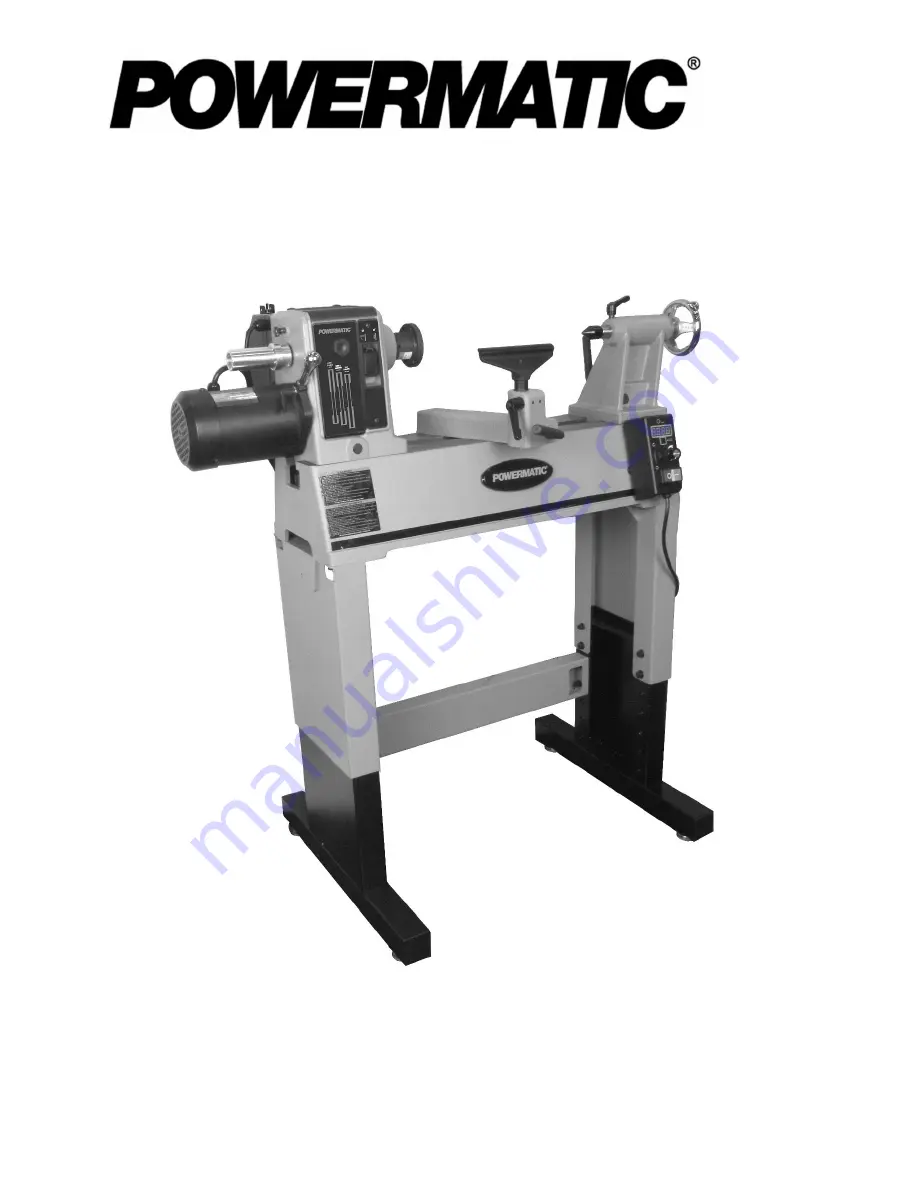
Powermatic
427 New Sanford Road
LaVergne, Tennessee 37086
Part No. M-1792014
Ph.: 800-274-6848
Edition 1 11/2019
www.powermatic.com Copyright © 2019 Powermatic
Operating Instructions and Parts Manual
20
”
x14
”
Benchtop
Woodturner’s Lathe
Model PM2014
Shown with optional stand #1792014S
(ordered separately)
This .pdf document is bookmarked
Summary of Contents for PM2014
Page 27: ...27 15 1 1 PM2014 Headstock Assembly Exploded View ...
Page 30: ...30 15 2 1 PM2014 Bed Toolrest and Tailstock Assemblies Exploded View ...
Page 35: ...35 16 0 Electrical connections PM2014 Lathe cont next page ...
Page 36: ...36 cont ...
Page 38: ...38 This page intentionally left blank ...
Page 39: ...39 This page intentionally left blank ...
Page 40: ...40 427 New Sanford Road LaVergne Tennessee 37086 Phone 800 274 6848 www powermatic com ...