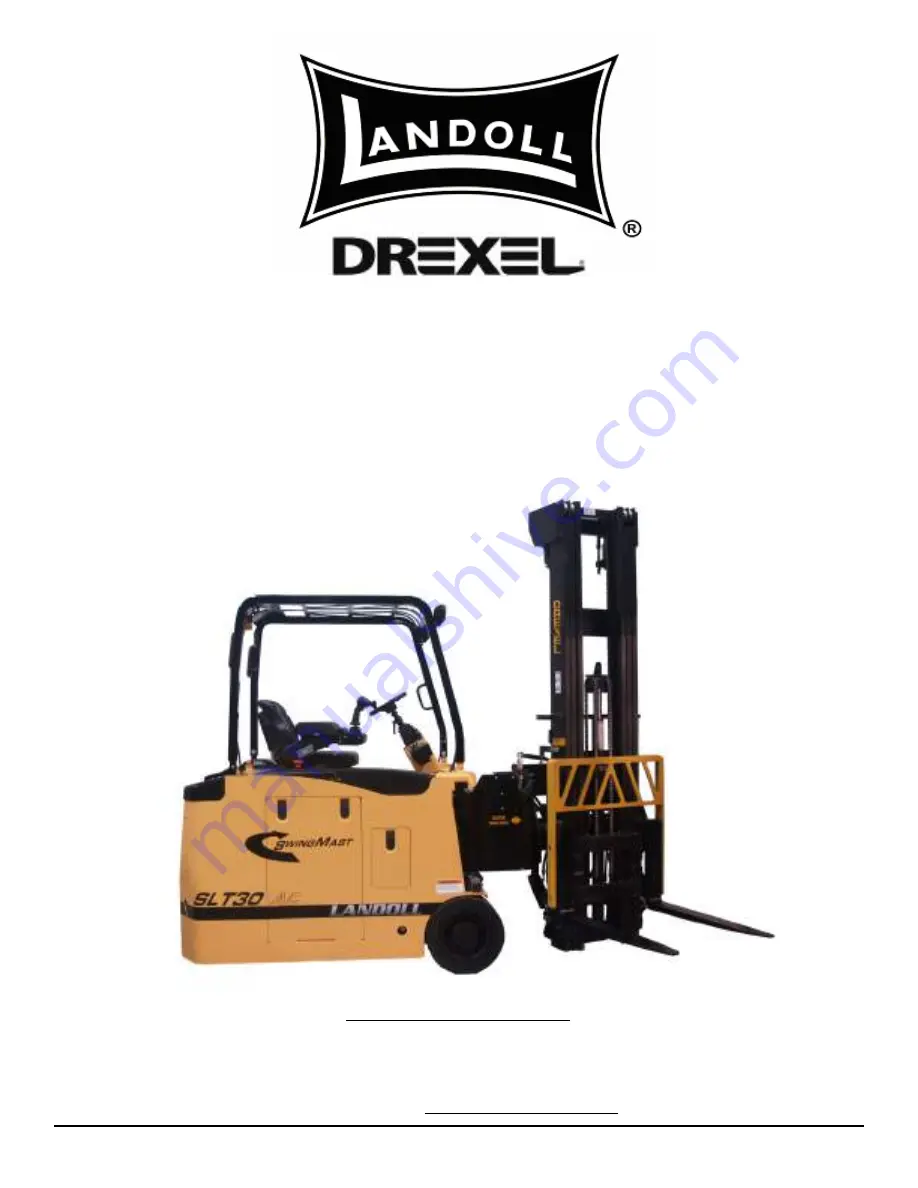
F-459-R1
LANDOLL CORPORATION
1900 North Street
Marysville, Kansas 66508
(785) 562-5381
800-428-5655 ~ WWW.LANDOLL.COM
Model SLT30/35 AC
Maintenance Manual
https://www.forkliftpdfmanuals.com/
F-459-R1
LANDOLL CORPORATION
1900 North Street
Marysville, Kansas 66508
(785) 562-5381
800-428-5655 ~ WWW.LANDOLL.COM
Model SLT30/35 AC
Maintenance Manual
https://www.forkliftpdfmanuals.com/