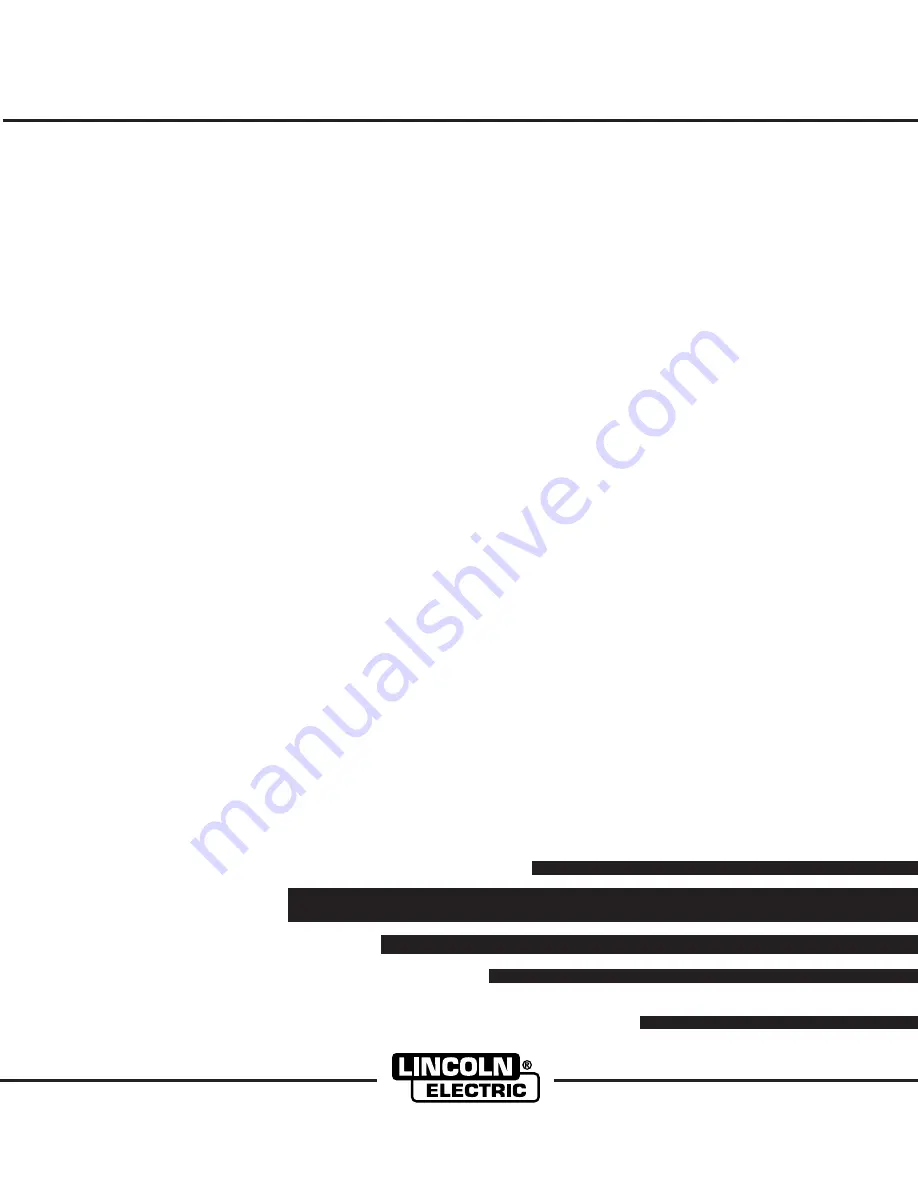
MASTER LOAD 750
OPERATORS MANUAL
IM575
May, 2006
Safety Depends on You
Lincoln arc welding and cutting
equipment is designed and built
with safety in mind. However, your
overall safety can be increased by
proper installation ... and thought-
ful operation on your part.
DO
NOT INSTALL, OPERATE OR
REPAIR THIS EQUIPMENT
WITHOUT READING THIS
MANUAL AND THE SAFETY
PRECAUTIONS CONTAINED
THROUGHOUT.
And, most
importantly, think before you act
and be careful.
For use with equipment code number 10401.
™
• Sales and Service through Subsidiaries and Distributors Worldwide •
Cleveland, Ohio 44117-1199 U.S.A. TEL: 216.481.8100 FAX: 216.486.1751 WEB SITE: www.lincolnelectric.com
• World's Leader in Welding and Cutting Products •
Copyright © 2005 Lincoln Global Inc.
Summary of Contents for MASTER LOAD 750
Page 18: ...10 DIAGRAMS 10 MASTER LOAD 750 D26300 3 5 97 MASTERLOAD 750 WIRING DIAGRAM ...
Page 19: ...11 DIAGRAMS MASTER LOAD 750 11 SB2561 2 22 96 MASTERLOAD 750 DIMENSION PRINT ...
Page 20: ...PARTS MASTER LOAD 750 D26244 SHT 1 2 3 6 97 MASTERLOAD 750 GENERAL ASSEMBLY ...
Page 23: ...NOTES ...
Page 24: ...NOTES ...
Page 25: ...NOTES ...