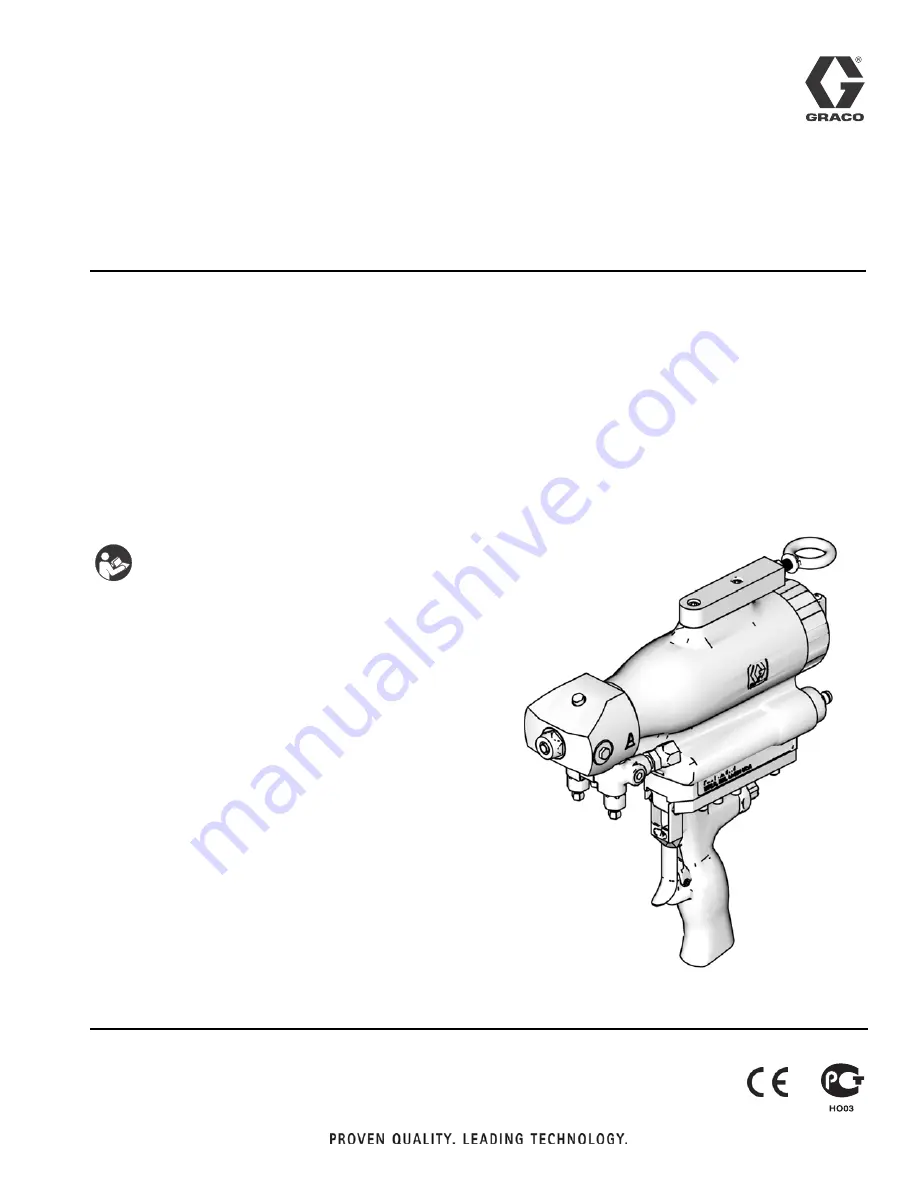
Instructions - Parts
EP
™
Gun
Plural Component, Impingement Mix, Mechanical Purge Pour Gun
with Throat Seal Liquid
™
Technology
For use with non-flammable foam. Not for use in explosive atmospheres.
Model 257999, 24C932, 24C933, 24C934
3000 psi (20.7 MPa, 207 bar) Maximum Fluid Working Pressure
80-100 psi (0.55-0.69 MPa, 5.5-6.9 bar) Air Inlet Pressure Range
180°F (82°C) Maximum Fluid Temperature
US Patent Pending
Important Safety Instructions
Read all warnings and instructions in this
manual. Save these instructions.
TI14450a
313872B
ENG