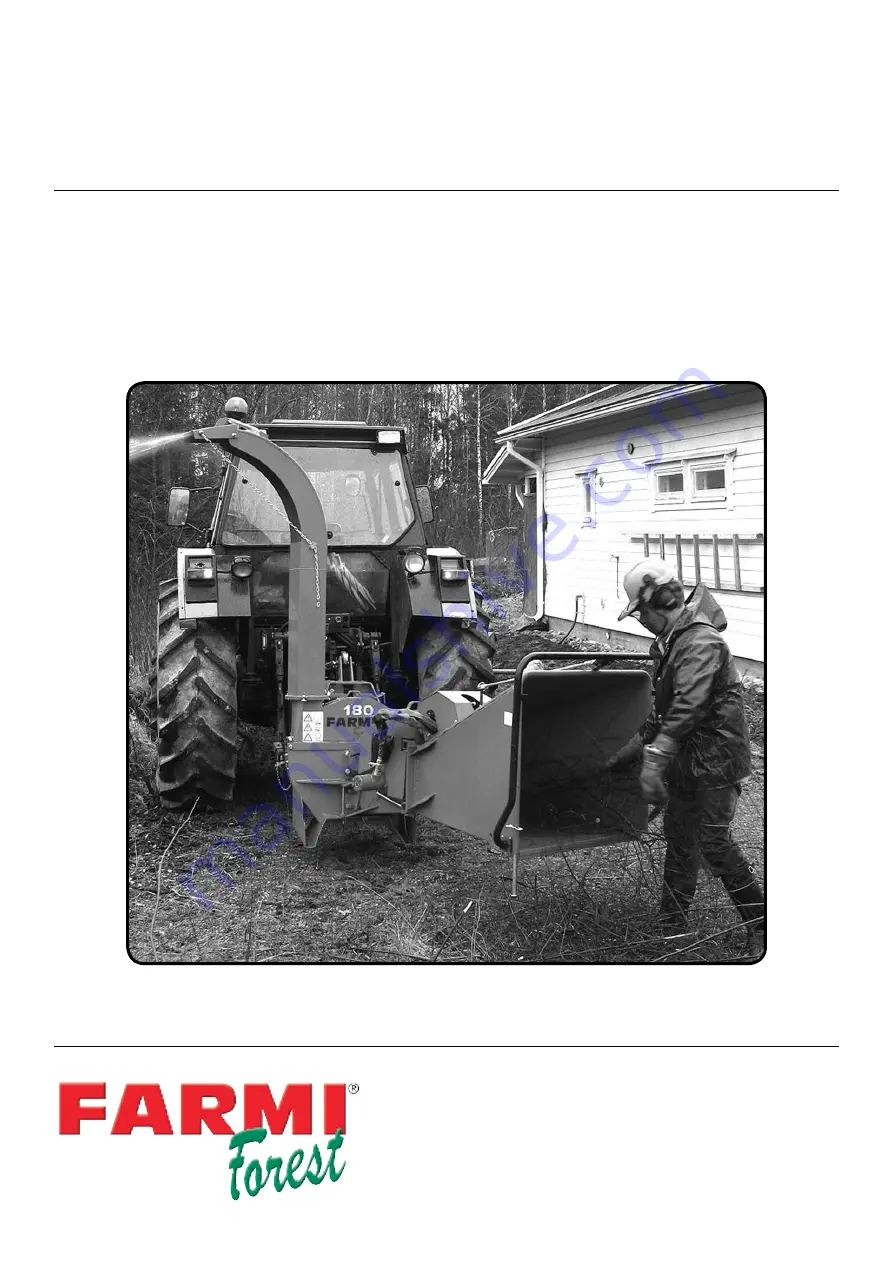
C F180
Farmi Forest Corporation
Ahmolantie 6
FIN-74510 Iisalmi, Finland
Tel. +358 (0)17 83 241
Fax. +358 (0)17 8324 372
www.farmiforest.fi
43514985 A-EN-160610-ER
OPERATION, MAINTENANCE
AND SPARE PARTS MANUAL
READ THIS OPERATION AND MAINTENANCE MANUAL CAREFULLY
BEFORE USING THE MACHINE
FROM MACHINE:
3525078
CHIPPER AND
HYDRAULIC FEEDER
Summary of Contents for CH180HF
Page 51: ......