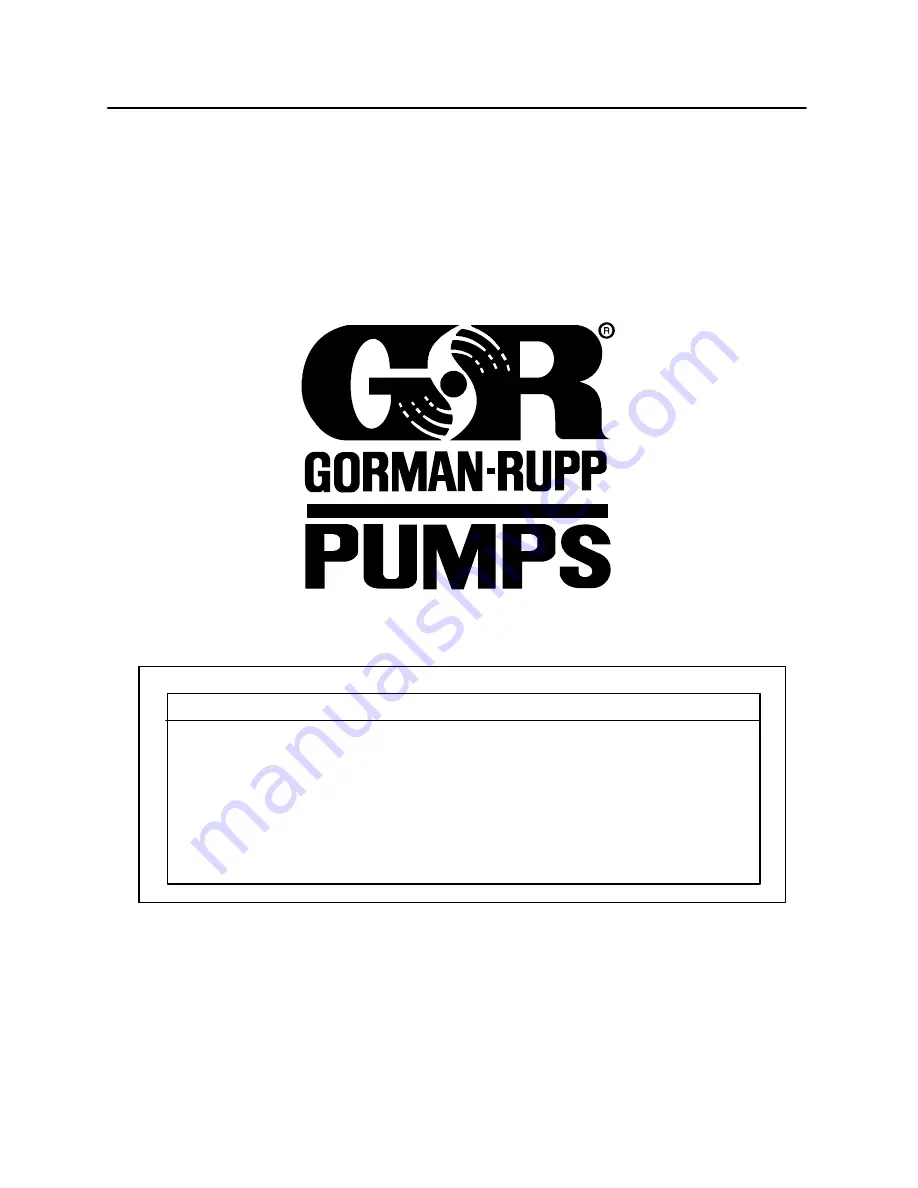
OM−05229−OM01
February 22, 2001
Rev. C 05-30-03
CER
THE GORMAN-RUPP COMPANY
MANSFIELD, OHIO
GORMAN-RUPP OF CANADA LIMITED
ST. THOMAS, ONTARIO, CANADA
Printed in U.S.A.
Copyright by the Gorman-Rupp Company
INSTALLATION, OPERATION,
AND MAINTENANCE MANUAL
WITH PARTS LIST
SUBMERSIBLE PUMPS
MODEL
JSV3H60−E5 230/1