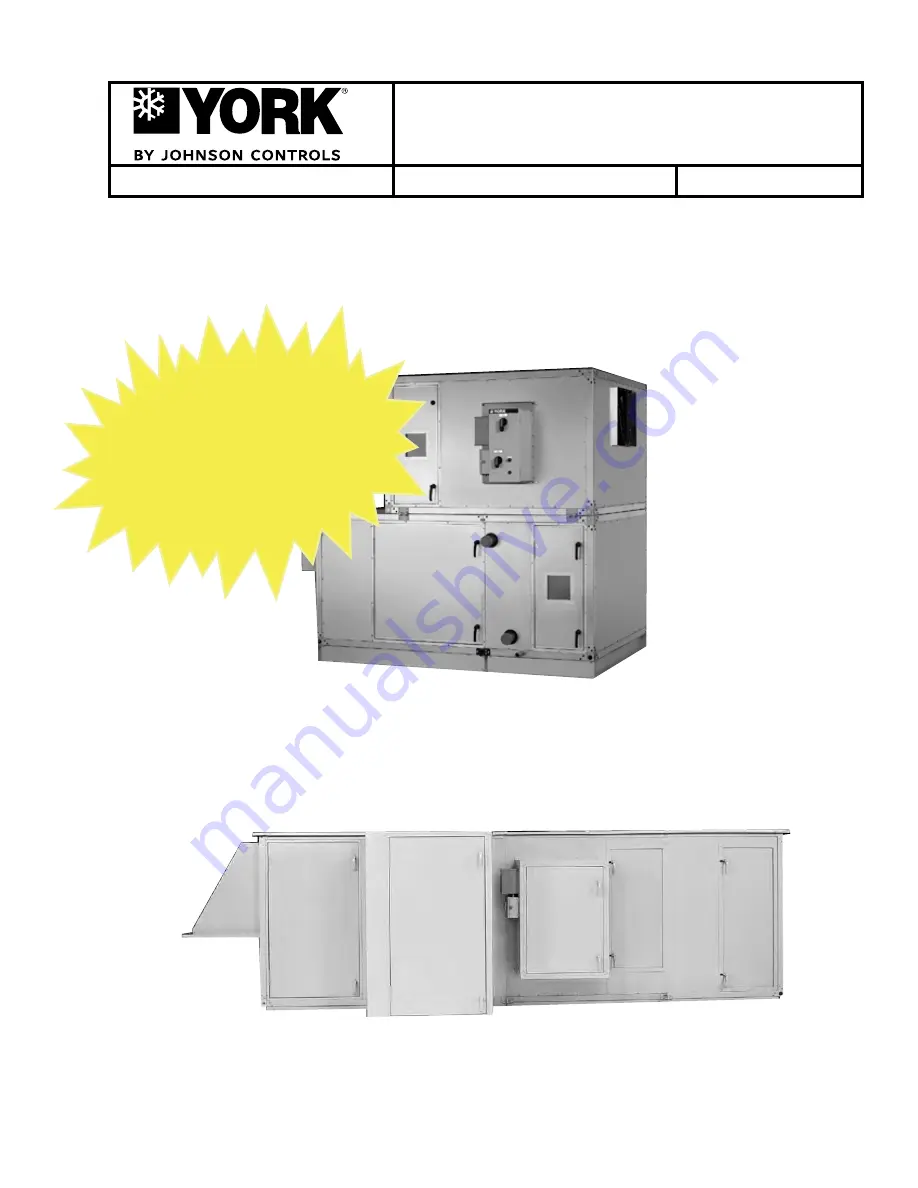
InstallatIon and staRtUP InstRUCtIons
YORK SOlutiOn
AiR hAndling unitS
Supersedes 102.20-N1 (1108)
Form 102.20-N1 (1109)
OutdOOR unit
indOOR unit
LD09624
LD09688
YORK SOlutiOn indOOR And OutdOOR MOdElS
Renewal Parts
Form 102.20-RP1
With P/
n contact Balt. Parts
(800) 932-1701
Manufactured or specialty parts
contact
Airside (800) 545-7814
Summary of Contents for YORK SOLUTION LD09624
Page 4: ...johnson controls 4 FORM 102 20 N1 1109 THIS PAGE INTENTIONALLY LEFT BLANK ...
Page 10: ...johnson controls 10 FORM 102 20 N1 1109 THIS PAGE INTENTIONALLY LEFT BLANK ...
Page 16: ...johnson controls 16 FORM 102 20 N1 1109 THIS PAGE INTENTIONALLY LEFT BLANK ...
Page 30: ...johnson controls 1 8 FORM 102 20 N1 1109 THIS PAGE INTENTIONALLY LEFT BLANK ...
Page 106: ...johnson controls 2 76 FORM 102 20 N1 1109 THIS PAGE INTENTIONALLY LEFT BLANK ...