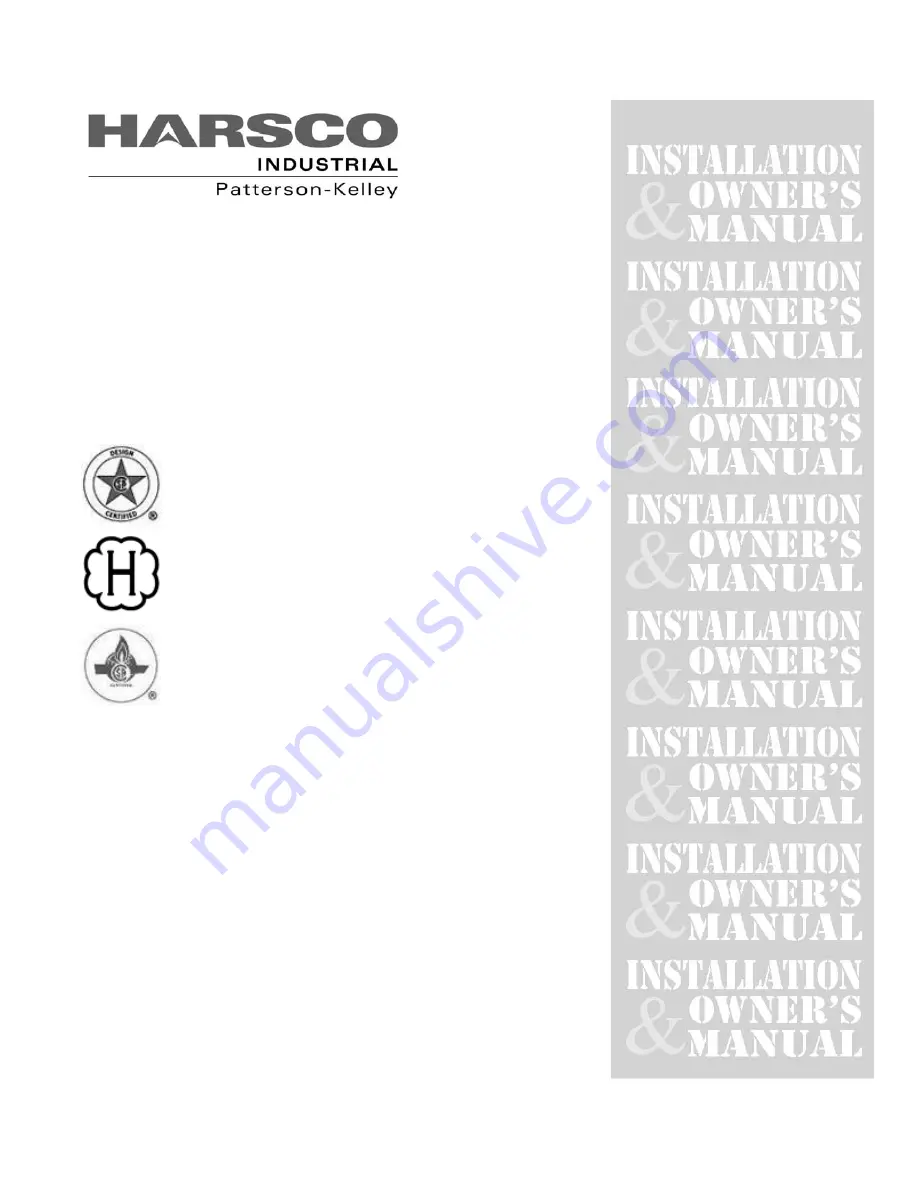
© 2011 Harsco Corporation, All Rights Reserved
MFD 202
MODU-FIRE
®
FORCED DRAFT
GAS-FIRED BOILER
2500 - 3000
Model #:_______
Serial #______________________
Start-Up Date: _______________________
Harsco Industrial, Patterson-Kelley
100 Burson Street
East Stroudsburg, PA 18301
Telephone: (570) 476-7261
Facsimile: (570) 476-7247
www.harscopk.com
C.S.A. Design-Certified
Complies with ANSI Z21.13/CSA 4.9
Gas-Fired Low Pressure Steam and Hot Water Boilers
ASME Code, Section IV
Certified by Harsco Industrial, Patterson-Kelley
C.S.A. Design-Certified
Complies with ANSI Z21.13/CSA 4.9
Gas-Fired Low Pressure Steam and Hot Water Boilers
MODU-FIRE® FD 2500-3000
Rev. 1.01 (2/7/12)
Summary of Contents for 1004905923
Page 2: ...MODU FIRE Forced Draft Gas Fired Boiler 2500 3000 2 ...
Page 45: ...MODU FIRE Forced Draft Gas Fired Boiler 2500 3000 45 6 1 3 Wiring Schematic ...
Page 48: ...MODU FIRE Forced Draft Gas Fired Boiler 2500 3000 48 6 1 6 Rear Junction Box ...
Page 49: ...MODU FIRE Forced Draft Gas Fired Boiler 2500 3000 49 6 1 7 Customer Connections ...
Page 56: ...MODU FIRE Forced Draft Gas Fired Boiler 2500 3000 56 ...