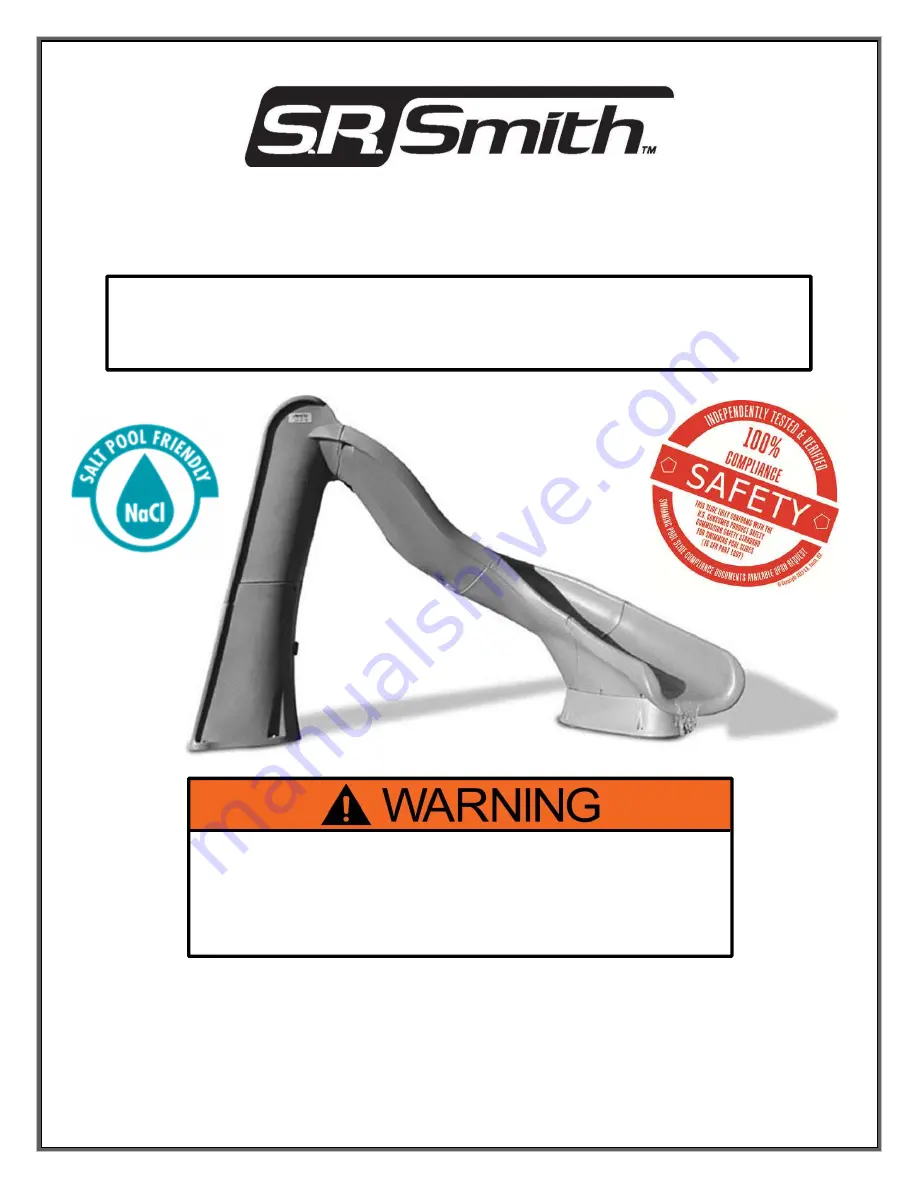
06-693
June16
TURBOTWISTER®
ASSEMBLY AND INSTALLATION
INSTRUCTIONS
SRS AUSTRALIA, PTY LTD
12 Enterprise St
Richlands QLD 4077
Australia
Phone 07 3812 2283 • Fax 07 3812 1187
www.srsmith.com/au
S.R. SMITH, LLC
CORPORATE HEADQUARTERS
P.O. Box 400 • 1017 S.W. Berg Parkway
Canby, Oregon 97013
USA
Phone (503) 266 2231 • Fax (503) 266 4334
www.srsmith.com
S.R. SMITH TURBOTWISTER SLIDES ARE MANUFACTURED FOR
INSTALLATION AND USE ON RESIDENTIAL INGROUND SWIMMING
POOLS ONLY. THE TURBOTWISTER IS NEVER TO BE INSTALLED AND
USED ON ABOVEGROUND POOLS, ONGROUND POOLS, HOUSEBOATS,
BOAT DOCKS, FLOATING DOCKS OR PLATFORMS OR OTHER BODIES
OF WATER SUCH AS LAKES, PONDS, RIVERS, ETC.