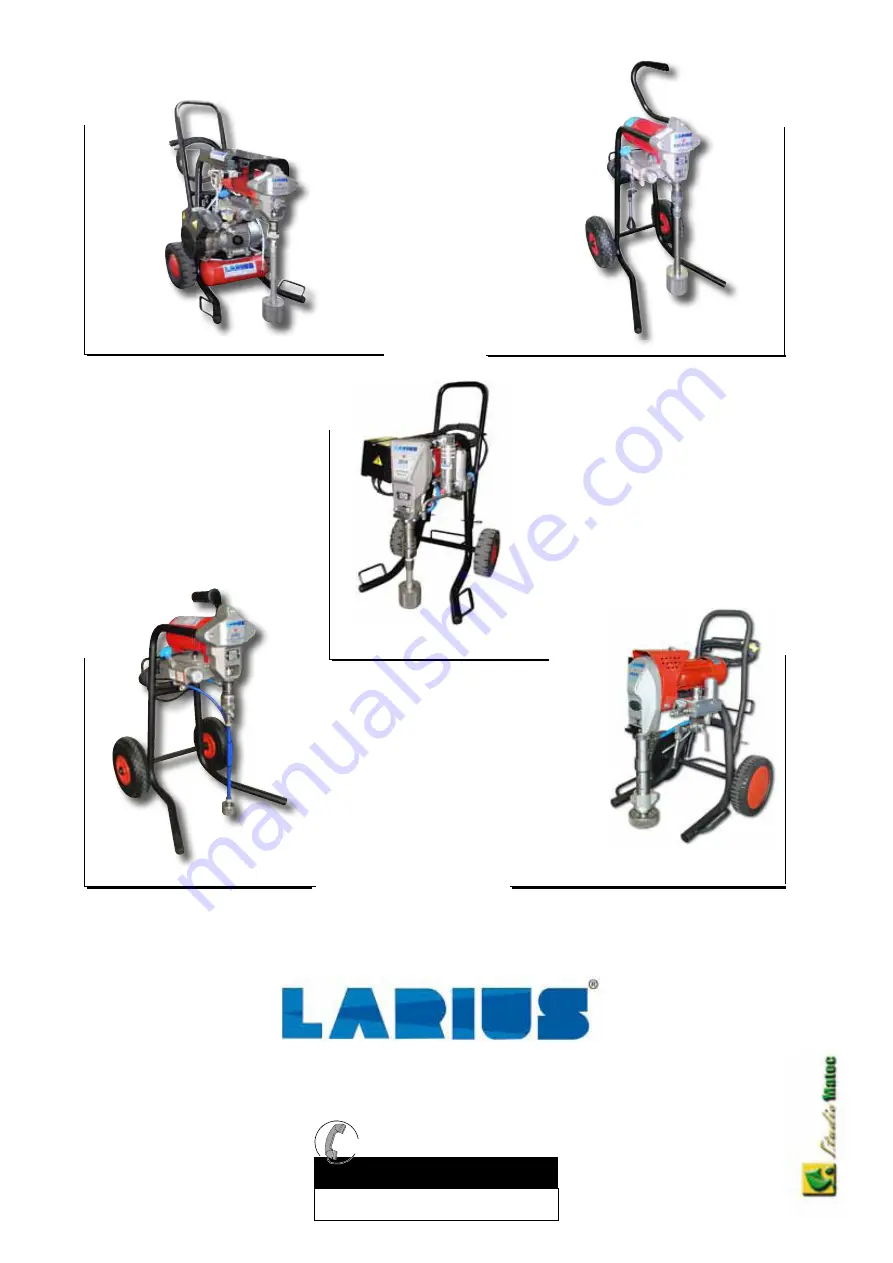
23801 CALOLZIOCORTE - LECCO - ITALY - Via Antonio Stoppani, 21
Tel. (39) 0341/62.11.52 - Fax (39) 0341/62.12.43
E-mail: larius@larius.com - Internet http://www.larius.com
MANUFACTURER:
DIRECT LINE
Tel. (39) 0341/621256
Fax (39) 0341/621234
CUSTOMERS TECHNICAL SERVICE
AIRLESS PISTON PUMPS
THOR 220V/50Hz long pump unit
Rif. 20705
THOR 220V/50Hz short pump unit
Rif. 20700
JOLLY
Rif. 56501
NEW EXCALIBUR version on trolley
Rif. 18776
NEW EXCALIBUR top finish
Rif. 18783
ZEUS
Rif. K35100
R version on trolley
Rif. 18776
LIBUR
finish
Rif. 18783