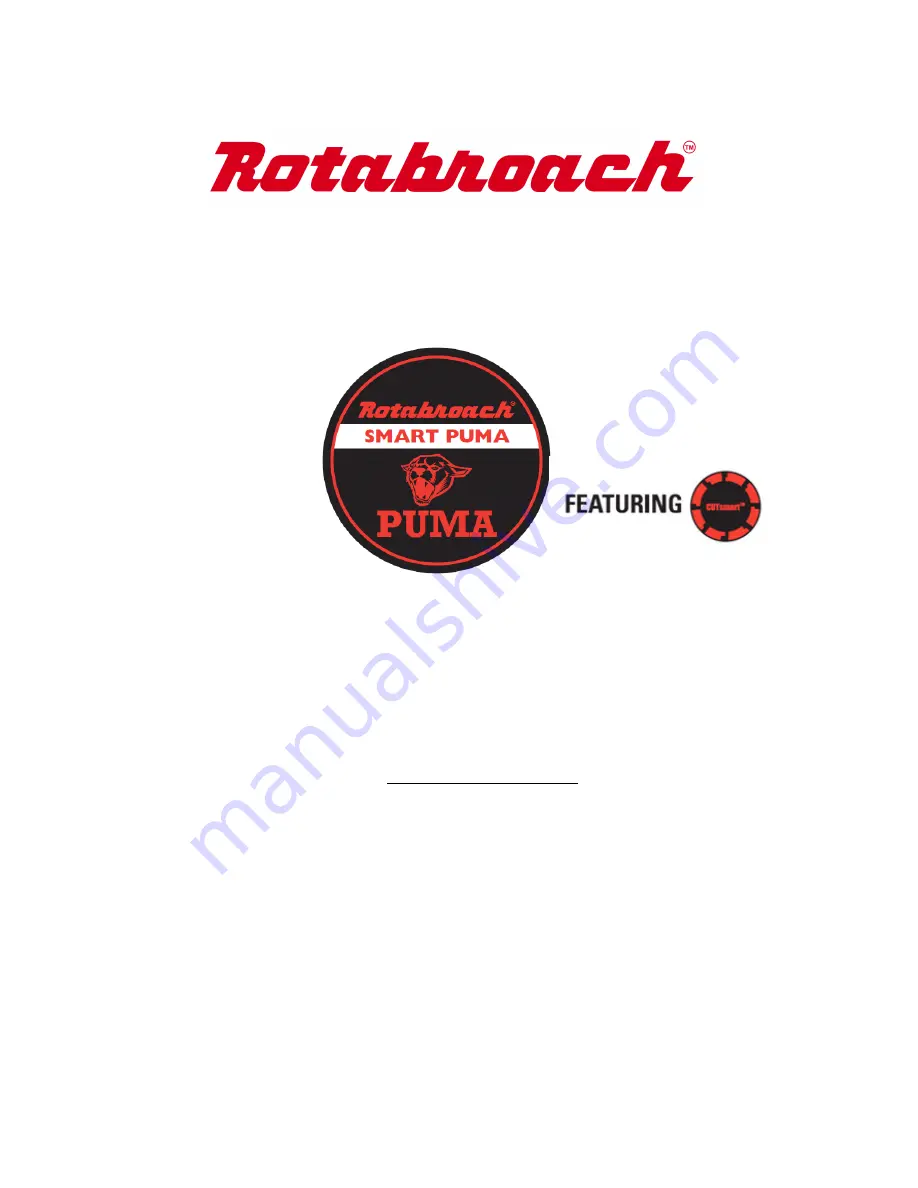
Issue 5
Original version
Nov 2014
1
PUMA MAGNETIC DRILLING MACHINE
Model No. SMARTPUMA1 & SMARTPUMA3
This machine (Serial No
) is CE approved.
Rotabroach Ltd
Imperial Works, Sheffield Road
Sheffield, South Yorkshire
United Kingdom
S9 2YL
Tel: +44 (0) 114 2212 510
Fax: +44 (0) 114 2212 563
Email: sales@rotabroach.co.uk
Web site: www.rotabroach.co.uk