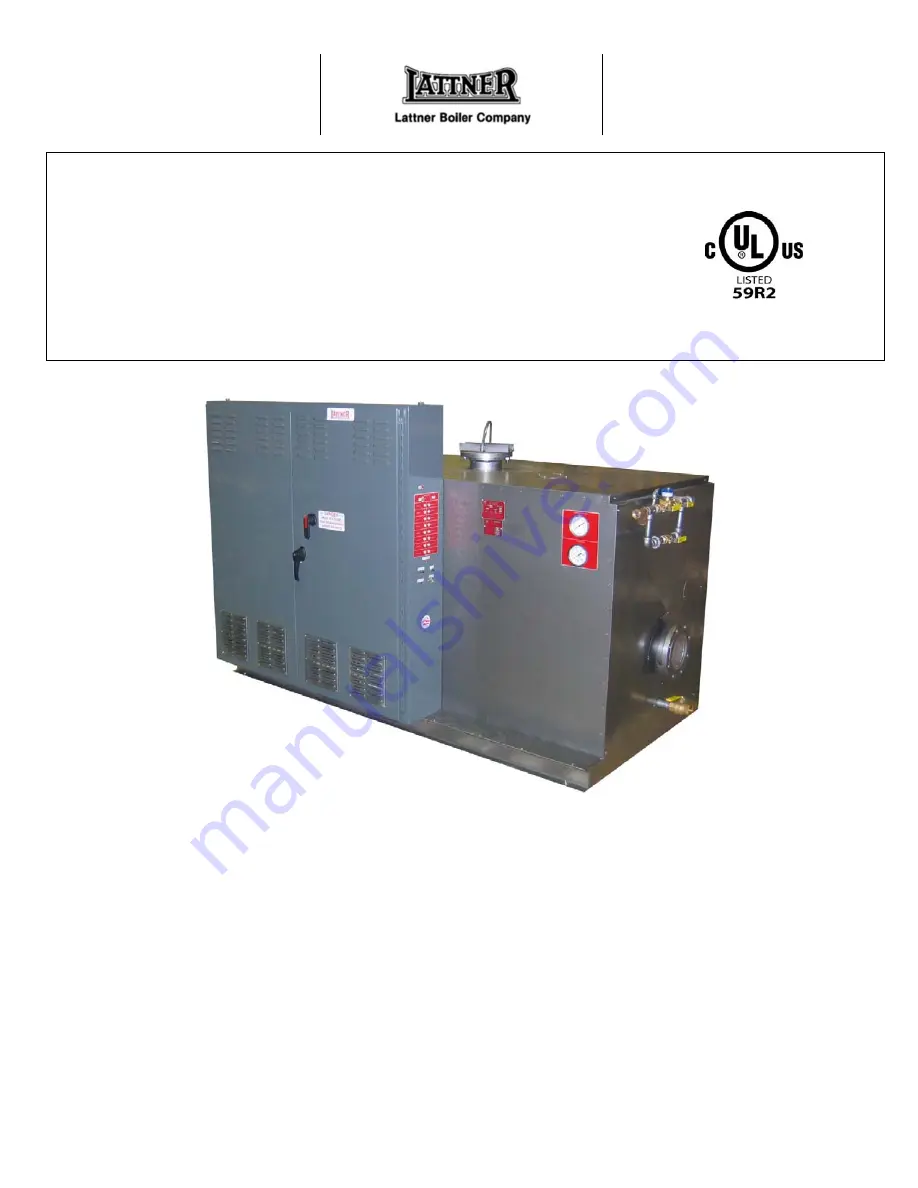
INSTALLATION, MAINTENANCE,
AND SERVICE MANUAL
ELECTRIC HOT WATER BOILERS
(LW, HW)
INDEX
General Information
Page 1
Installation
Page 2
Typical Piping Diagram
Page 2
Operation & Controls
Page 3
Construction Page
3
Start Up
Page 4
Maintenance Page
4
Element Replacement
Page 5
Troubleshooting
Literature Index
Page 6
Page 7
GENERAL INFORMATION
Vessel Construction
– All vessels registered with the
National Board of Boiler and Pressure Vessel Inspectors;
Data reports are furnished. Comply with Section IV, ASME
Code, stamped with “H”. Maximum design temperature and
pressure is 250 degrees F and 160 psi if model “LW” boiler.
Vessels above 250 degrees F and/or above 160 psi are
designed to ASME Section I or Section VII and are
stamped “S” or “U”; model number designation is “HW”.
Heating Elements
– Removable, incoloy sheathed electric
heating elements are mounted in 150 lb. ASME blind
flanges with plated steel compression fittings. Complete
flange assembly is inserted horizontally into vessel and
bolted in place.
UL Listing
– Under file No. E30432 up to 600 volts.
Enclosure
– Heavy gauge steel control panel and steel
vessel enclosure are attached to a steel frame, mounted on
a 4” channel base. All surfaces are protected against
corrosion with durable baked finish.
Insulation
– Minimum 4” fiberglass on all sides. Minimizes
heat loss from vessel and keeps enclosure temperature
cooler.
1