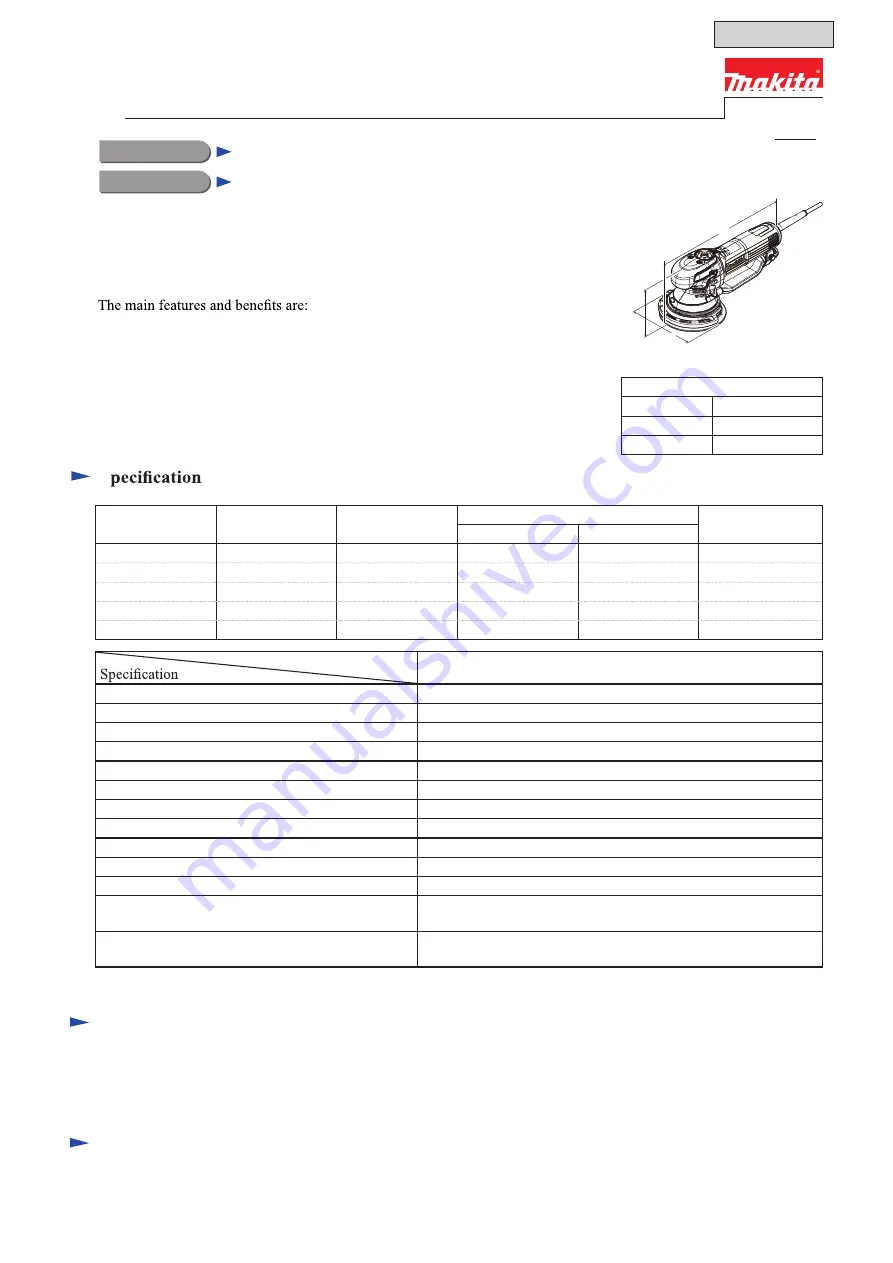
C
ONCEPT AND MAIN APPLICATIONS
BO6050 is a 150mm (6”) Random orbit sander developed as the successor to
the current model BO6040.
• Excellent operability thanks to the following:
- Toolless pad change
- Ergonomically designed soft palm grip
- Slim skirt
• Change lever protection system
S
Model
BO6050
Orbits per minute: opm= min
-1
1,600 - 6,800
Sanding strokes: spm= min
-1
3,200 - 13,600
Pad speed in Roto-orbit mode: rpm= min
-1
140 - 600
Paper fastening system
Hook & loop
Pad diameter: mm (")
ø150 (6)
Abrasive disc diameter: mm (")
ø150 (6)
Orbit diameter: mm (")
ø5.5 (7/32)
Pad brake
Yes
Variable speed control
Yes
Soft start
Yes
Constant speed control
Yes
Power supply cord: m (ft)
European countries: 4.0 (13.1), Australia, Brazil: 2.0 (6.6)
Other countries: 2.5 (8.2)
Weight according to
EPTA-Procedure 01/2003
*
1
: kg (lbs)
2.6 (5.7)
*1
With Dust nozzle
Dimensions: mm ( " )
Length (L)
330 (13)
Width (W)
155 (6-1/8)
Height (H)
145 (5-3/4)
L
W
H
Voltage (V)
Current (A)
Cycle (Hz)
Continuous Rating (W)
Max Output (W)
Input
Output
110
7.2
50/60
750
350
750
120
6.6
50/60
---
350
750
220
3.6
50/60
750
350
850
230
3.5
50/60
750
350
850
240
3.3
50/60
750
350
850
Abrasive disc 150-120
*
2
Dust nozzle
Side grip
Pad protector
Plastic carrying case
*2
for some countries only
Abrasive discs 150-40/60/80/120/180/240/400
Pad 150 (Soft, hard, super soft)
Pad 130 (Polishing)
Wool pad
Felt pad
Front cuffs 24
Front cuffs 22
S
tandard equipment
O
ptional accessories
T
ECHNICAL INFORMATION
PRODUCT
P 1/ 28
Model No.
Description
150mm (6") Random Orbit Sander
BO6050
November 2015
OFFICIAL USE
for ASC & Sales Shop