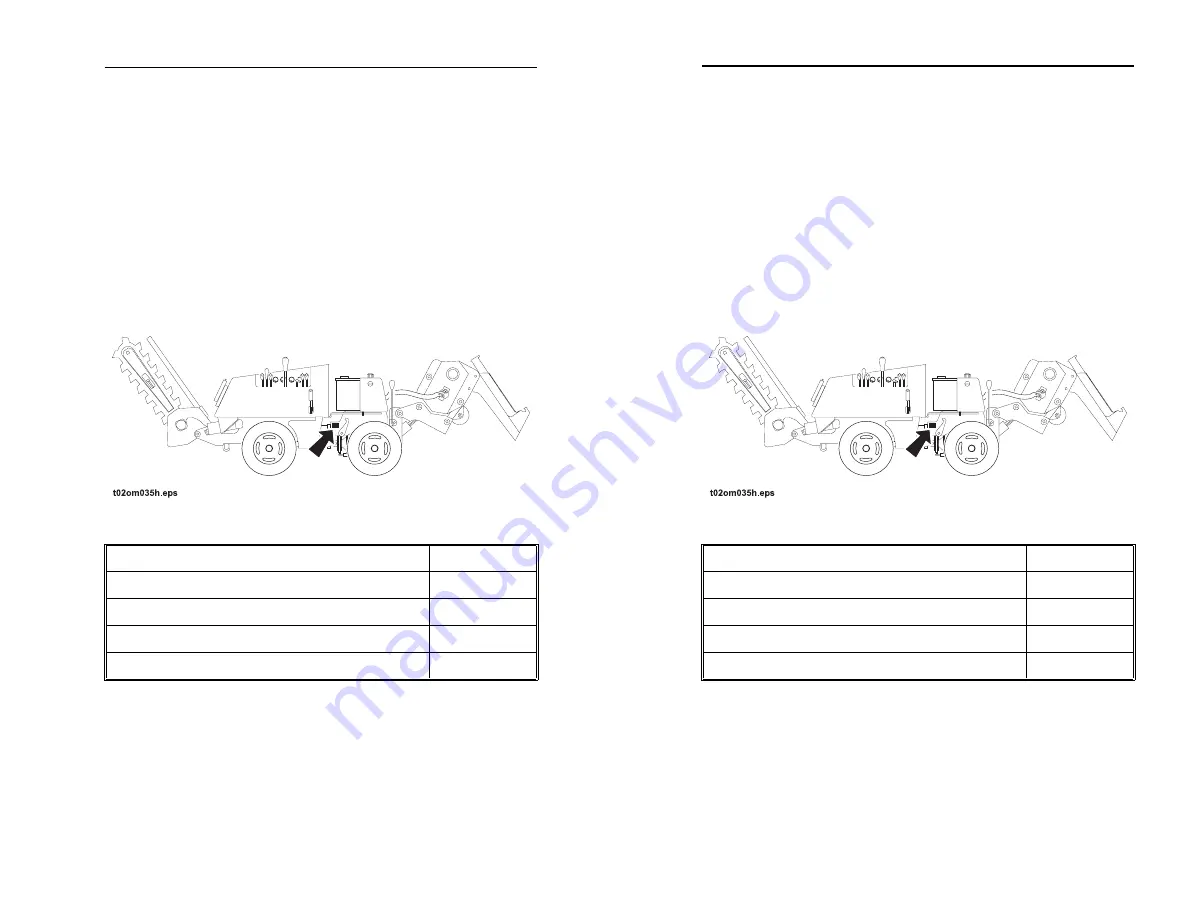
410sx - SUPPORT
1
SERIAL NUMBER
410sx - SUPPORT
1
SERIAL NUMBER
SUPPORT
SERIAL NUMBER
Record the serial number and date of purchase in spaces
provided. Serial number is located on rear section near
articulation joint.
Date of manufacture:
Date of purchase:
Serial number:
Engine serial number:
Trenching attachment serial number
SUPPORT
SERIAL NUMBER
Record the serial number and date of purchase in spaces
provided. Serial number is located on rear section near
articulation joint.
Date of manufacture:
Date of purchase:
Serial number:
Engine serial number:
Trenching attachment serial number
Summary of Contents for 410SX
Page 4: ...4 410sx SUPPORT 4 410sx SUPPORT ...
Page 10: ...10 410sx CONTENTS 10 410sx CONTENTS ...
Page 26: ...26 410sx CONTROLS 26 410sx CONTROLS ...
Page 60: ...60 410sx TRANSPORTATION 60 410sx TRANSPORTATION ...
Page 68: ...68 410sx TRENCHING ATTACHMENT 68 410sx TRENCHING ATTACHMENT ...
Page 120: ...120 410sx SERVICE AS NEEDED SERVICE 120 410sx SERVICE AS NEEDED SERVICE ...
Page 128: ...128 410sx SPECIFICATIONS 128 410sx SPECIFICATIONS ...
Page 131: ...410sx WARRANTY 131 410sx WARRANTY 131 ...
Page 132: ...132 410sx WARRANTY 132 410sx WARRANTY ...
Page 133: ...410sx 133 410sx 133 ...