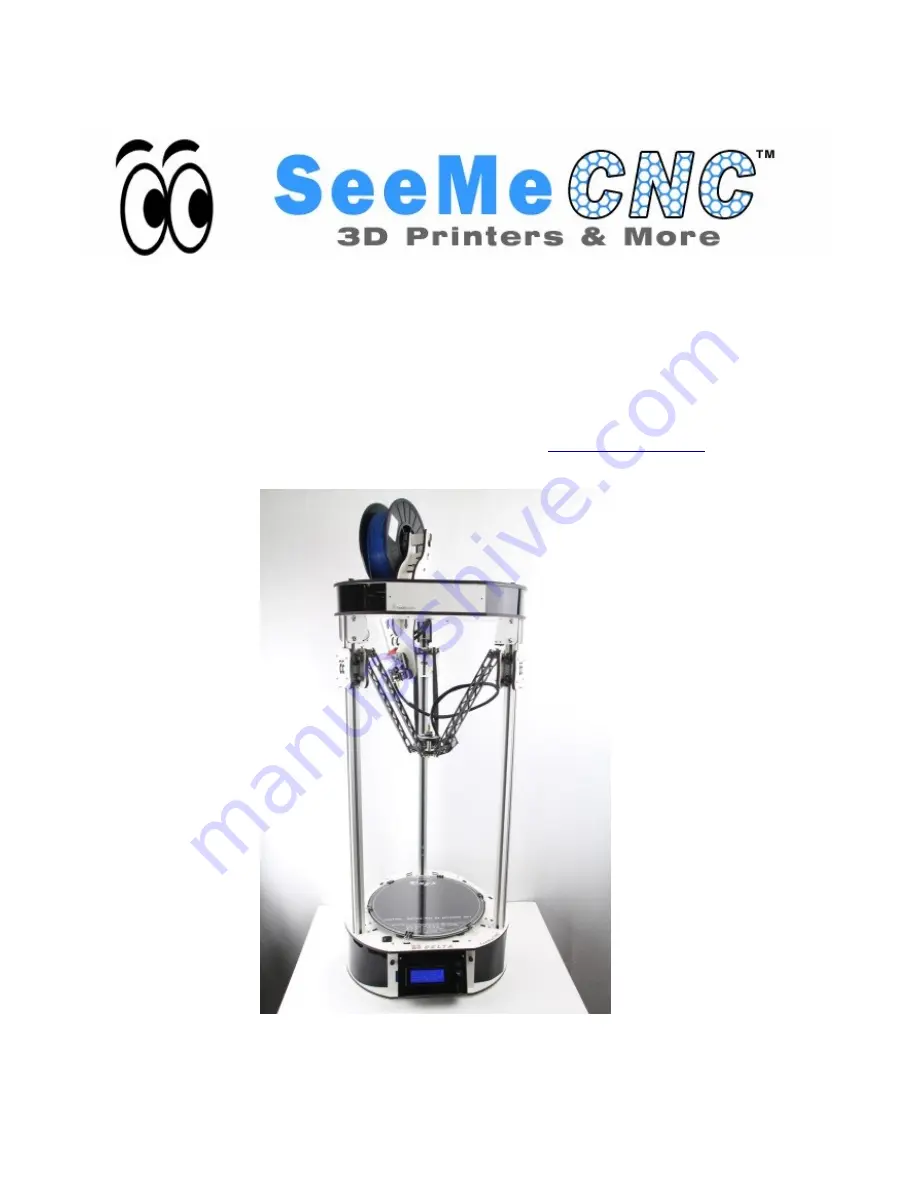
Rostock MAX v2 Assembly Guide – 4thEd.
Welcome to the Assembly Guide for the Rostock MAX v2.0 3D printer.
Version 4.47, September 28
th
, 2016
Fourth Edition
Copyright 2016 by Gene Buckle
Licensed as Creative Commons Attribution-ShareAlike 3.0
Questions or corrections should be emailed to
geneb@deltasoft.com
– 1