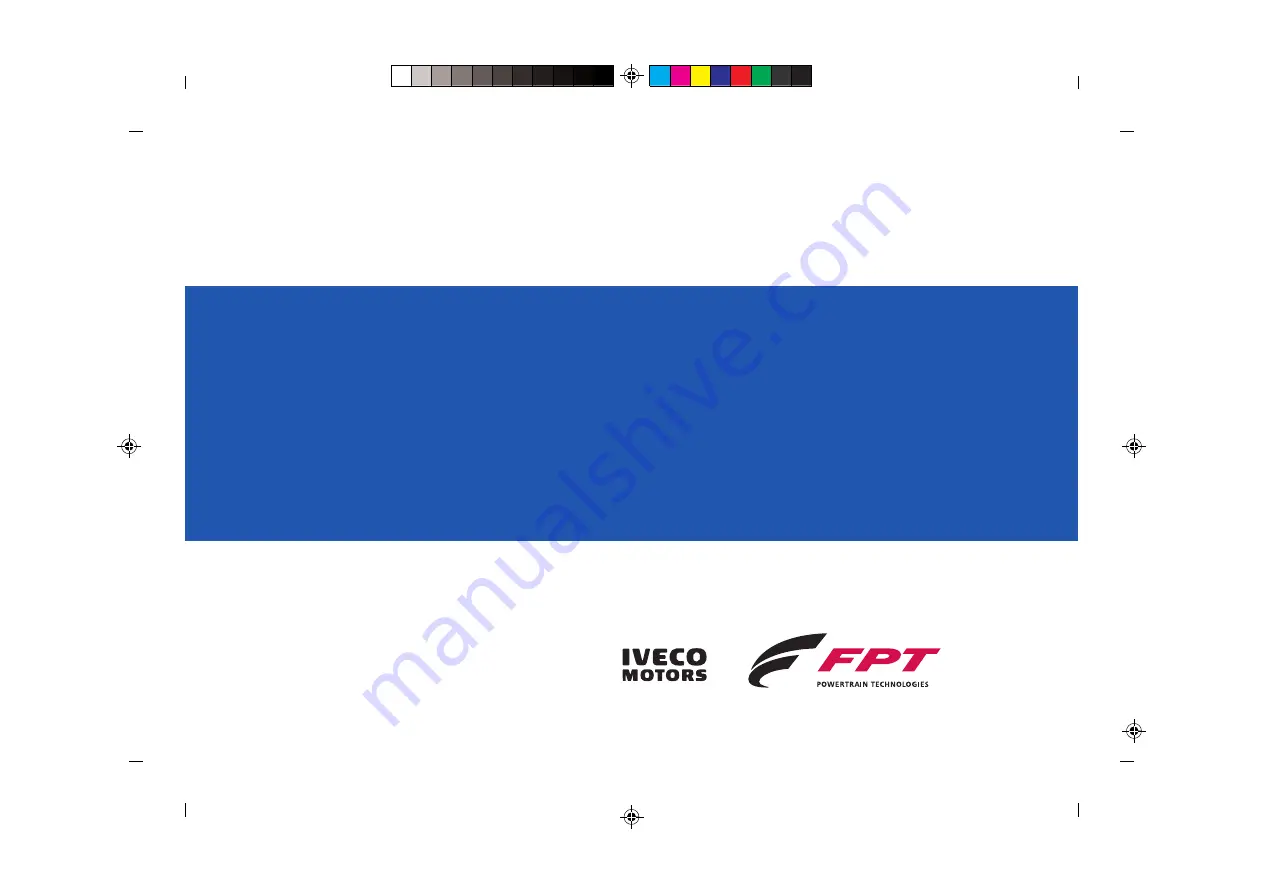
copertina NEF series electronic 20-11-2006 10:04 Pagina 1
Colori compositi
C
M
Y
CM
MY
CY CMY
K
USE AND MAINTENANCE
USO E MANUTENZIONE
UTILISATION ET ENTRETIEN
BETRIEB UND WARTUNG
USO Y MANTENIMIENTO
NEF
S
ERIES
E
LECTRONIC
I
NJECTION
S
YSTEM
Publication edited by
Marketing - Adv. & Promotion
Print L31900018 - 10/06
MARINE ENGINES