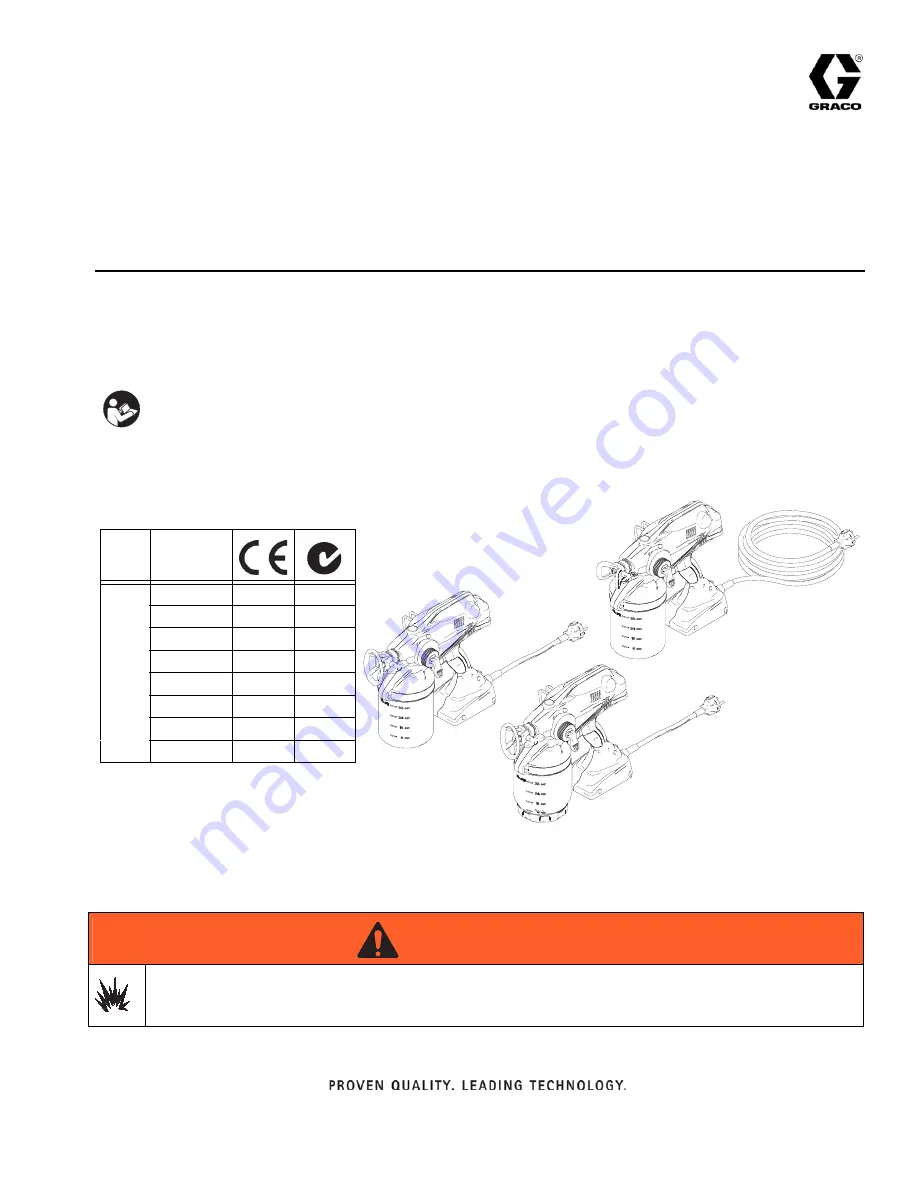
ti19609a
3A2854G
EN
Operation - Repair - Parts
Electric Hand-Held Paint Sprayers
- For portable spray applications of architectural paints and coatings only
-
- Not approved for use in explosive atmosphere locations -
All Models:
Maximum Working Pressure 2000 psi (14 MPa, 138 bar)
IMPORTANT SAFETY INSTRUCTIONS
Read all warnings and instructions in this
manual. Save these instructions.
Model
230V
16N661
16N662
16N663
16N667
16P122
16W104
17C242
17C811
WARNING
WARNING
WARNING
WARNING
Use only water-based materials.
Do not use materials which state “FLAMMABLE” on the packaging. For
more information about your material, request MSDS from distributor or retailer.
Summary of Contents for 16N661
Page 31: ...Notes 3A2854G 31 Notes ...