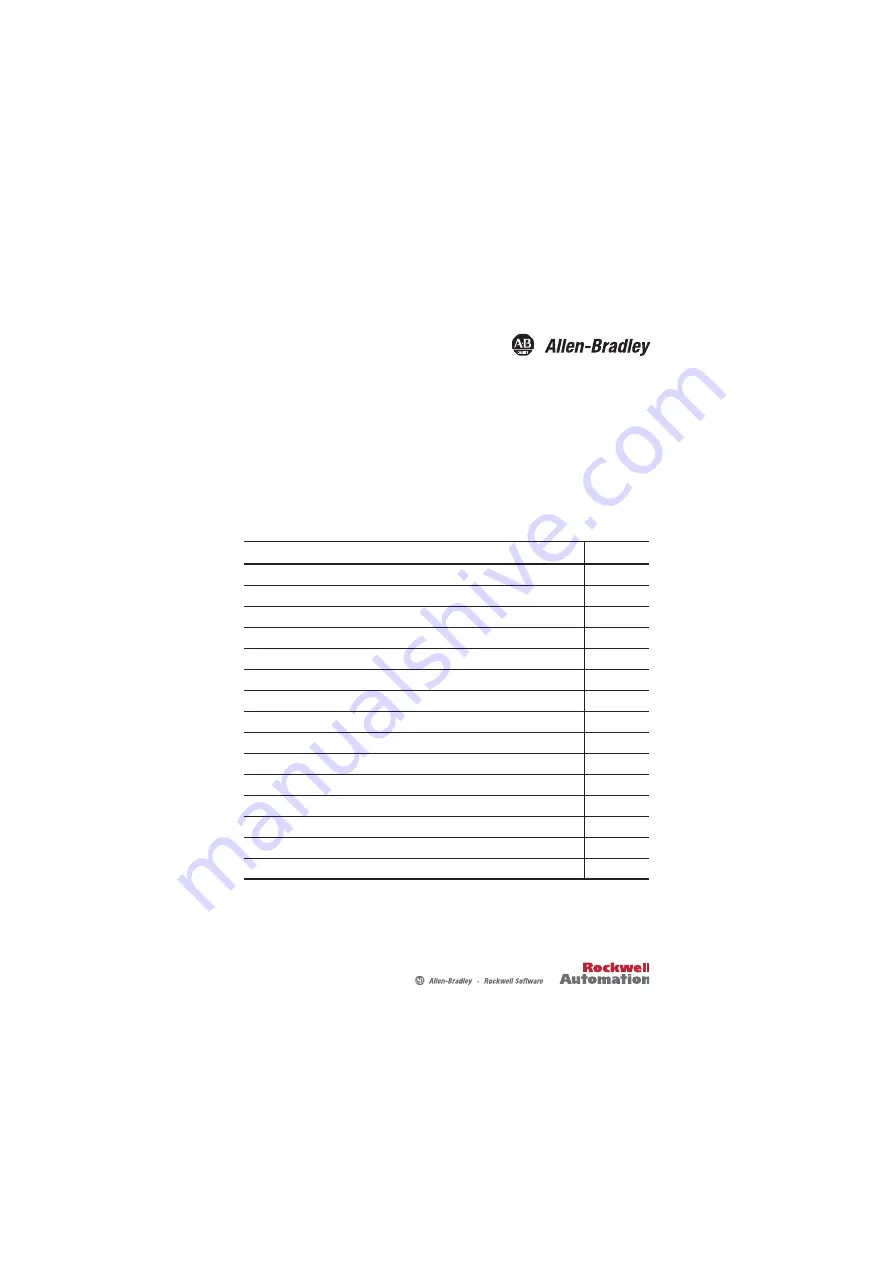
Installation Instructions
POINT I/O 5V DC and 24V DC Very High
Speed Counter Module
Catalog Numbers 1734-VHSC5, 1734-VHSC24, Series C
Table of Contents
Topic
Page
Important User Information
2
Environment and Enclosure
3
Preventing Electrostatic Discharge
3
North American Hazardous Location Approval
4
European Hazardous Location Approval
5
Additional Resources
6
About the Module
6
Install the Mounting Base
8
Install the Module
8
Install the Removable Terminal Block
10
Remove a Mounting Base
11
Wire the Module
12
Communicate with Your Module
13
Interpret Status Indicators
20
Specifications
22