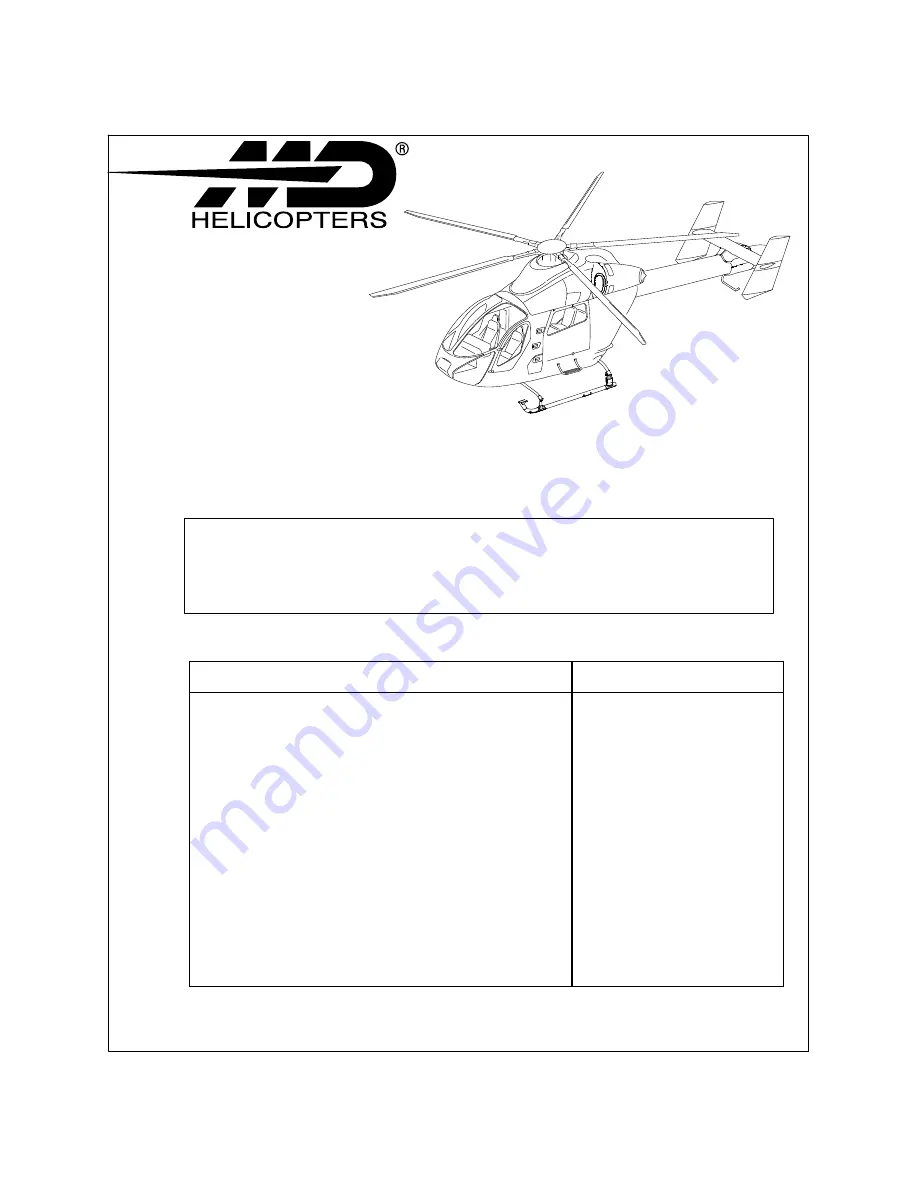
Log of EASA Revisions By Date
REVISION NUMBER AND DATE
EASA Approval Number
Revision 7
13 January 2003
. . . . . . . . . . . . . . .
2004-2053
Revision 8
8 July 2005
. . . . . . . . . . . . . . . . . . . .
2004-2053
TR6-001
5 June 2006
. . . . . . . . . . . . . . . . . . . . .
E02686
TR6-002
22 December 2006
. . . . . . . . . . . . . . . .
E02686
Revision 9
21 August 2007
. . . . . . . . . . . . . . . .
E02686
Revision 10
20 February 2008
. . . . . . . . . . . . .
E02686
Revision 11
11 April 2008
. . . . . . . . . . . . . . . . .
E02686
Reissue #1
2 December 2008
. . . . . . . . . . . .
E02686
Revision 1
21 July 2009
. . . . . . . . . . . . . . . . . . .
E02686
Reissue #2
6 November 2009
. . . . . . . . . . . .
E02686
Reissue #2
EASA
−
i
CSP
−
902RFM207E
−
1
As of 28 September 2003, the EASA began approving FAA rotorcraft
flight manuals. Operators of MD900 series helicopters registered in a
European Union member state are required to place this approval page
after the cover page in their flight manual.
European Aviation Safety Agency approved
Rotorcraft Flight Manual for Model MD900
(902 Configuration with PW 207E)
Summary of Contents for MD900 Explorer
Page 4: ......