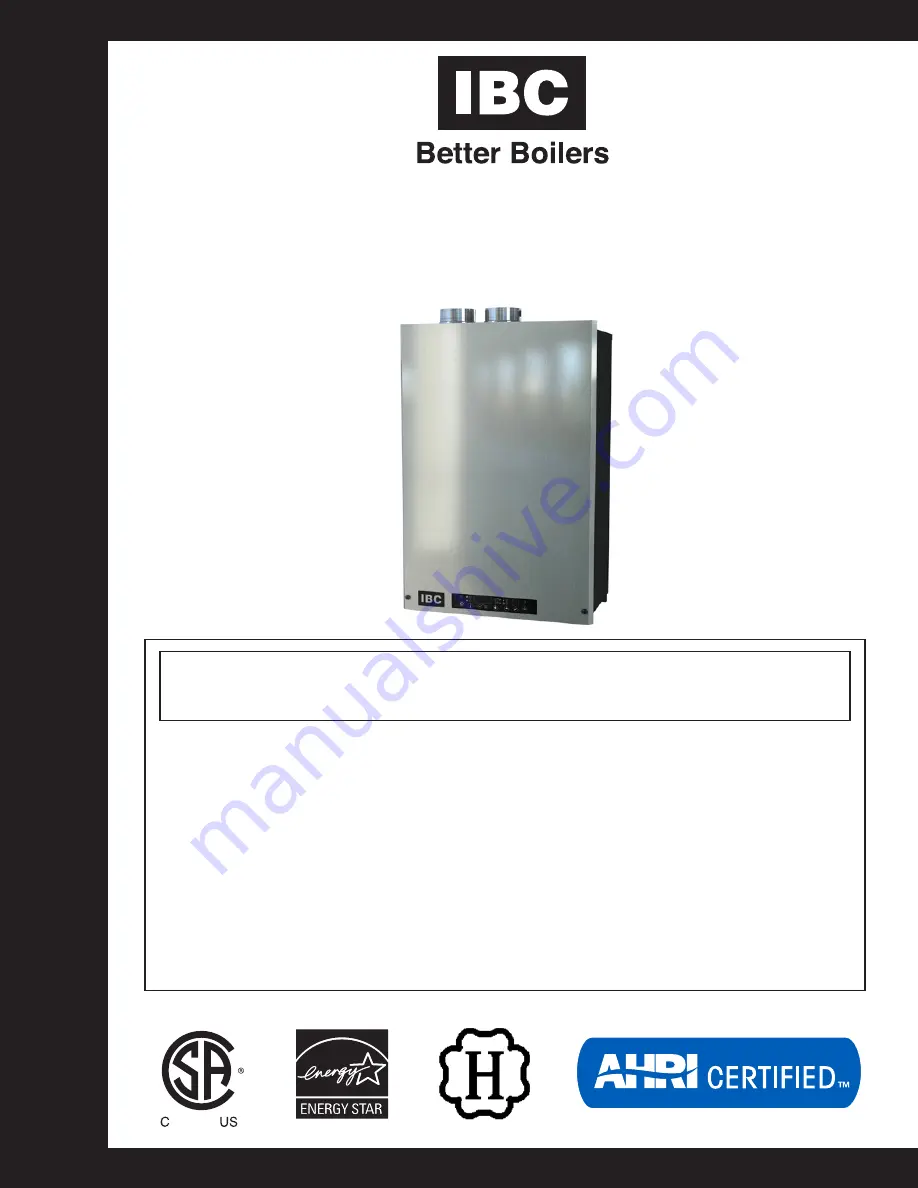
INST
ALLA
TION AND OPERA
TING INSTR
UCTIONS
www.ibcboiler.com
HC Series Boilers
HC 13-50, HC 23-84, HC 29-106, HC 33-124, HC 20-125, HC 33-160
(Natural Gas or Propane)
WARNING: If the information in this manual is not followed exactly, a fire or
explosion may result causing property damage, personal injury, or loss of life.
Do not store or use gasoline or other flammable vapours and liquids or other
combustible materials in the vicinity of this or any other appliance.
WHAT TO DO IF YOU SMELL GAS:
•
Do not try to light any appliance.
•
Do not touch any electrical switch; do not use any phone in your building.
•
Immediately call your gas supplier from a nearby phone. Follow the gas
supplier’s instructions.
•
If you cannot reach your gas supplier, call the fire department.
Installation and service must be performed by a qualified installer, service
agency or the gas supplier.
This Manual is also available in French - contact IBC or visit our web site www.ibcboiler.com