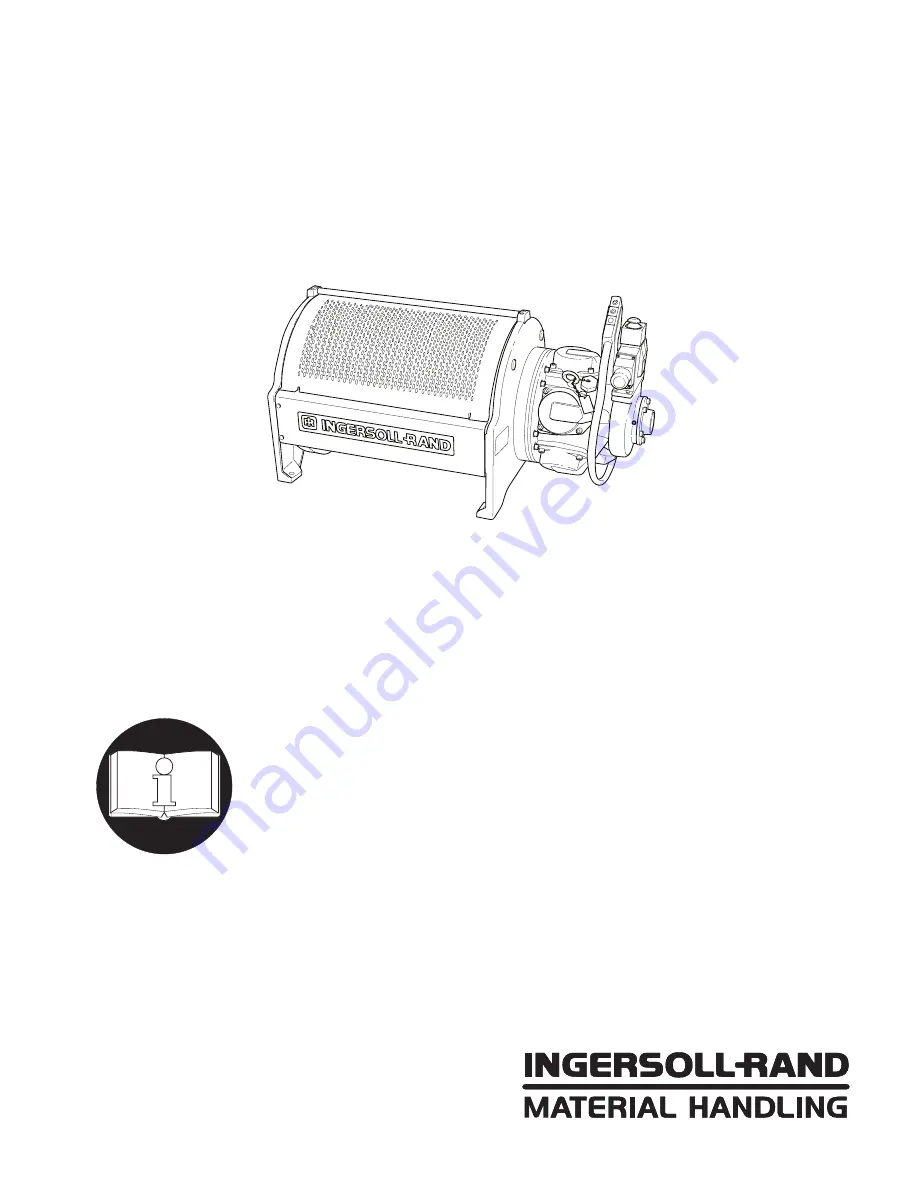
Form MHD56111
Edition 2
March 1997
71296438
©
1997 Ingersoll-Rand Company
Form MHD56111
MODEL FA5A AIR WINCH
SUPPLEMENTAL SERVICE
AND MAINTENANCE INSTRUCTIONS
This manual contains important service and maintenance information.
Make this manual available to all persons responsible for the service
and maintenance of these products.
Always operate, inspect and maintain this winch in accordance with American National
Standards Institute Safety Code (ASME B30.16) and any other applicable safety codes and
regulations.
Refer all communications to the nearest Ingersoll-Rand Material Handling Office or
Distributor.
Summary of Contents for FA5A
Page 10: ...10 DISC BRAKE PARTS DRAWING Dwg MHP0667 Dwg MHP0630 One Way Clutch Detail Section 1...
Page 19: ...19 Section 2 SERVICE NOTES...
Page 54: ...54 REDUCTION GEAR ASSEMBLY PARTS DRAWING Dwg MHP1221 Section 5...
Page 57: ...57 SERVICE NOTES...
Page 58: ...58 SERVICE NOTES...
Page 59: ...59 SERVICE NOTES...