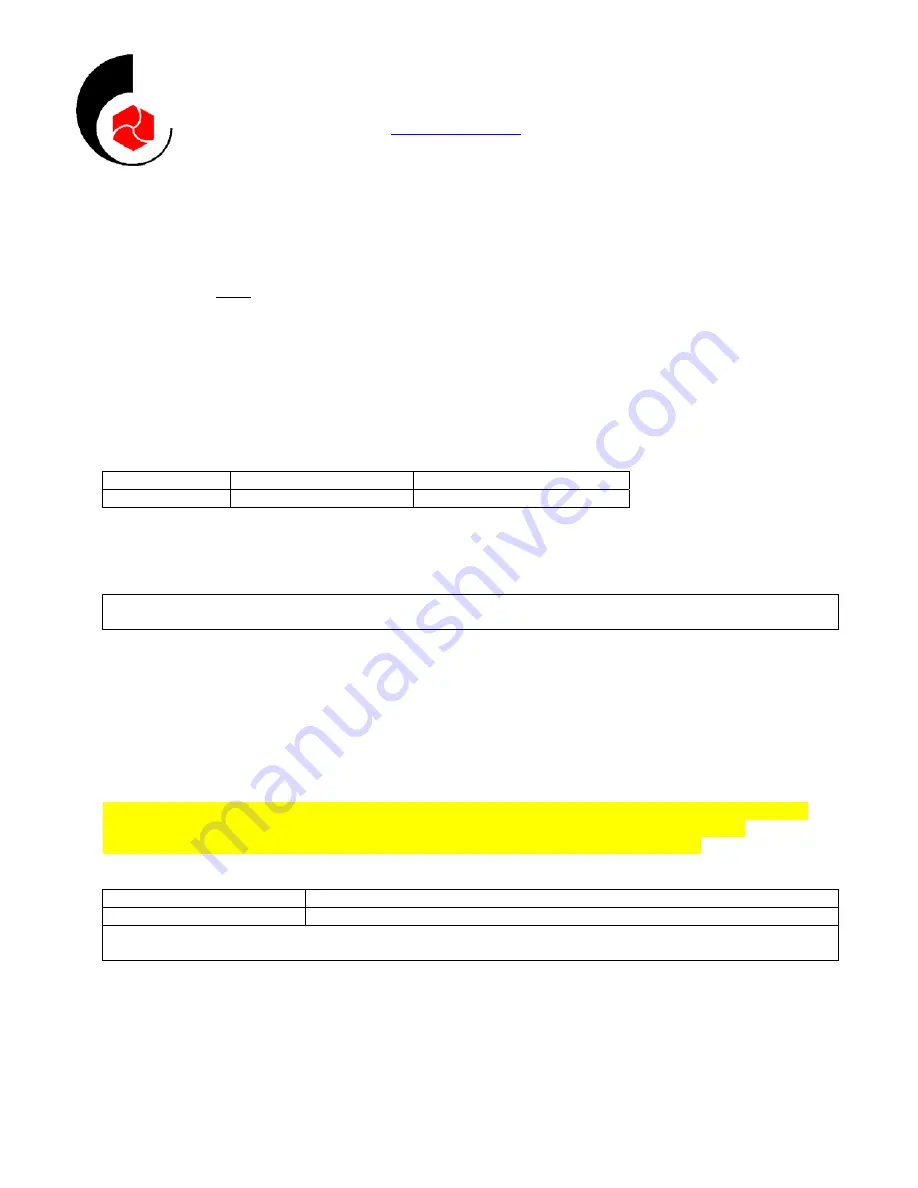
15150 25th Avenue North, Minneapolis, MN 55447-1981
Phone 763-476-8600 Fax 763-476-4092
For Service: MN 763-476-4191 IA 319-632-4288 NE 402-330-2323
Visit us at:
Productivity is ISO 9001:2000 Certified
Productivity Inc
®
Makino EDGE-2 PRE-INSTALLATION CHECKLIST
– Rev 01/2009
Installation of your new Makino EDGE-2 can be smooth and rapid if preparations are made prior to the delivery of
your machine. Any questions regarding machine installation should be directed to our service department for
clarification. We hope this checklist will aid in a rapid installation of your new machine.
