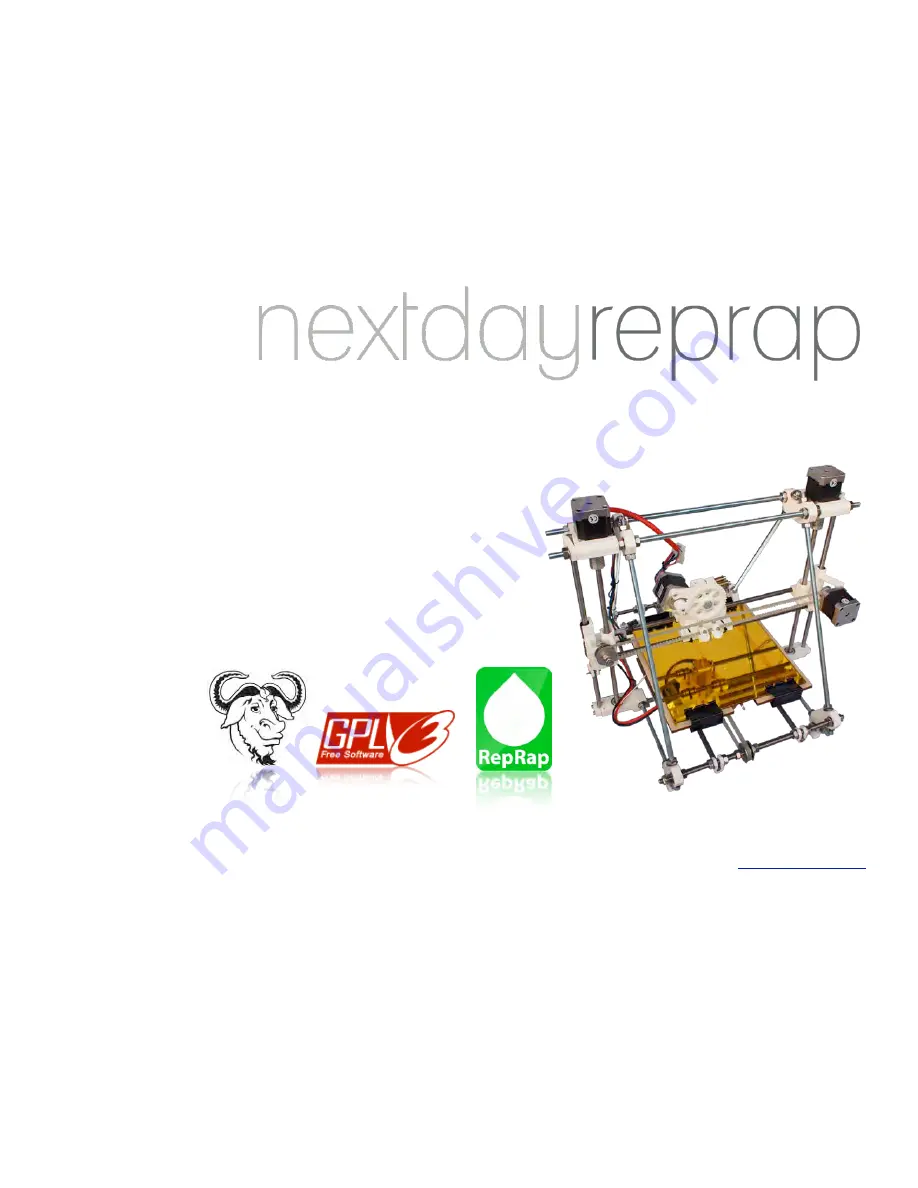
Copyright 2012 NextDayReprap All registered trademarks belong to their respective owners, any unauthorized copying and redistribution is strictly prohibited. E&OE
LM8UU Prusa Mendel Build Manual
The programs supplied and referenced in this manual are free software: you can redistribute them and/or modify them under the terms of the GNU General Public License
as published by the Free Software Foundation, either version 3 of the License, or (at your option) any later version. These programs are distributed in the hope that they will
be useful, but WITHOUT ANY WARRANTY; without even the implied warranty of MERCHANTABILITY or FITNESS FOR A PARTICULAR PURPOSE. See the GNU General
Public License for more details. You should have received a copy of the GNU General Public License along with these programs. If not, see
http://www.gnu.org/licenses/
.