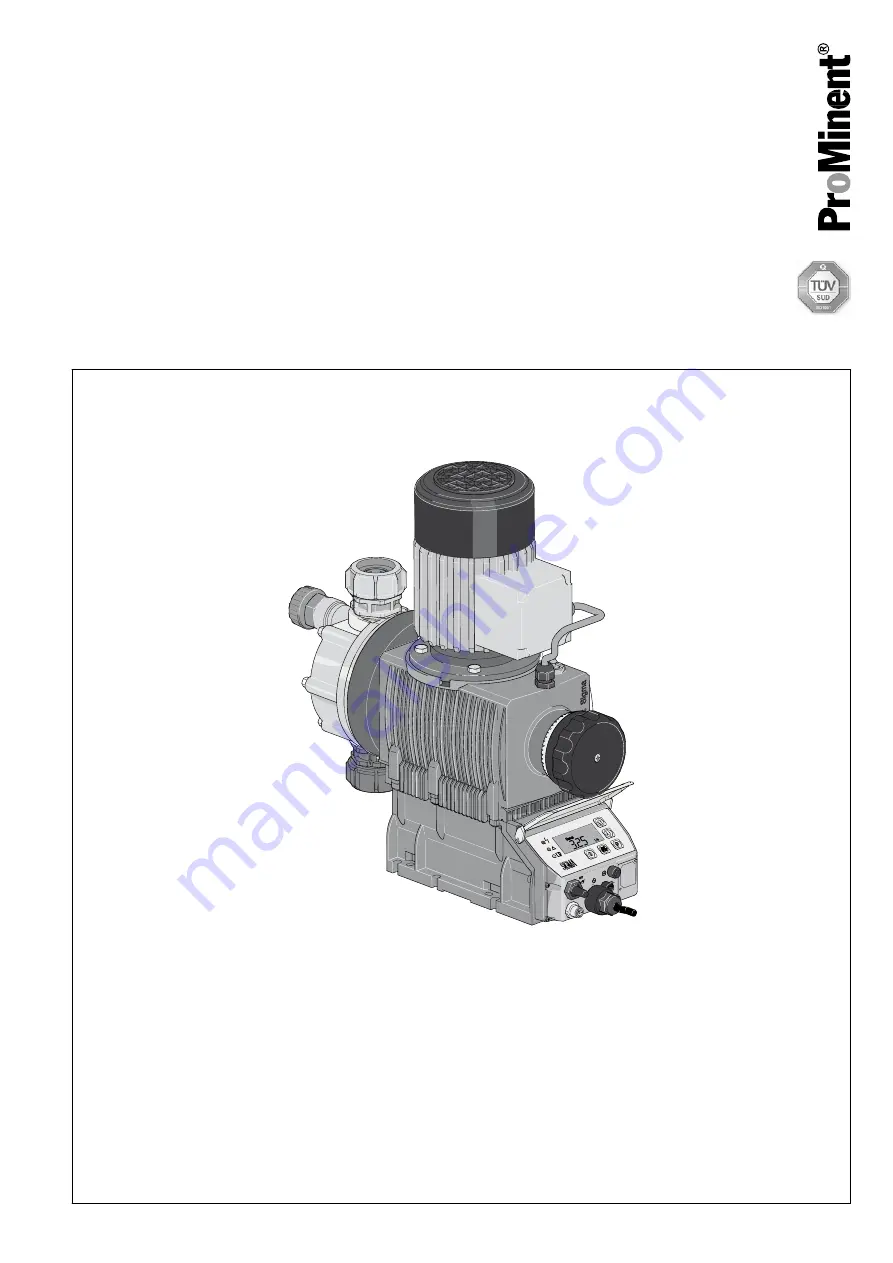
Diaphragm Motor-Driven Metering Pump
Sigma/ 2 Control Type S2Ca
Operating instructions
PK_2_115
Two sets of operating instructions are required for the safe, correct and proper operation of the metering pumps: The
product-specific operating instructions and the "General Operating Instructions for ProMinent
®
motor-driven metering
pumps and hydraulic accessories".
Both sets of operating instructions are only valid when read together.
Original Operating Instructions (2006/42/EC)
Part no. 985894
BA SI 040 05/11 EN
Please carefully read these operating instructions before use! · Do not discard!
The operator shall be liable for any damage caused by installation or operating errors!
Technical changes reserved.