NOTE: The following
must be completed prior to our service technician arriving to install your new machine.
¾
Power Requirements for your machine: 30 Amp/3 phase/9kVa
*Voltage of 200 to 480 at +/- 10% must be maintained. If not, an Automatic Voltage Regulator should be used.
Proper voltage per machine specifications should be ready at machine site.
Do NOT power up the machine.
See Makino Installation Manual for more information, or contact our Service Department with any
questions.
¾
Customer should furnish and have available the proper supply and types of lubricants required for machine
operation.
ITEM CAPACITY
FLUID
TYPE
Dielectric Oil
52.8 Gal
IONO Plus+
You will need to have Dielectric Oil on hand for installation. Contact our Service Department for more
information.
¾
Air lines should be routed to the machine location and operational for proper air pressure.
Clean, Dry Compressed Air of 70 psi. must be available; less than 40% relative humidity; In-line water trap
recommended.
¾
Machine location should be planned to allow enough room for access panels to be opened and serviced with
ease. A minimum of 36” is required around the machine for operator and maintenance access.
¾
Weight requirements should be checked to insure that the surface below the machine will have sufficient
strength for support and stability. The machine must be set on a solid, sound and stable, steel bar-reinforced
concrete slab poured directly on the grade. In general, the 6” concrete floor on industrial buildings is suitable
for machine placement.
¾
The EDGE-2 is best moved with a forklift. See Makino Installation Manual for lifting instructions.
**NOTE 1: LIFTING EQUIPMENT, ROPES, SCHACKLES, LIFTING BARS, LIFTING BEAMS, ETC. ARE
OPTIONAL EQUIPMENT AND ARE NOT PROVIDED WITH THE MACHINE. ITEMS MUST BE
PURCHASED PRIOR TO MACHINE DELIVERY IF LIFTING WITH OVERHEAD/CRANE.
Upon arrival of
your machine, uncrate and immediately check for visible damage.
SHIPPING WEIGHT
SHIPPING DIMENSIONS OF MACHINE
8,377 # (Skidded/wrapped)
91" L x 91" W x 96" H (Skidded/wrapped)
See Makino Installation Manual for floor space requirements/dimensions – will vary depending upon the
options you purchase.
¾
Remove as much preservative from the machine as possible without having to power up (tables –
slides, pulleys, etc.). We recommend mineral spirits to clean. Apply oil when finished to prevent rust.
PLEASE FORWARD THIS TO THE APPROPRIATE PERSON. THANK YOU.
Summary of Contents for EDGE-2
Page 8: ...vi 3UH QVWDOODWLRQ XLGH...
Page 11: ...01_20ed3aSafety fm 3UH QVWDOODWLRQ XLGH 1 11 Installation Safety Instructions 1 25...
Page 12: ...3UH QVWDOODWLRQ XLGH NOTES SKETCHES...
Page 34: ...1 22 3UH QVWDOODWLRQ XLGH FIGURE 1 4 OILMATIC SAFETY LABELS...
Page 38: ...1 26 3UH QVWDOODWLRQ XLGH NOTES SKETCHES...
Page 63: ...02_20ed3a Specifications fm 2 23 3UH QVWDOODWLRQ XLGH NOTES SKETCHES...
Page 64: ...2 24 3UH QVWDOODWLRQ XLGH...
Page 74: ...3 8 3UH QVWDOODWLRQ XLGH NOTES SKETCHES...
Page 79: ...04_20ed3a Pre Delivery Prep fm 4 3 3UH QVWDOODWLRQ XLGH NOTES SKETCHES...
Page 87: ...04_20ed3a Pre Delivery Prep fm 4 11 3UH QVWDOODWLRQ XLGH NOTES SKETCHES...
Page 88: ...4 12 3UH QVWDOODWLRQ XLGH NOTES SKETCHES...
Page 103: ...05_20ed3a Machine Delivery fm 5 13 3UH QVWDOODWLRQ XLGH NOTES SKETCHES...
Page 104: ...5 14 3UH QVWDOODWLRQ XLGH NOTES SKETCHES...
Page 112: ...SSHQGL A 6 NOTES SKETCHES...
Page 120: ...SSHQGL A 14 NOTES SKETCHES...