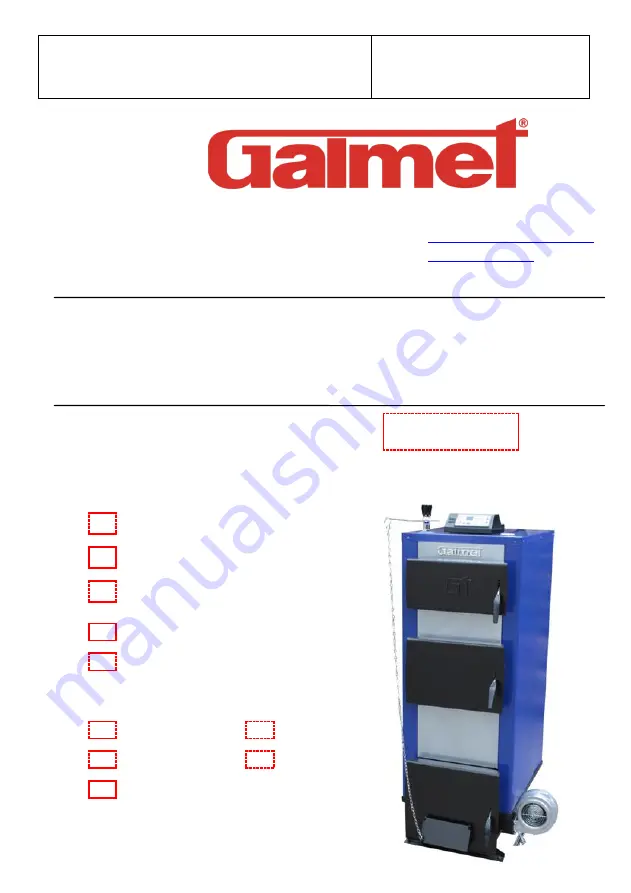
Catalogue No.
KJ
technika grzewcza
boiler servicing: +48 77 40 34 530
controller service: +48 61 43 77 690
tel. 796 067 784
Operation and installation manual
Warranty Card
Please read the instructions before installation and use of the product.
Water boiler for
central heating GT-
kW
with cast iron grate
with water-cooled grate
standard version
with draught regulator
with fan and controller
Controller
Fan
LX EKO pid
MM
LX EKO pid - 2
EW
ST-32 pid
Summary of Contents for KW-10
Page 2: ...2 www galmet com pl ...
Page 3: ...3 ...
Page 4: ...4 ...
Page 5: ...5 ...
Page 23: ...23 ...