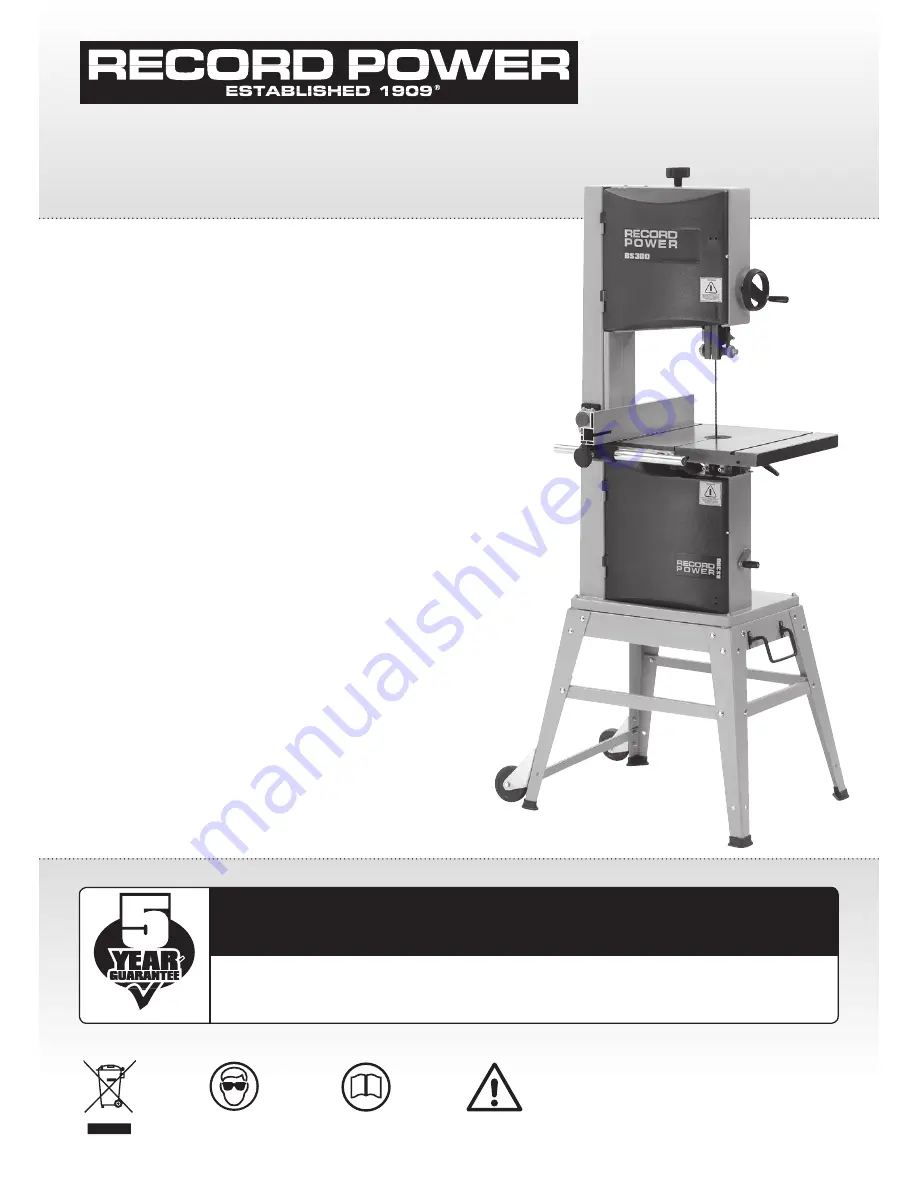
Original Instruction Manual
BS300E
Premium
12" Bandsaw
Always wear safety glasses when
using woodworking equipment.
Always read the instructions
provided before using
woodworking equipment.
i
Kg
Version 3.0
January 2013
To register this product please visit
www.recordpower.info
It is important to register your product as soon as possible in order to receive efficient after sales
support and be entitled to the full
5 year guarantee
. Your statutory rights are not affected.
Please see back cover for contact details.
Important
For your safety read instructions carefully
before assembling or using this product.
Save this manual for future reference.
i
Kg
Summary of Contents for BS300E Premium
Page 33: ...33 13 Parts Diagrams cont ...
Page 34: ...34 13 Parts Diagrams cont ...
Page 35: ...35 13 Parts Diagrams cont ...