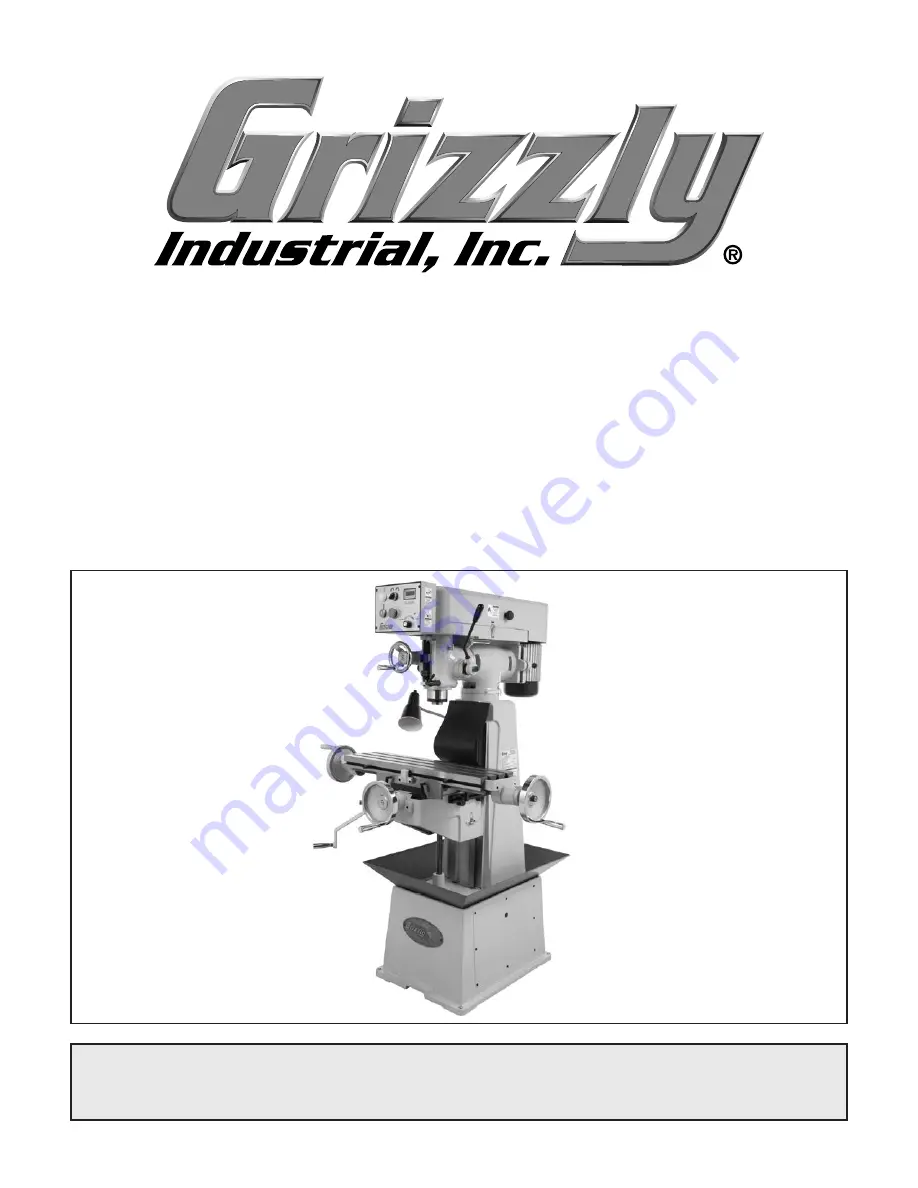
COPYRIGHT © SEPTEMBER, 2008 BY GRIZZLY INDUSTRIAL, INC., REVISED JANUARY, 2021 (MN)
WARNING: NO PORTION OF THIS MANUAL MAY BE REPRODUCED IN ANY SHAPE
OR FORM WITHOUT THE WRITTEN APPROVAL OF GRIZZLY INDUSTRIAL, INC.
#TS10934 PRINTED IN TAIWAN
V2.01.21
MODEL G0678
VARIABLE SPEED 8" X 30"
VERTICAL MILL
OWNER'S MANUAL
(For models manufactured since 06/15)