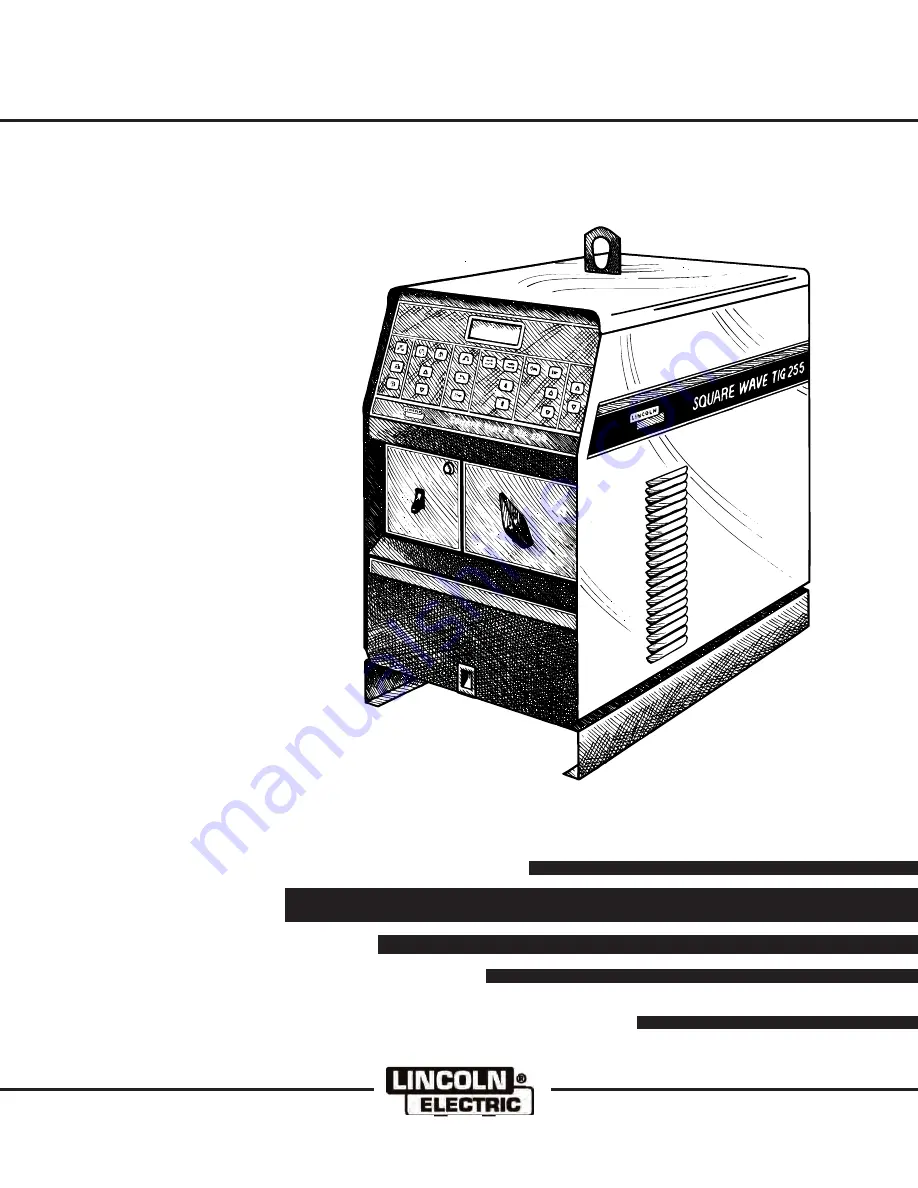
SQUARE WAVE TIG 255
OPERATOR’S MANUAL
Sales and Service through Subsidiaries and Distributors Worldwide
22801 St. Clair Ave. Cleveland, Ohio 44117-1199 U.S.A. Tel. (216) 481-8100
World's Leader in Welding and Cutting Products
Premier Manufacturer of Industrial Motors
IM520-B
January, 1997
Safety Depends on You
Lincoln arc welding and cutting
equipment is designed and built
with safety in mind. However,
your overall safety can be
increased by proper installation ...
and thoughtful operation on your
part.
DO
NOT
INSTALL,
OPERATE OR REPAIR THIS
EQUIPMENT
WITHOUT
READING THIS MANUAL AND
THE SAFETY PRECAUTIONS
CONTAINED THROUGHOUT.
And, most importantly, think
before you act and be careful.
For use with machines having Code Number 10022 thru 10026 & 10134, 10451,10452,10453.