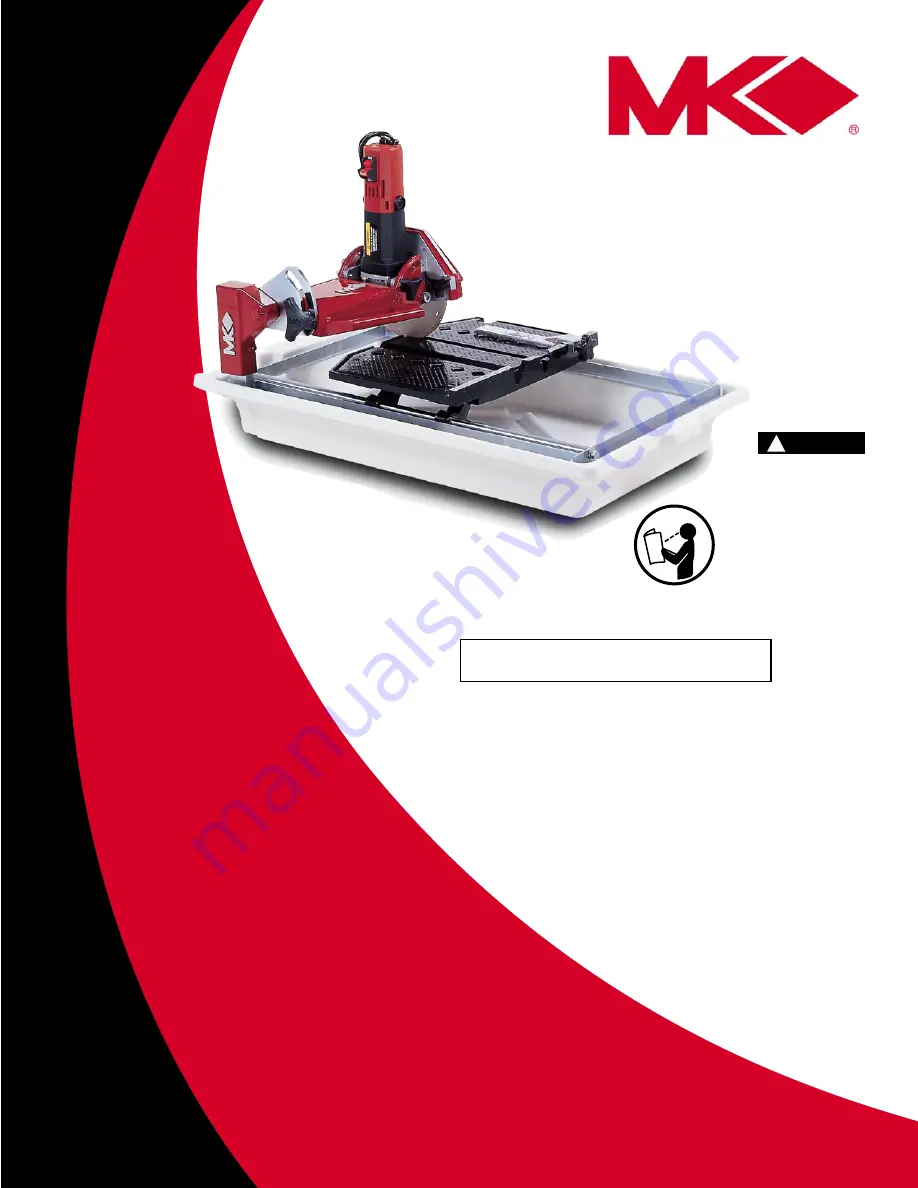
TILE SAW
OWNER’S MANUAL &
OPERATING INSTRUCTIONS
MK-370 EXP TILE SA
W
READ SAFETY
AND GENERAL
INSTRUCTIONS
CAREFULLY
BEFORE USING
SAW FOR THE
FIRST TIME
serial number
You should record the serial number
of your saw on this owner’s manual
and on the warrranty card, which must
be sent in, to be effective. be sure
to include all pertinent information
required.
Part No. 160084
Revision 12/03
CAUTION
!
O
W
N
E
R
S
M
A
N
U
A
L