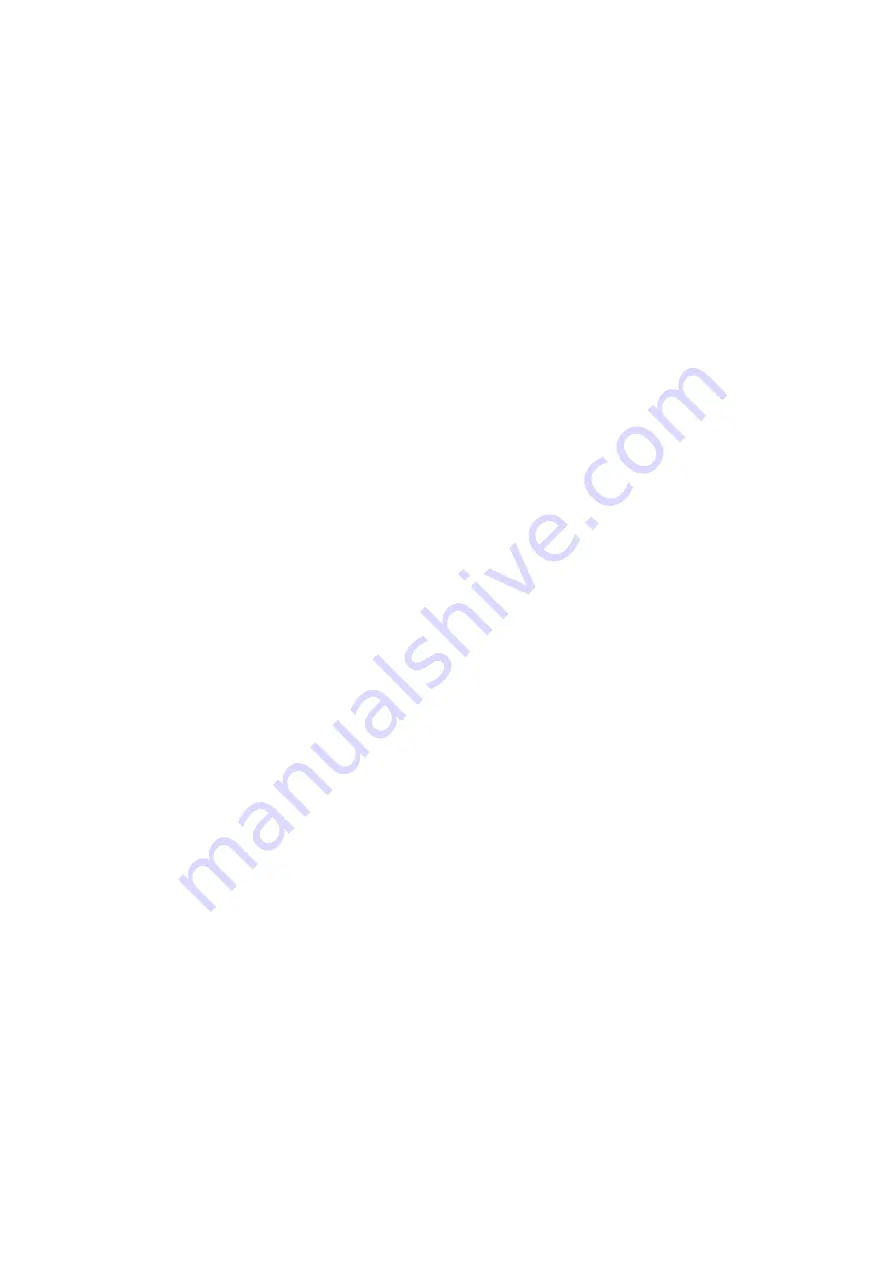
~1~
PREFACE
This manual offers all service specialists with the technological
procedures of maintenance, repairing for PA125
detailedly show
those whom may concern how to maintain, repair, change parts,
troubleshoot and reassemble, etc.
At every important section we illustrate by assembly, explosion
diagrams and photographs, if necessary, please check the diagrams
already shown.
Though we have tried our best, please kindly instruct us any
faults found in this manual.
MOTIVE POWER INDUSTRY CO., LTD.
Summary of Contents for PA125
Page 10: ... 10 B CHASSIS Steel ball steering Front brake fluid Front brake cam ...
Page 12: ......
Page 33: ...33 1 Lubrication System Lubrication System Diagram ...
Page 42: ...42 42 2 Engine dismantling A Dismantling engine B lnstalling engine ...
Page 63: ... 63 7 A C Generator A Dismantling AC generator B Installing AC generator ...
Page 92: ... 92 F Rear damper 1 Rear damper disassembling diagram ...
Page 99: ... 99 3 Recharge system 1 Recharge system diagram ...
Page 103: ... 103 5 Starting system 1 Starting wiring ...