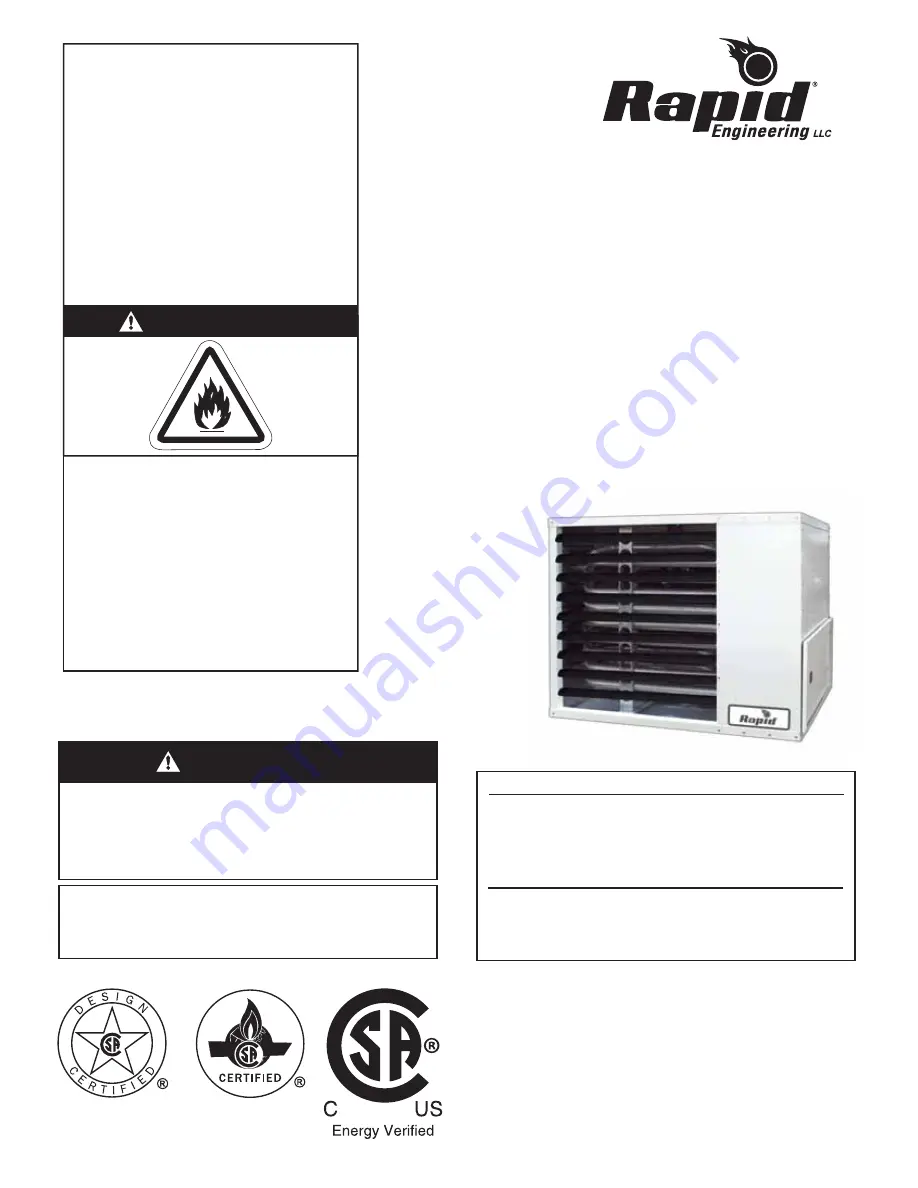
P/N RP111101NA 11/14 Rev. J
WARNING
FOR YOUR SAFETY
If you smell gas:
1. Open windows.
2. DO NOT try to light any appliance.
3. DO NOT use electrical switches.
4. DO NOT use any telephone in
your building.
5. Extinguish any open flame.
6. Leave the building.
7. Immediately call your local gas
supplier after leaving the building.
Follow the gas supplier’s
instructions.
8. If you cannot reach your gas
supplier, call the Fire Department.
Fire Hazard
Keep all flammable objects, liquids and
vapors the minimum required clear-
ances to combustibles away from
heater.
Some objects will catch fire or explode
when placed close to heater.
Failure to follow these instructions can
result in death, injury or property
damage.
WARNING
Installation must be done by a contractor qualified
in the installation and service of gas-fired heating
equipment or your gas supplier.
Improper installation, adjustment, alteration, service
or maintenance can result in death, injury or
property damage. Read the Installation, Operation
and Service Manual thoroughly before installing or
servicing this equipment.
Installer
Please take the time to read and understand
these instructions prior to any installation.
Installer must give a copy of this manual to the owner.
Owner
Keep this manual in a safe place in order to provide
your service technician with necessary information.
Rapid Engineering LLC
1100 Seven Mile Road NW
Comstock Park, MI 49321
Telephone: +1.616.784.0500
Fax: +1.616.784.1910
Toll Free: 800.536.3461
www.rapidengineering.com
© 2014 Rapid Engineering LLC
Installation, Operation
& Service Manual
Models UHA[T][M][X][S]
150, 175, 200, 225
250, 300, 350, 400
UHA-Series
Tubular Unit Heaters
(Standard Range)
Summary of Contents for UHAM 150
Page 2: ......
Page 4: ......
Page 8: ......
Page 50: ...UHA STANDARD UNIT HEATER INSTALLATION OPERATION AND SERVICE MANUAL 42 of 59 14 1 General ...
Page 65: ...SECTION 16 SPECIFICATIONS 57 of 59 16 4 Dimension Data for Models UHA T M X S 300 400 ...
Page 68: ......
Page 69: ......
Page 70: ......
Page 71: ......
Page 72: ......