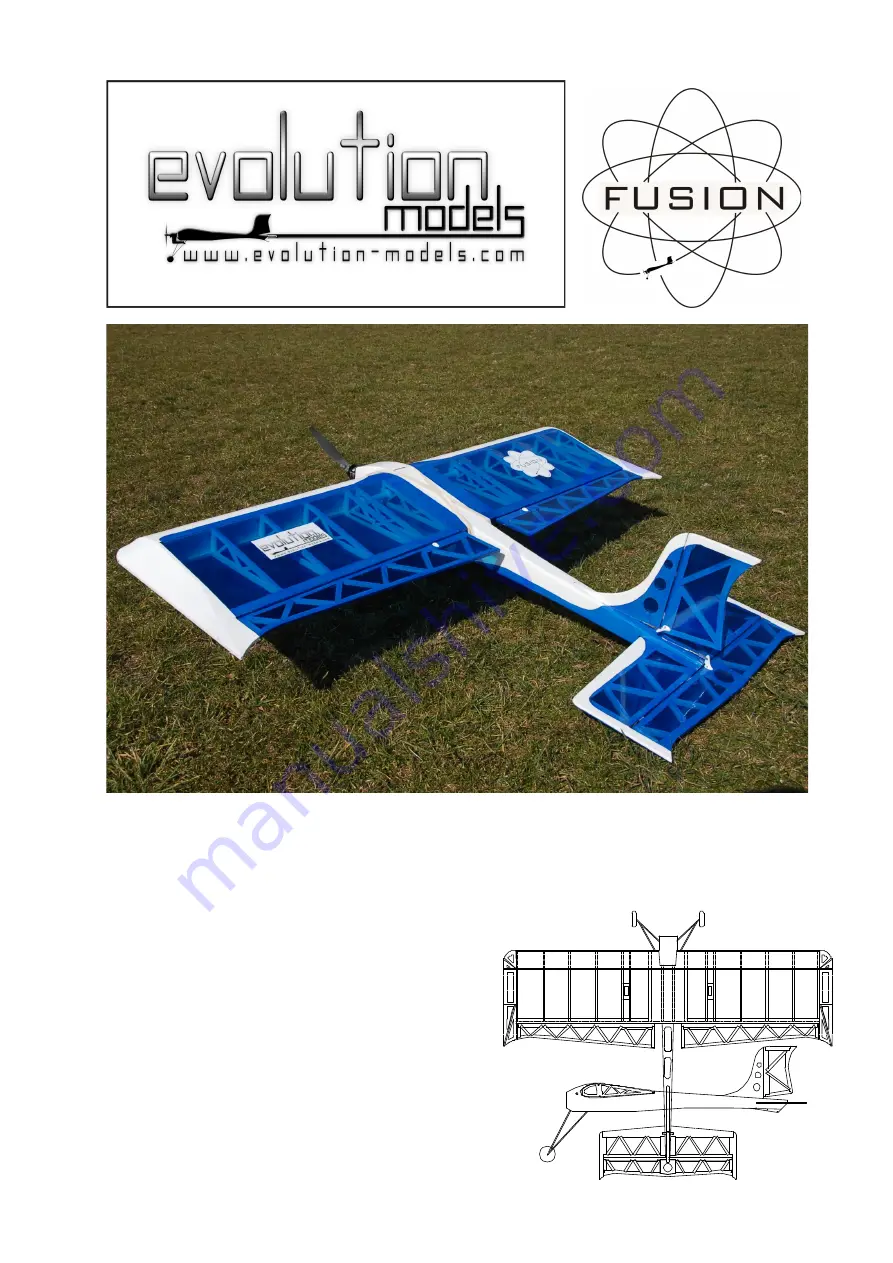
0
Glow and Electric Instruction
Manual
FEATURES
Precision Laser Cut Parts
Lightweight Strong Airframe
Excellent Low Speed Stability
Comprehensive Instruction Manual
High Quality Balsa Ply and Depron parts
Excellent Precise Handling Characteristics
High Quality Comprehensive Hardware Pack