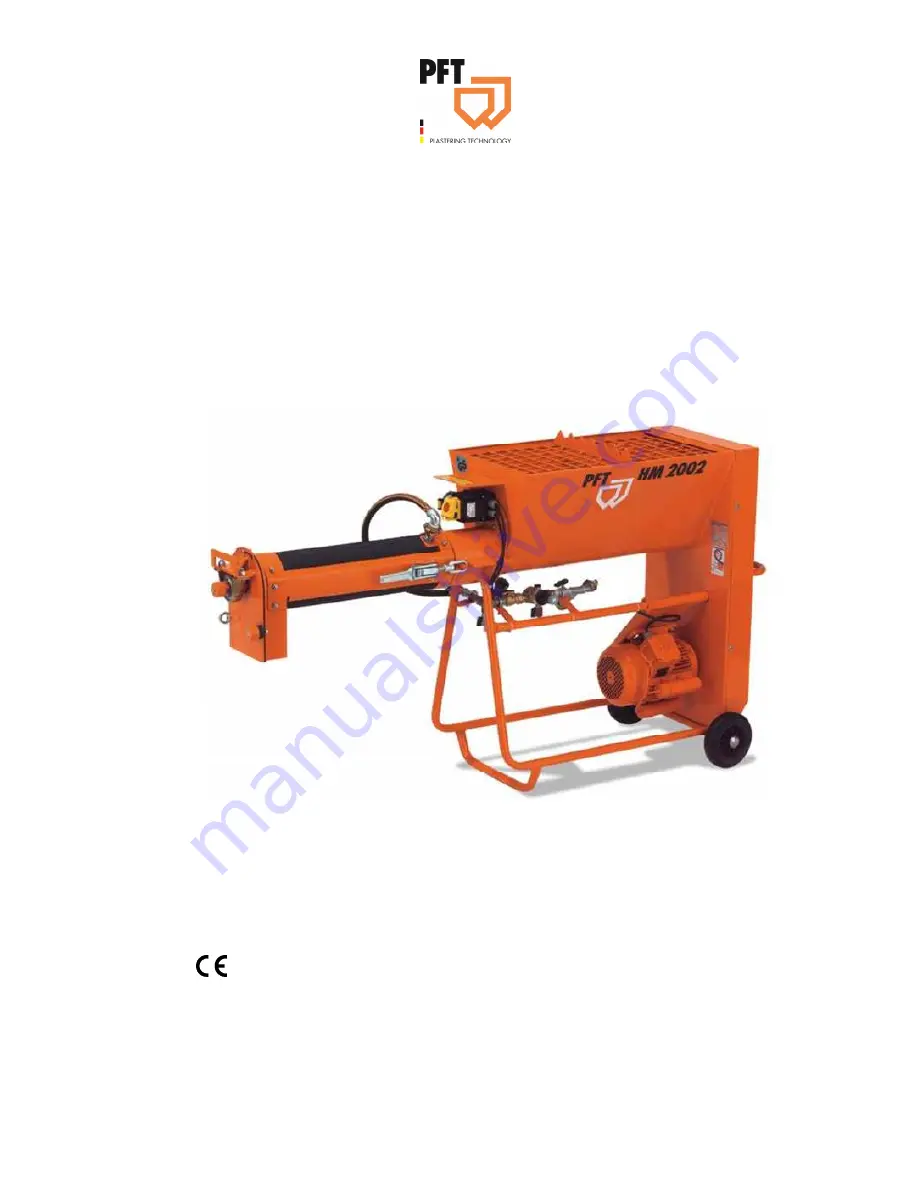
Table of Contents
2017-03-14
Operating manual
PFT continuous mixer HM 2002
Overview - Operation - Spare parts lists
Article number of the operating manual: 20 09 98 59
HM 2002 article number 20 54 60 03
HM 2002 with rubber mixing tube article number 00 02 04 73
HM 2002 rubber mixing tube 2.2 KW 120 V 60 Hz 1 Phase article number 00 59 33 59
Read the operating manual prior to starting any work!