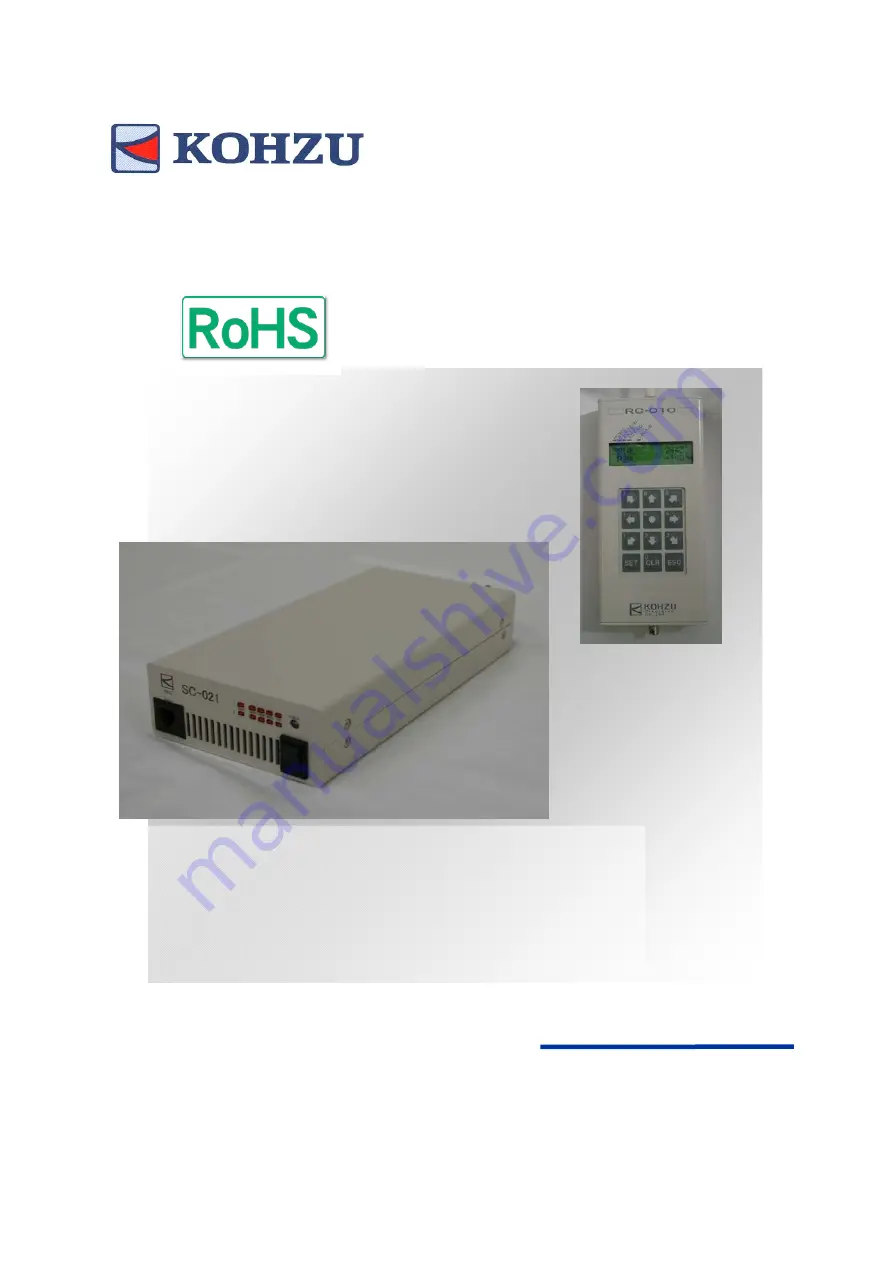
Stepping Motor Controller
SC-021 RC-010
Pioneering the door to the future with a commitment to technology
KOHZU Precision Co., Ltd.
Introduction Manual
●
Thank you for purchasing this product.
●
Before operating this product, carefully review this Manual in its entirety
to ensure its proper and safe use. Always keep this Manual in a
convenient location, for future reference.
Ver. 1.00
Note: this version does not correspond with
the latest controller version.